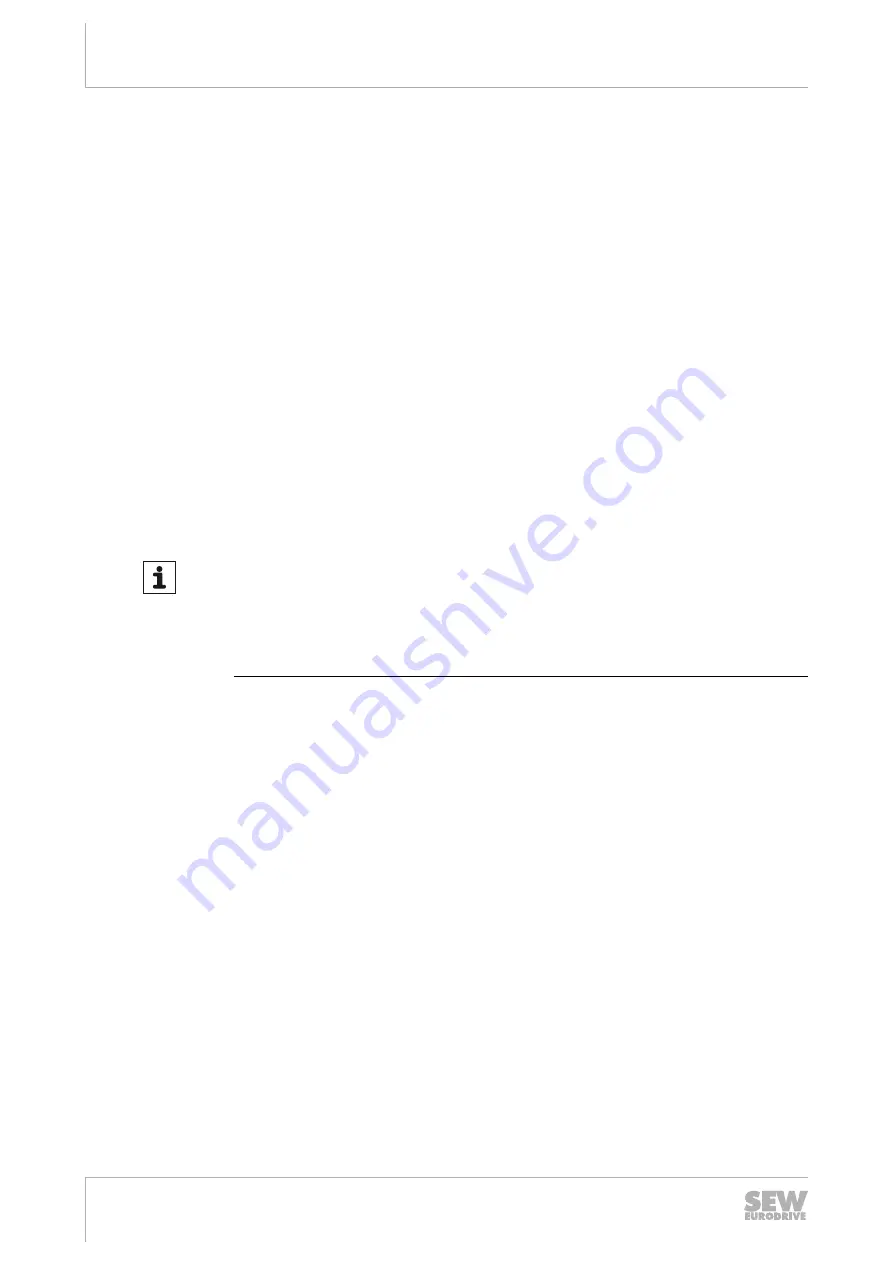
10
Project planning
Recommendations for motor and inverter selection
Operating Instructions – MOVIMOT
®
flexible
274
10.5.3
Motor selection for asynchronous motors
The mechanical resistance of the motor against the overload, which might exceed the
permitted limit values, must be strictly checked.
M
pk
and n
base
depend on the motor/inverter combination, as well as on the used control
mode.
Asynchronous motors are mainly operated in control mode VFC
PLUS
. The control mode
efficiently adjusts the motor magnetization to the respective operating point. It simul-
taneously allows for dynamic responses to load shocks at the drive train.
10.5.4
Asynchronous motors in control mode VFC
PLUS
The control mode VFC
PLUS
without encoder allows for dynamic use of the entire speed
range of the drive. Reversing and moving through the rotational speed 0 are also pos-
sible.
However, continuous operation of asynchronous motors without encoder at low
speeds is not possible. The minimum speeds that must not be permanently undercut
during operation without encoder are:
•
Motor mode: 1% of the asynchronous motor nominal speed.
•
Regenerative operation: 10% of the asynchronous motor nominal speed.
INFORMATION
Lifting application with encoder
The control must be designed in such a way that the direction of rotation of the drive
can only be reversed when it is at a standstill (with the brake applied).
If the direction of rotation should be changed without standstill, a motor encoder must
be used.
The described restrictions do not apply in control mode VFC
PLUS
with encoder. In com-
parison to operation without encoder, higher dynamic properties can be achieved with
an encoder.
When determining the maximum speed, observe that the breakdown torque M
K
is re-
duced in an quadratic relationship in the field weakening range.
29129451/EN – 12/2019