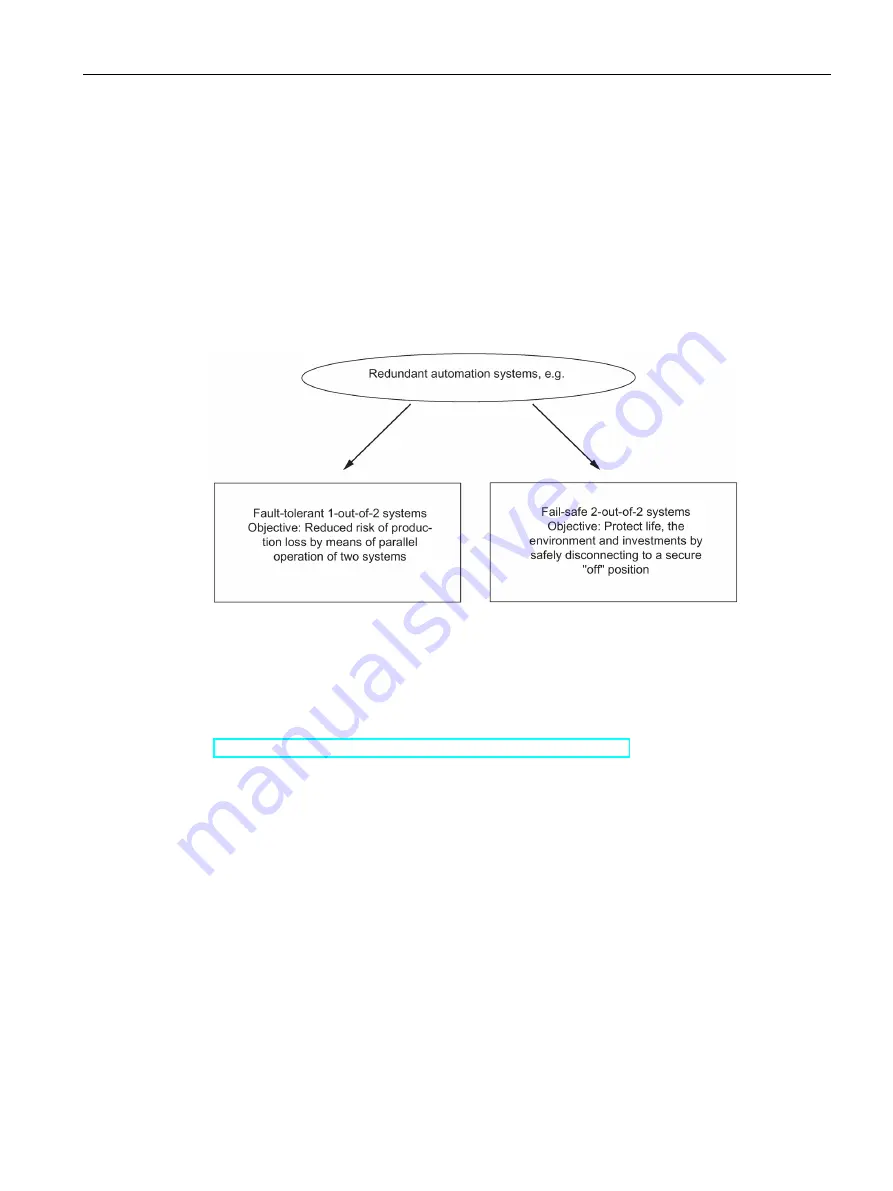
I/O configuration variants
6.3 Fault-tolerant automation systems (redundancy operation)
CPU 410 Process Automation/CPU 410 SMART
System Manual, 05/2017, A5E31622160-AC
61
6.3
Fault-tolerant automation systems (redundancy operation)
6.3.1
Redundant SIMATIC automation systems
Operating objectives of redundant automation systems
Redundant automation systems are used in practice with the aim of achieving a higher
degree of availability or fault tolerance.
Figure 6-3
Operating objectives of redundant automation systems
Note the difference between fault-tolerant and fail-safe systems.
The S7-400H is a fault-tolerant automation system. You may only use the S7-400H to
control safety-related processes if you have programmed it and assigned its parameters in
accordance with the rules for F-systems. You can find information on this in following
manual: SIMATIC Industrial Software S7 F/FH Systems
http://support.automation.siemens.com/WW/view/en/2201072
Why fault-tolerant automation systems?
The purpose of using fault-tolerant automation systems is to reduce production downtimes,
regardless of whether the failures are caused by an error/fault or are due to maintenance
work.
The higher the costs of production stops, the greater the need to use a fault-tolerant system.
The generally higher investment costs of fault-tolerant systems are soon recovered since
production stops are avoided.
Redundant I/O
Input/output modules are termed redundant when they exist twice and they are configured
and operated as redundant pairs. The use of redundant I/O provides the highest degree of
availability, because the system tolerates the failure of a CPU or of a signal module.