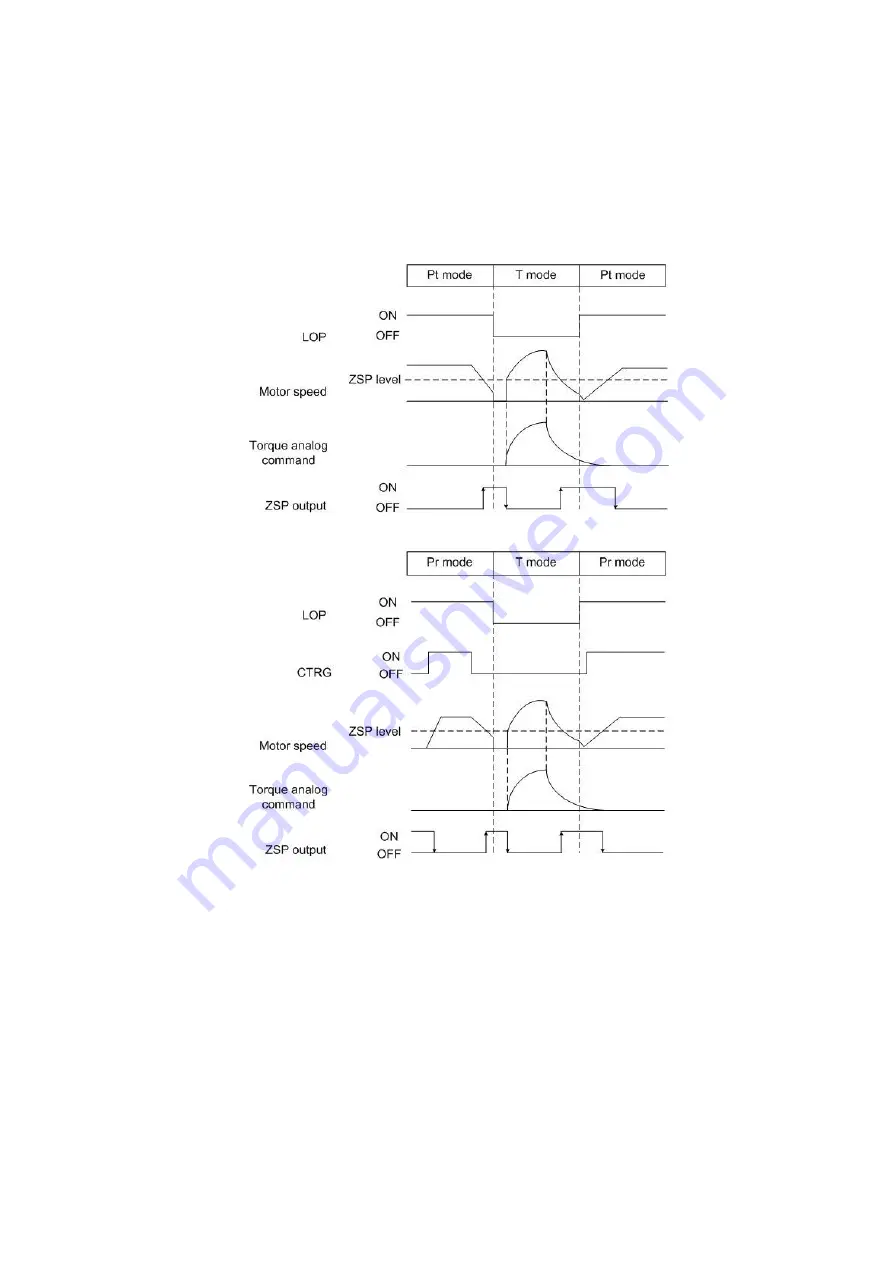
156
6.8.3.
Torque/Position control mode switch
This hybrid mode is divided into 2 types: T/Pt and T/Pr. Users could set the PA01 as 1005h (T/Pt
mode) or 1015h (T/Pr mode). The switch could not be performed if the motor is at a high speed rotation.
It could be switched as the zero speed detection output signal is ON. Users could use the pin function
LOP of DI to switch these 2 modes. When the position mode with inner register command is wanted,
the state of CTRG signal must be turned on. The sequence chart is presented in the figure below.
It is recommended that users switch torque to position mode after the motor is static.
Содержание SDE Series
Страница 13: ...5 1 6 Function block diagram ...
Страница 26: ...18 3 3 3 CN1 pin name list ...
Страница 212: ...204 SDE 075A2U SDE 100A2U 750W 1KW unit mm Dimensions of the servo drive may be revised without prior notice ...
Страница 223: ...215 SME L040 SME L075 SME L100 SME L150 ...
Страница 224: ...216 SME L200 SME L300 SME M100 SME M150 Continuous running range ...
Страница 225: ...217 SME M200 SME M300 NOTE These characteristic plots above are measured in case of 3φ 200 240V power supplied ...
Страница 227: ...219 ...
Страница 231: ...223 4 Wiring example with peripheral equipment CN2 Encoder socket ...
Страница 242: ...234 12 4 Version information Version V1 01 Issue date Aug 2017 Proofreader Yaochou Shu ...