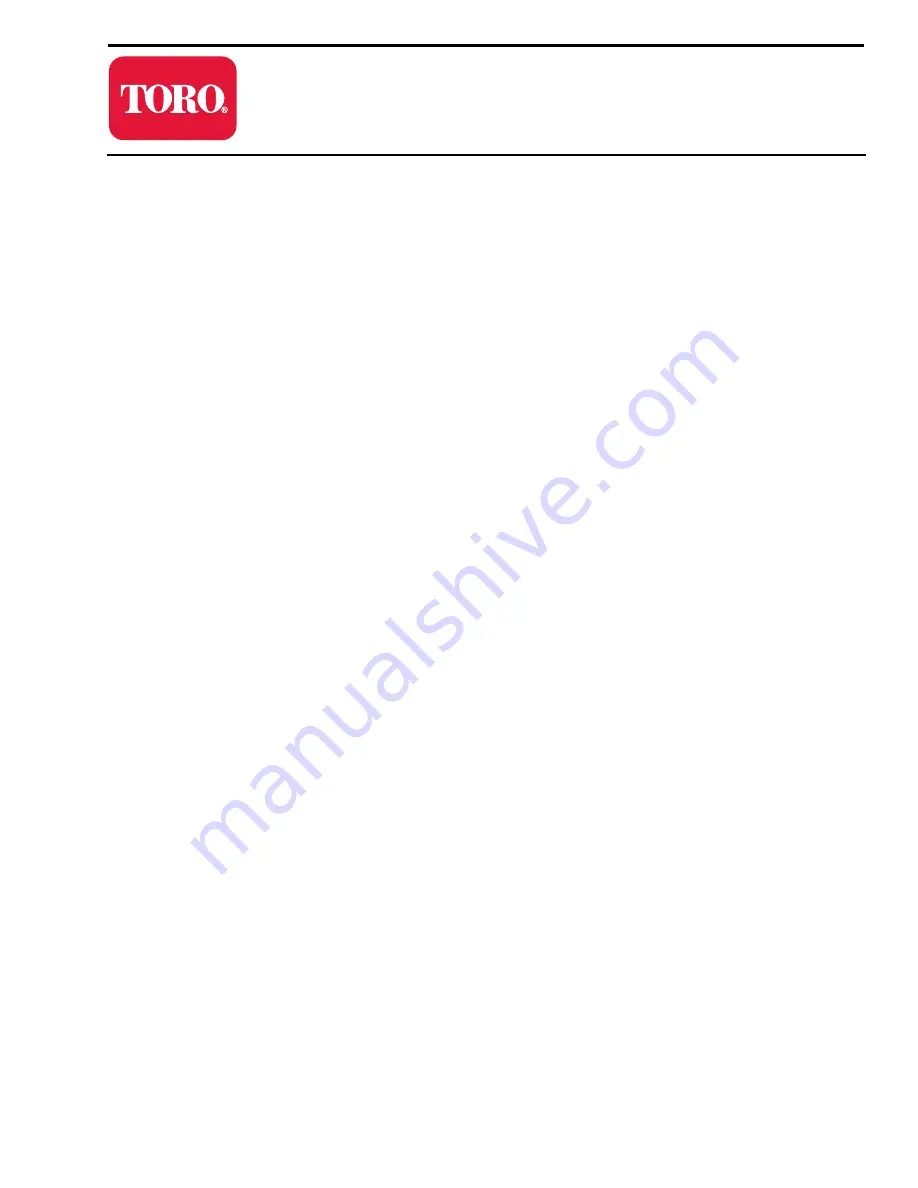
Chapter 9
Universal Groomer (Optional)
Table of Contents
The Gear Box Assembly .................................................................................................................... 9–4
The Idler Assembly ............................................................................................................................ 9–9
The Groomer Reel ........................................................................................................................... 9–11
The Height Adjuster Assembly ......................................................................................................... 9–14
The Grooming Brush (Optional) ....................................................................................................... 9–16
Greensmaster
®
1018/1021/1026
Page 9–1
Universal Groomer (Optional)
18238SL Rev B
Содержание Greensmaster 1018
Страница 4: ...NOTES NOTES Page 4 Greensmaster 1018 1021 1026 18238SL Rev B ...
Страница 6: ...g264048 Figure 1 Model 04830 shown Preface Page 6 Greensmaster 1018 1021 1026 18238SL Rev B ...
Страница 104: ...Electrical System Component Testing Page 6 12 Greensmaster 1018 1021 1026 18238SL Rev B ...
Страница 162: ...DPA Cutting Units Service and Repairs Page 8 28 Greensmaster 1018 1021 1026 18238SL Rev B ...
Страница 179: ......