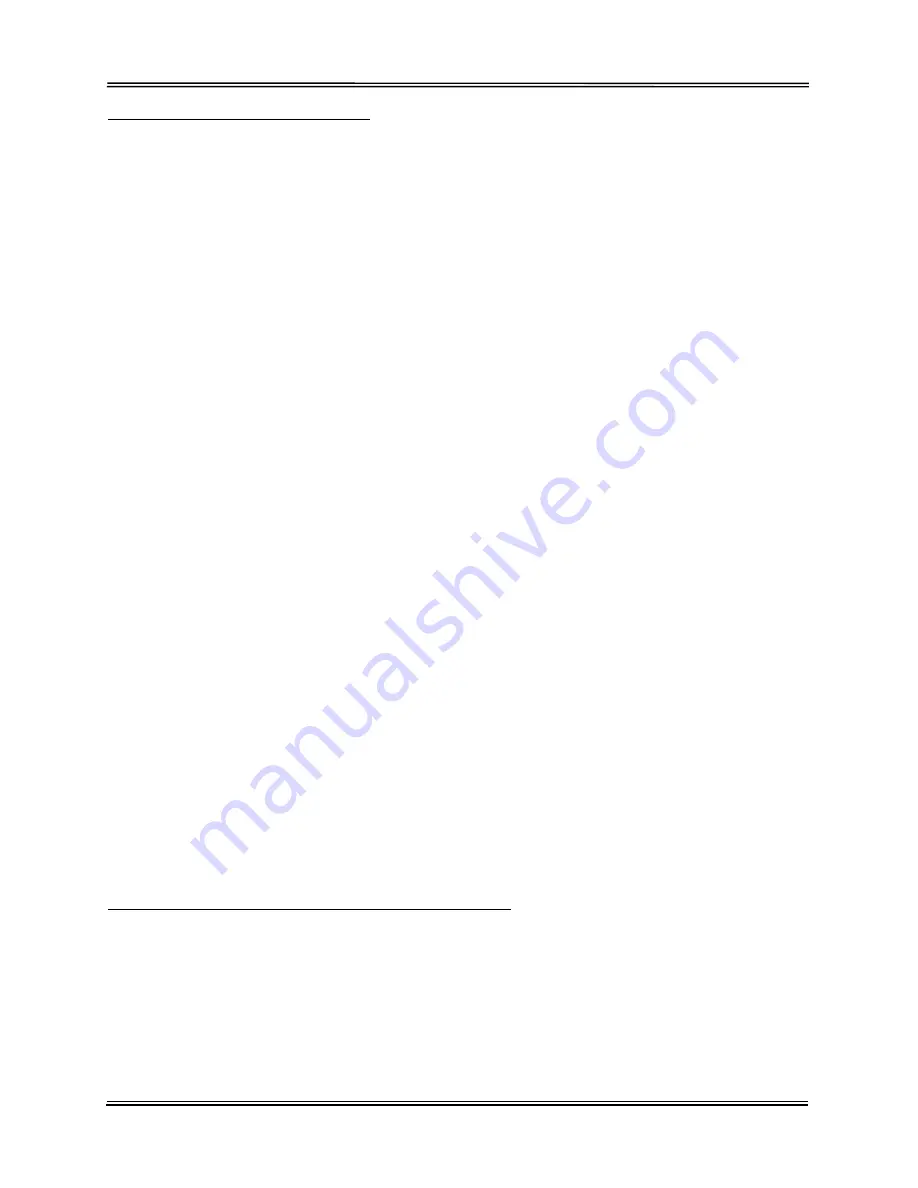
Mach-DSP User’s Manual
Document Number: MACH-DSP-9021
Page 47
www.ScannerMAX.com
Input Command parameters
In this section, you will find the parameters related to the input command signal.
Input Source
(analog or digital serial input)
This selects whether the Input Command signal is derived from the 6-pin Analog Input
connector, or the 8-pin header (with or without XY2-100 daughterboard) providing
serial-digital command input, using either the XY2-100 protocol or FB4 protocol.
Input Scale
(mechanical degrees motion for maximum positive input)
This controls the amount of mechanical motion caused by the input command voltage
(or digital signal). For example, if this is set to 15.00, then an input command signal
having +10V DC (or a 16-bit signal having a value of 65535) will create +15.00
mechanical degrees of deflection (+30 optical degrees of motion). This also implies that
-10V (or a 16-bit signal having a value of 0) will create -15 mechanical degrees (-30
optical degrees) of deflection. Thus, 20V peak to peak (or the full scale digital signal
range) will create 30 mechanical degrees peak-to-peak (or 60 optical degrees peak to
peak) deflection. To invert the polarity of input versus motion, this can be set to a
negative number. For example, if this is set to -15.00, then an input command signal
having +10V DC (or a 16-bit signal having a value of 65535) will create -15.00
mechanical degrees of deflection. This control allows values up to 150.00, thus
providing increased sensitivity in the form of smaller input command signals that create
large optical deflection angles.
Input Offset
(mechanical degrees of offset added to the input)
This controls the mechanical degrees of offset that will be applied to the servo input.
Input Shear
(geometric image rotation)
This controls the amount of signal from the X-axis that is fed into the Y-axis (and vice-
versa). This is usually used to compensate for small misalignments in mirror mounting
or misalignments of the beam entering the X-Y mount. This can also be used to perform
geometric correction. (Although it’s not intuitive or obvious why, the servo algorithm
requires somewhat more processing time when shear on the
X-axis
is not zero.)
Non-integrating (Class 0) servo parameters
In this section, you will find the main three parameters used by many servos found on
the market – most especially PD servos.
Error-proportional (Servo) Gain
This controls the amount of position error signal that is fed into the summing node.
Some servo drivers call this “Servo Gain”, and others call this “Error-proportional gain”.