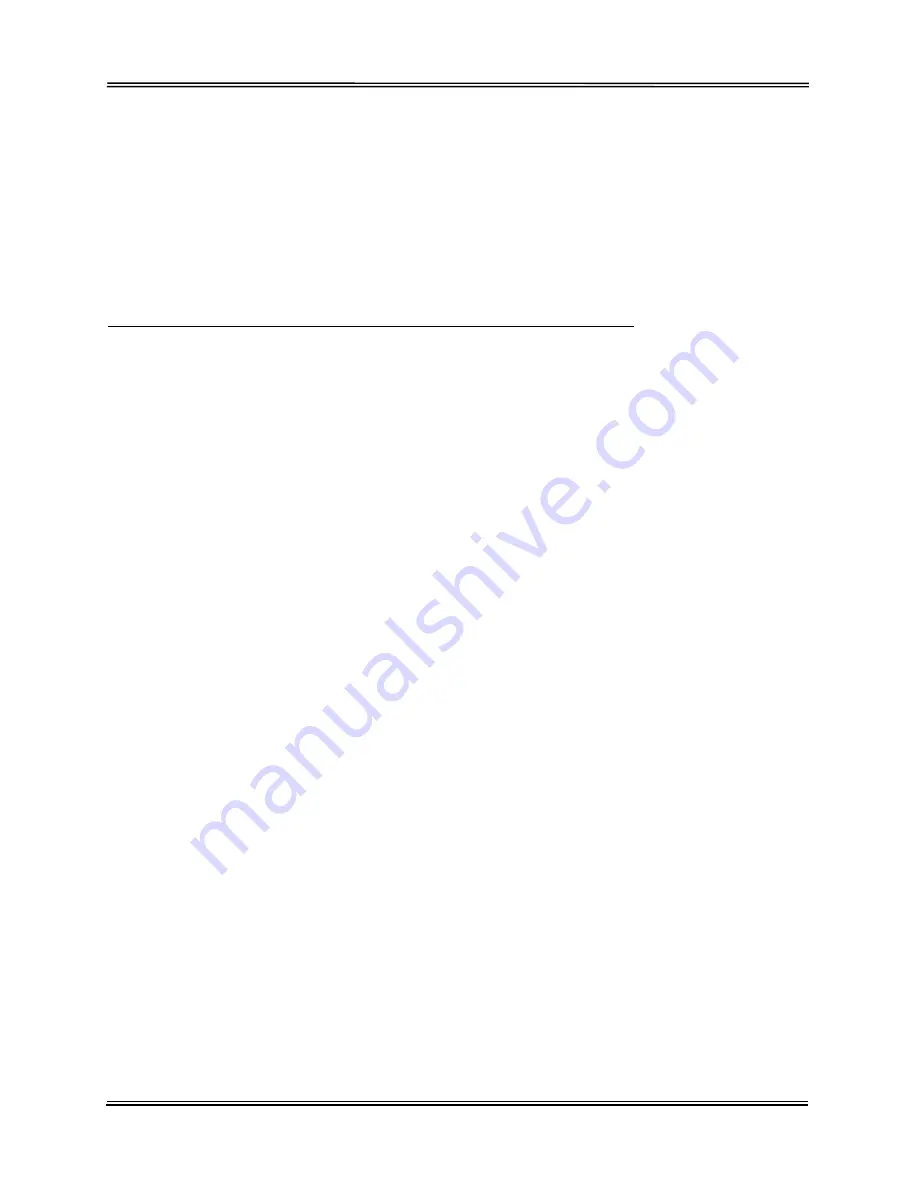
Mach-DSP User’s Manual
Document Number: MACH-DSP-9021
Page 56
www.ScannerMAX.com
Note that once a servo fault is triggered, the Mach-DSP servo will shut down, and then
go through a controlled startup sequence, which takes several seconds.
Also note that these controls are related to the internal position signal (viewable on the
built-in oscilloscope). A “positive” position signal may correspond to right-ward or left-
ward beam deflection, depending on the orientation of the X-Y mount and other factors.
It is this reason that these are referred to as “positive” and “negative” instead of
“clockwise”, “right-ward”, or some less-definitive quantity.
Velocity and Position (high frequency damping) observer
The Mach-DSP servo includes a flexible means of deriving high frequency velocity
information. Depending on the adjustment of the parameters in this section, simple
current integration could be used for high frequency damping, or alternatively, velocity
information may come from a “rigid body observer” built into the Mach-DSP servo. (For
more information about “observers”, see servo text books.)
Torque-constant to inertia ratio
In general, this controls the amount of current that is integrated to ultimately create the
high frequency velocity signal, which is then controlled using the “High Frequency
Damping gain” described above. Greater amounts of “Torque-constant to inertia ratio”
will allow lower amounts of High Frequency Damping gain.
When “Observer gain” is set to zero, this control only influences the amount of High
Frequency Damping gain that is needed. Stated another way, this works like a gain
control over the High Frequency Damping gain. However, when Observer gain is set
above zero, it is important that the Torque-constant to inertia ratio be set correctly,
otherwise the observer will not function correctly and velocity errors will result (making it
difficult or impossible to achieve perfect damping).
To correctly set this control, you should look for the “Torque constant” and “Rotor
Inertia” specifications found on the scanner’s datasheet. Add the mirror’s inertia to the
rotor inertia specified on the datasheet, and then perform a division.
For example, the Saturn 1 torque constant is 18,000, and its rotor inertia is 0.010. A
typical 3mm mirror’s inertia is 0.0027. Adding the 0.0027 mirror inertia to the 0.010 rotor
inertia sums to a total system inertia of 0.0127. Performing a division provides: 18,000 /
0.0127 = 1,417,322. This control does not allow numbers in the millions – only in the
thousands. Because of this, the optimal number to enter is 1417 (the actual torque
constant to inertia ratio of the system divided by 1000).
Viscous damping
Galvanometer scanners that use ball bearings will experience viscous damping, due
partially to the balls riding in the raceway, and due partially to the lubricant in the