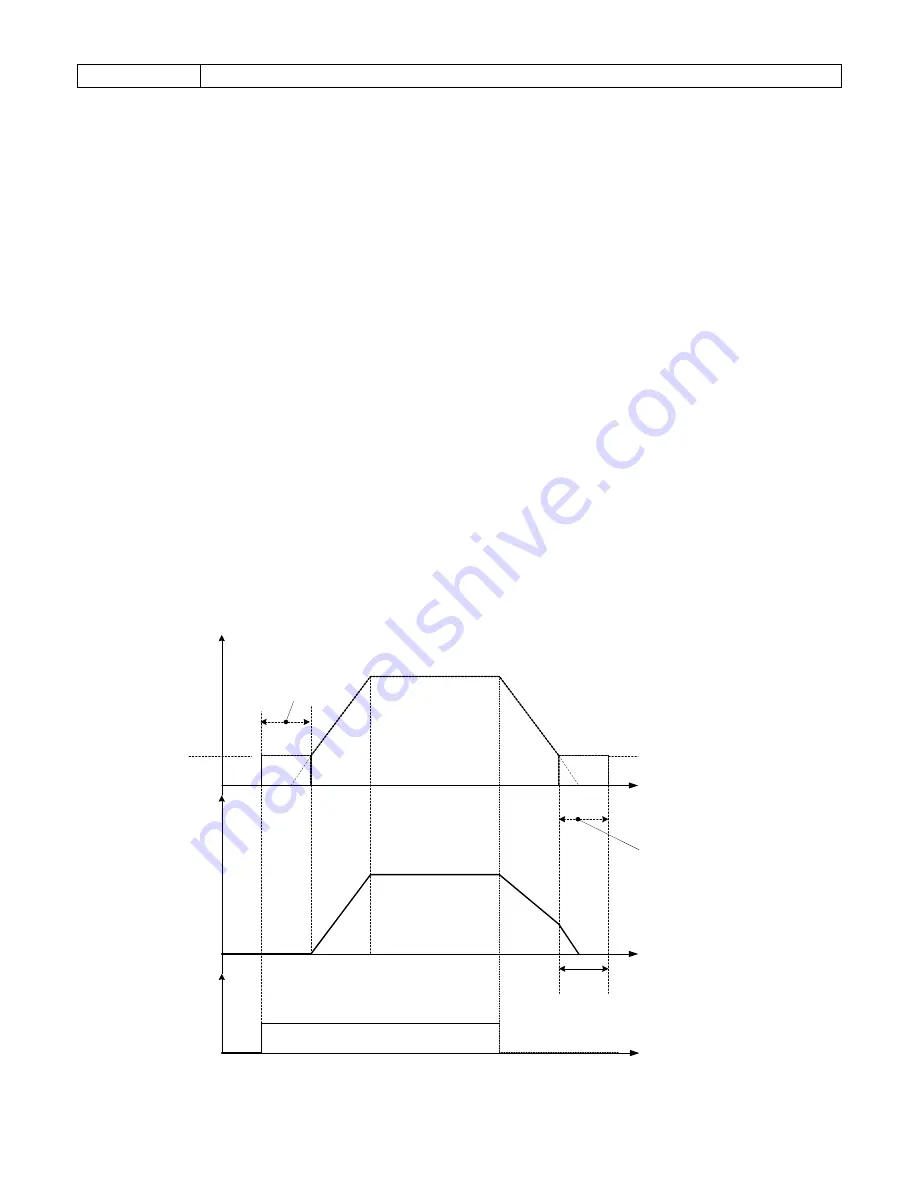
4-188
Range
0.00~10.00 Sec
Duration of DC injection braking during a start operation. DC injection braking at start is disabled when parameter
07-16 is set to 0 sec.
DC Injection Braking Operation
When DC Injection braking is active DC voltage is applied to the motor, increasing the braking current and
resulting in an increase in the strength of the magnetic field trying to lock the motor shaft.
To enable DC injection braking during a start operation set the DC injection braking current (07-07) and the DC
injection braking time (07-16) at start to a value greater than 0. DC injection braking at start can be used to
prevent “wind milling effect” in fan applications.
To enable DC injection braking during a stop operation set the DC injection braking current (07-07) and the DC
injection braking time at stop (07-08) to a value greater than 0.
Notes:
- When parameter 07-16 is set to 0 sec. the inverter will start from the minimum output frequency.
- Increasing the DC braking time (07-08, 07-16) can reduce the motor stop time.
- Increasing the DC braking current (07-07) can reduce the motor stop time.
- During stop operation: If the DC braking start frequency < minimum output frequency (01-08), DC braking
is activated when the output frequency reaches the minimum output frequency level.
- DC Injection braking cannot be used in sensor vector control (SV).
For DC braking operation, please refer to Figure 4.4.57.
t
07-06
07-08
07-16
01-08
(Fmin)
Braking
time
The larger value of
01-08 or 07-06
Output
Frequency
Motor
Speed
Run
Command
t
t
Figure 4.4.57 DC braking operation
Содержание A510
Страница 25: ...3 11 Step 3 Make wire connections and place cover back Step 4 Fasten screw ...
Страница 38: ...3 24 690V 100 150HP 460V 125HP Power supply 690V 100 150HP M10 Terminal screw size T M10 M10 ...
Страница 45: ...3 31 3 690V 175HP 270HP ...
Страница 160: ...4 85 Frequency Reference Output Frequency 100 00 12 00 13 100 Figure 4 4 6 Frequency reference upper and lower limits ...