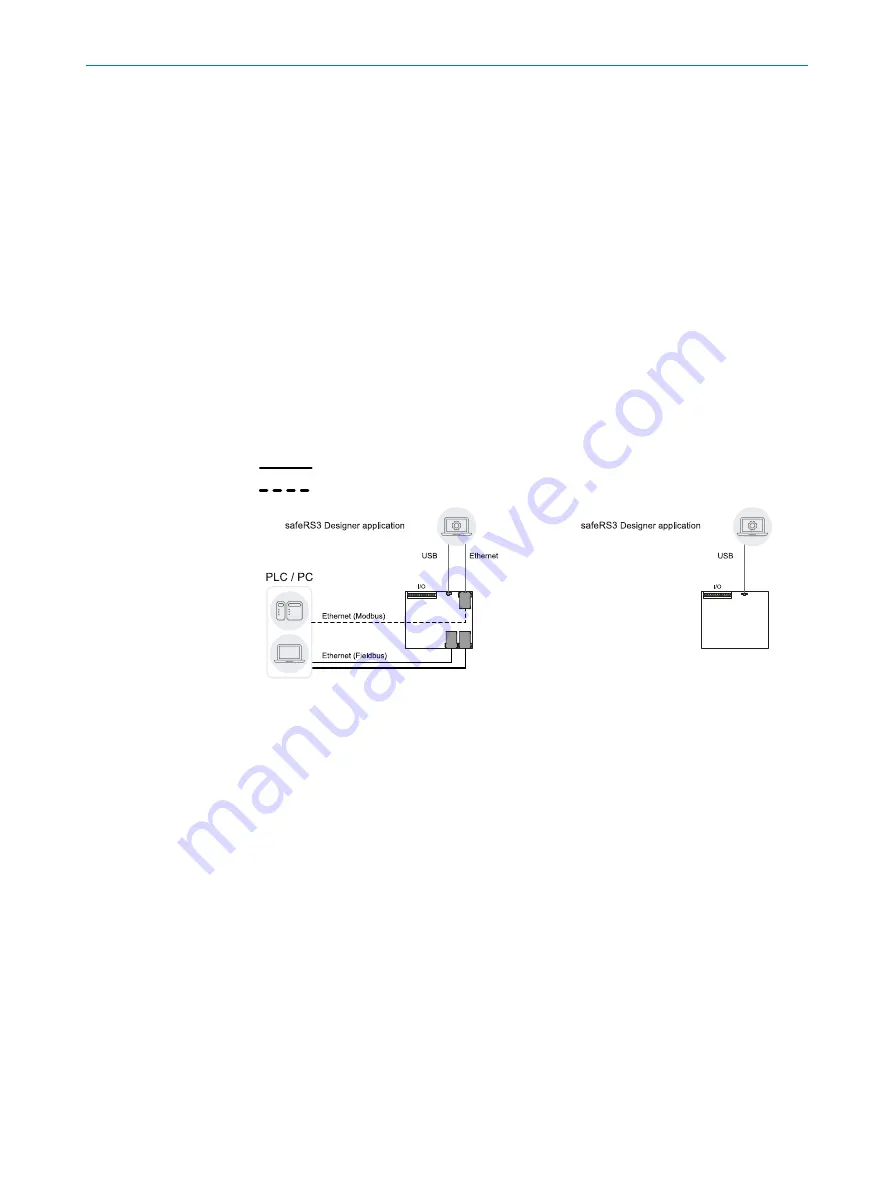
20
O P E R A T I N G I N S T R U C T I O N S | safeRS3
8027489/2022-03-01 | SICK
Subject to change without notice
4 GET TO KNOW SAFERS3
deactivated, so the control system can put the area into a safe condition and/or prevent
restarting of the machinery.
In the absence of other control systems, safeRS3 can be connected to the devices that
control the power supply or machinery start-up.
safeRS3 does not perform normal machinery control functions.
For connection examples, see
Electrical connections on page 104
4.2
safeRS3 controls
4.2.1
Control supported
The safeRS3 supports two different controls. The main difference between them are the
connection ports and therefore the communication interfaces available:
l
safeRS3 Control PROFINET: two Ethernet ports for Fieldbus, an Ethernet port for
system configuration and Modbus communication and a micro-USB port
l
safeRS3 Control I/O: a micro-USB port
Safe
Unsafe
safeRS3 Control PROFINET communication
architecture.
safeRS3 Control I/O communication
architecture.
4.2.2
Functions
The control performs the following functions:
l
Collects information from all the sensors via CAN bus.
l
Compares the position of detected motion with the set values.
l
Deactivates the selected safety output when at least one sensor detects motion in
the protective field.
l
Deactivates all the safety outputs if a failure is detected in one of the sensors or the
control.
l
Manages the inputs and outputs.
l
Communicates with the safeRS3 Designer application for all configuration and
diagnostic functions.
l
Allows dynamically switching between different configurations.