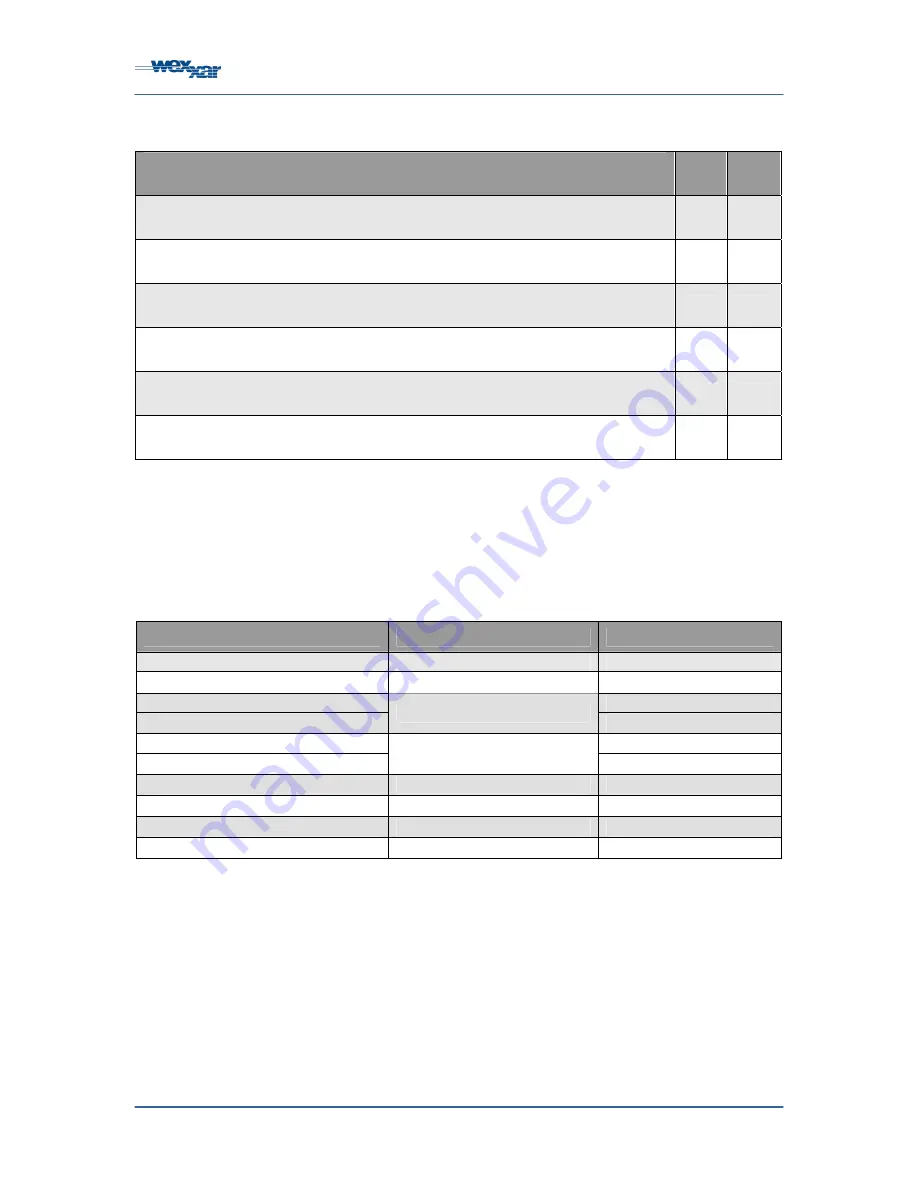
WF-10T
Case Former
Operating Procedures
6-42
Check the ‘S’ box for Satisfactory Performance and ‘US’ box for Unsatisfactory Performance.
Table 5: Preliminary Start-up Checklist
Machine Start-up
Preliminary checks
S
US
Check if the machine is set up for the right case size.
Check if the machine is properly loaded.
Check if the air pressure is set correctly to 90 PSI, with the manual
shutoff valve open.
Verify that all guard doors are closed and that all personnel are clear.
Verify that the electrical power disconnect switch is turned
ON
and that
the
‘EMERGENCY STOP’
button in the
OUT
position.
Check if the tape applicator is properly installed, loaded with a tape roll,
and ready to go.
6.2.2 Start-up Procedures
After completing the procedures outlined in Section 6.2.1:
, start the machine
as follows:
1) Press
the
‘RESET’
button once. Air pressure will now be applied to the various machine
mechanism cylinders. The remaining mechanisms move to their respective
HOME
positions as follows:
Table 6: Mechanism HOME Positions and Valve Numbers
Mechanism
HOME Position
Valve Number
Case Separator Valve
DOWN
V1
Injector Valve
UP
V2
Carriage Back Valve
V3A
Carriage Forward Valve
Carriage BACK
V3B
Jaws Cylinder Retracted Valve
V4A
Jaws Cylinder Extended Valve
CLOSED
V4B
Carriage Up/Down Valve
DOWN
V5
Minor Folder Raise/Lower Valve
DOWN
V6
Major Folder On/Off Valve
OFF
V7
Conveyor Motor
OFF
N/A
2) Check that the conveyor side-belts are tracking properly. They should be centered on
the drive pulley, properly tensioned, and in reasonably good condition.
Содержание WF-10T
Страница 2: ...WF 10T Case Former ...
Страница 118: ...WF30T Case Former Appendix A MSDS Geralyn FMG 387 106 ...
Страница 119: ...WF30T Case Former Appendix A MSDS Geralyn FMG 387 107 ...
Страница 120: ...WF30T Case Former Appendix A MSDS Geralyn FMG 387 108 ...
Страница 121: ...WF30T Case Former Appendix A MSDS Geralyn FMG 387 109 ...
Страница 122: ...WF30T Case Former Appendix A MSDS Geralyn FMG 387 110 ...
Страница 123: ...WF30T Case Former Appendix A MSDS Geralyn FMG 387 111 ...
Страница 125: ...WF 10T Case Former Appendix B Keystone Nevastane HT 2 113 ...
Страница 126: ...WF 10T Case Former Appendix B Keystone Nevastane HT 2 114 ...
Страница 127: ...WF 10T Case Former Appendix B Keystone Nevastane HT 2 115 ...
Страница 128: ...WF 10T Case Former Appendix B Keystone Nevastane HT 2 116 ...
Страница 129: ...WF 10T Case Former Appendix B Keystone Nevastane HT 2 117 ...