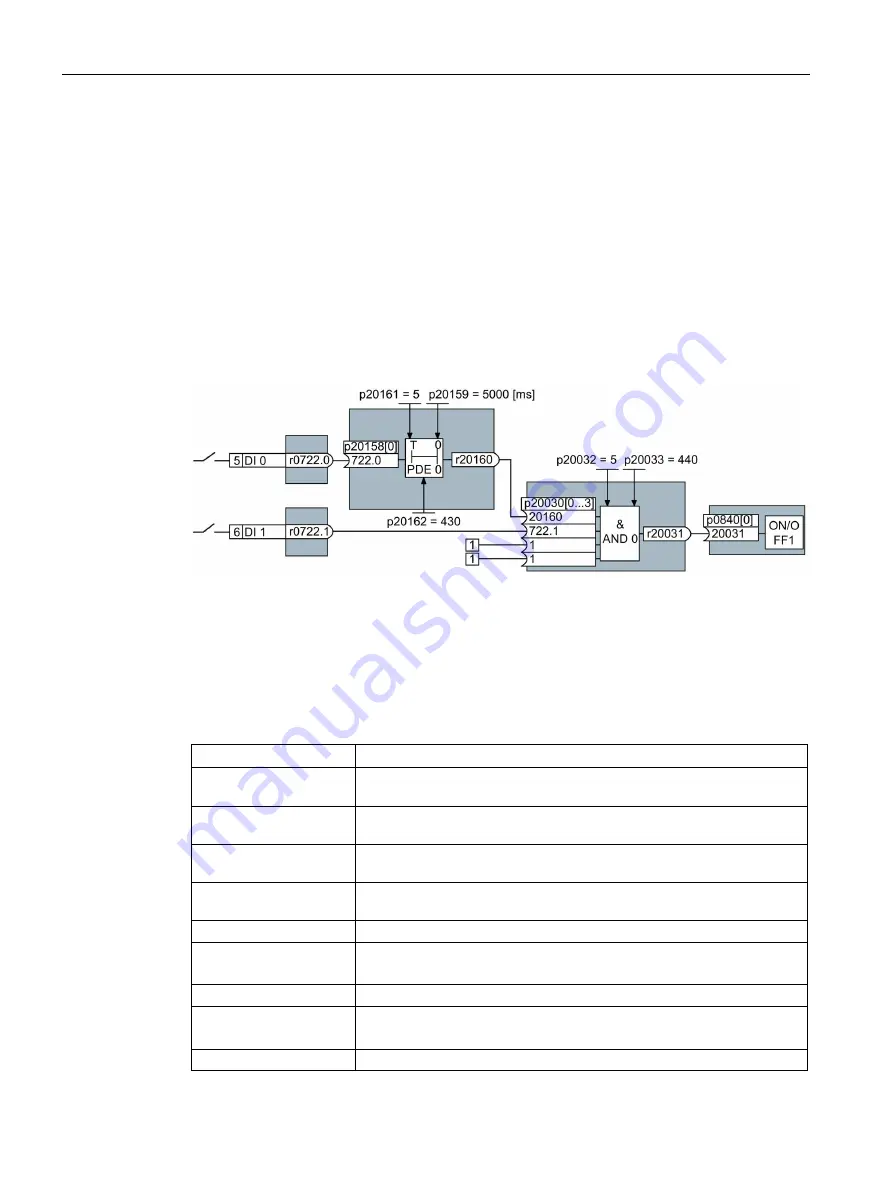
Appendix
A.4 Interconnecting signals in the inverter
Converter with control units CU250D-2
370
Operating Instructions, 04/2015, FW V4.7.3, A5E34261542B AB
A.4.2
Example
Moving a basic control logic into the inverter
A conveyor system is to be configured in such a way that it can only start when two signals
are present simultaneously. These could be the following signals, for example:
●
The oil pump is running (the required pressure level is not reached, however, until after 5
seconds)
●
The protective door is closed
To implement this task, you must insert free function blocks between digital input 0 and the
command to switch on the motor (ON/OFF1).
Figure A-5 Example: Signal interconnection for control logic
The signal of digital input 0 (DI 0) is fed through a time block (PDE 0) and is interconnected
with the input of a logic block (AND 0). The signal of digital input 1 (DI 1) is interconnected to
the second input of the logic block. The logic block output issues the ON/OFF1 command to
switch-on the motor.
Setting the control logic
Parameter
Description
p20161 = 5
The time block is enabled by assigning to runtime group 5 (time slice of
128 ms)
p20162 = 430
Run sequence of the time block within runtime group 5 (processing before
the AND logic block)
p20032 = 5
The AND logic block is enabled by assigning to runtime group 5 (time
slice of 128 ms)
p20033 = 440
Run sequence of the AND logic block within runtime group 5 (processing
after the time block)
p20159 = 5000.00
Setting the delay time [ms] of the time module: 5 seconds
p20158 = 722.0
Connect the status of DI 0 to the input of the time block
r0722.0 = Parameter that displays the status of digital input 0.
p20030[0] = 20160
Interconnect the timer block to the 1st input of the AND
p20030[1] = 722.1
Interconnect the status of DI 1 with the 2nd AND input
r0722.1 = Parameter that displays the status of digital input 1.
p0840 = 20031
Interconnect the AND output to ON/OFF1