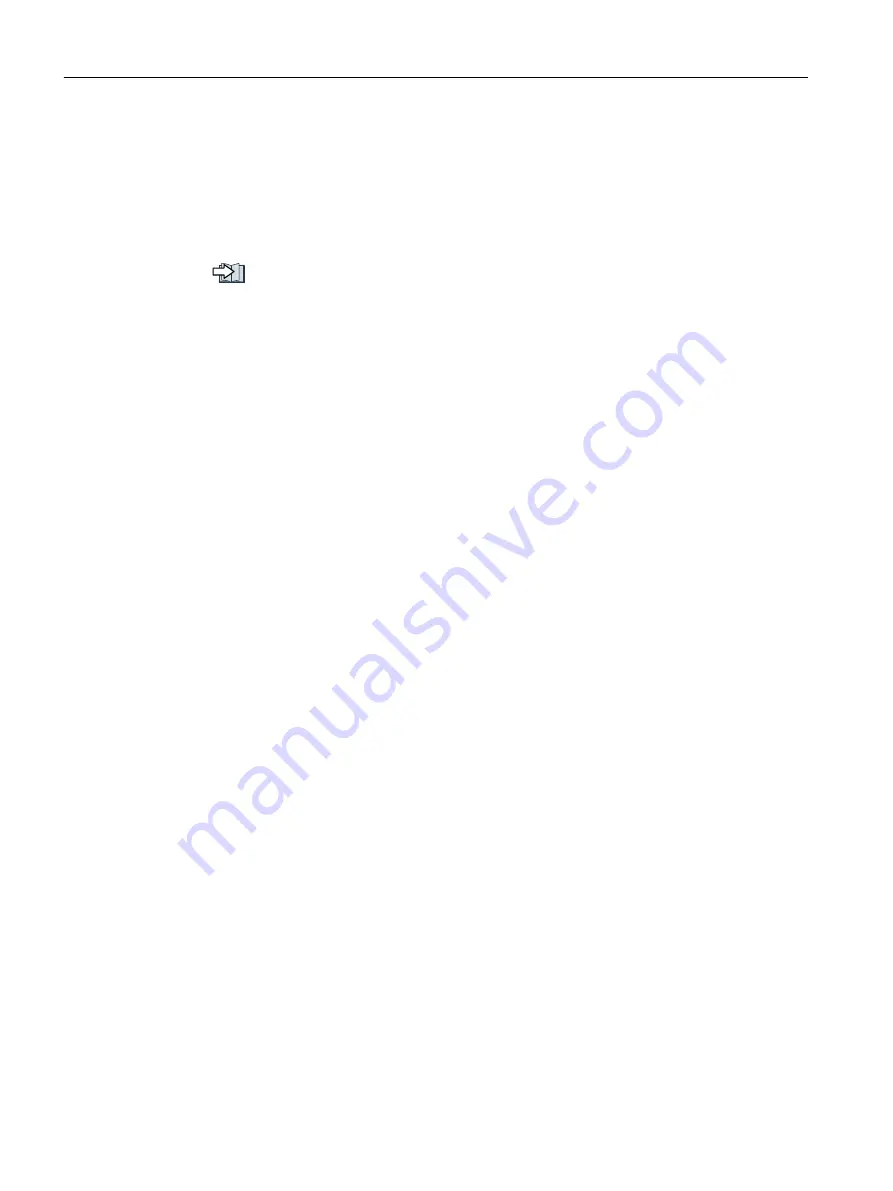
Documentation of the inverter
The following must be documented for the inverter:
● The results of the acceptance test.
● The settings of the integrated drive safety functions.
The STARTER commissioning tool logs the settings of the integrated drive functions, if
necessary.
Documentation for acceptance (Page 413)
The documentation must be signed.
Who may perform the acceptance test of the inverter?
Personnel from the machine manufacturer, who, on account of their technical qualifications
and knowledge of the safety functions, are in a position to perform the acceptance test in the
correct manner are authorized to perform the acceptance testing of the inverter.
Commissioning
5.17 Acceptance tests for the safety functions
Safety Integrated - SINAMICS G110M, G120, G120C, G120D and SIMATIC ET 200pro FC-2
210
Function Manual, 01/2017, FW V4.7 SP6, A5E34261271B AD