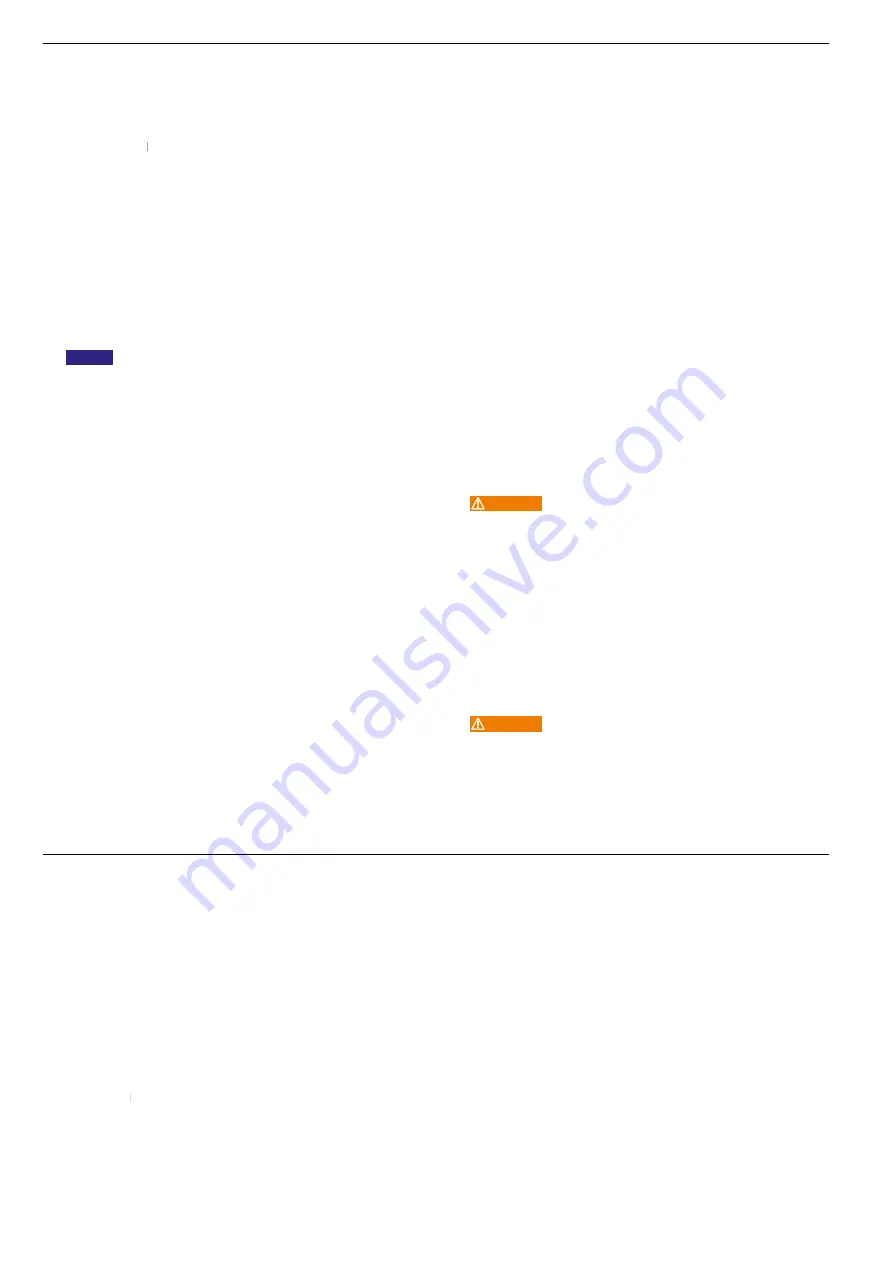
14
The pipe cutter (18) cuts pipes ¼ – 2", resp. 2½ – 4".
The reamer (19) deburs pipes ¼ – 2" resp. 2½ – 4". To avoid rotation, latch the
reamer sleeve into the reamer arm either in the front or in the back end,
depending on the position of the pipe.
3.2. Chuck
A clamping sleeve (Art. No. 343001) adapted to the diameter is required for
ROLLER’S Robot up to 2" for clamping diameters < 8 mm, for
ROLLER’S Robot
ROLLER’S Robot
ROLLER’S Robot
up to 4" for clamping diameters < 20 mm. The desired clamping diameter must
be specifi ed when ordering the clamping sleeve.
3.2.1. Quick Action Hammer Chuck (1), Guide Chuck (2)
The quick action hammer chuck (1) with large clamping ring and moving dies
inserted into the die carriers ensures centred and safe clamping with the least
force. As soon as the material protrudes from the guide chuck, this must be
closed.
To change the dies (24), close the clamping ring (22) up to approx. 30 mm
clamping diameter. Remove screws of the dies (24). Push out the dies to the
back with a suitable tool (screwdriver). Push the new dies with inserted screw
into the die carriers from the front.
3.3. Work Procedure
Remove blockages of chips and fragments of the workpiece before starting work.
NOTICE
NOTICE
Switch off the thread cutting machine when the tool set approaches the machine
housing.
Swing out the tools and move the tool carrier to the right-hand end position
with the aid of the pressing lever (8). Pass the material to be threaded through
the opened guide (2) and through the opened chuck (1) so that it extends by
about 10 cm from the chuck. Close the chuck until the jaw comes against the
material and then, after a short opening movement, jerk it shut once or twice
in order to clamp the material fi rmly. Closing the guide chuck (2) centers the
material that extends from the rear of the machine. Swing down and close the
die head. Set the switch (3) to position 1, then operate the foot switch (4). Type
U is switched on and off with the foot switch (4) only.
On Type K and Type D, the second operating speed can be selected for
sectioning, deburring and small thread cutting operations. To do this, with the
machine running, slowly move switch (3) from position 1 to position 2. With the
contact lever (8), advance the die head onto the rotating material.
After one or two threads have been cut, the die head will continue to cut auto-
matically. In the case of tapered pipe threads, the die head opens automatically
when the standard length of thread is reached. When cutting extended threads
or bolt threads, open the die head manually, with the machine running. Release
pedal switch (4). Open quick action hammer chuck, take out material.
Threads of unlimited length can be cut by reclamping the material, as follows.
When the tool holder approaches the machine housing during the thread cutting
process, release pedal switch (4) but do not open the die head. Release the
material and bring the tool holder and material to the right-hand end-position
by means of the contact lever. Clamp material again, switch on machine again.
For pipe cutting operations, swing in the pipe cutter (18) and bring it to the
desired cutting position by means of the contact lever. The pipe is cut by rotating
the spindle clockwise.
Remove any burrs inside the pipe resulting from the cutting operation with the
pipe reamer (19).
To drain the cooling lubricant: Take off the fl exible hose of the tool holder (7)
and hold it into a container. Keep the machine running until the oil tray is empty.
Or: Remove screw plug (25) and drain trough.
3.4. Cutting Nipples and Double Nipples
ROLLER’S Spannfi x (automatic inside clamping) or ROLLER’S Nipparo (inside
clamping) are used for cutting nipples. Make sure that the pipe ends are deburred
on the inside. Always push on the pipe sections as far as they will go.
To clamp the pipe section (with or without thread) with the ROLLER’S Nipparo,
the head of the nipple tightener is splayed by turning the spindle with a tool.
This may only be done with the pipe section fi tted.
Makes sure that no shorter nipples than the standard allows are cut with the
ROLLER’S Spannfi x and the ROLLER’S Nipparo.
3.5. Cutting Left-handed Threads
Only ROLLER’S Robot 2K, 2D, 3K, 3D, 4K and 4D are suitable for left-handed
threads. The die head in the tool carrier must be pinned with an M 10 × 40 screw
for cutting left-handed threads, otherwise this can lift and damage the start of
the thread. Set switch to position "R". Switch over the hose connections on the
coolant-lubricant pump or short circuit the coolant-lubricant pump. Alternatively,
use the changeover valve (Art. No. 342080) (accessory) which is fi xed to the
machine. The fl ow direction of the coolant-lubricant pump is reversed with the
lever on the changeover valve (Fig. 9).
4. Maintenance
Notwithstanding the maintenance described below, it is recommended to send
in the ROLLER thread cutting machine to an authorised ROLLER contract
customer service workshop for inspection and periodic testing of electrical
devices at least once a year. In Germany, such periodic testing of electrical
devices should be performed in accordance with DIN VDE 0701-0702 and also
prescribed for mobile electrical equipment according to the accident prevention
rules DGUV, regulation 3 “Electrical Systems and Equipment”. In addition, the
respective national safety provisions, rules and regulations valid for the appli-
cation site must be considered and observed.
4.1. Maintenance
WARNING
WARNING
Pull out the mains plug before carrying out maintenance or repair work!
The gear of the ROLLER’S thread cutting machine is maintenance-free. The
gear runs in a closed oil bath and therefore needs no lubrication. Keep the
clamping and guide chucks, guide arms, tool carrier, die head, ROLLER’S dies,
pipe cutter and pipe inside deburrer clean. Replace blunt ROLLER’S dies,
cutting wheel, deburrer blade. Empty and clean the oil tray from time to time
(at least once a year).
Clean plastic parts (e.g. housing) only with machine cleaner (Art. No. 140119)
or a mild soap and a damp cloth. Do not use household cleaners. These often
contain chemicals which can damage the plastic parts. Never use petrol,
turpentine, thinner or similar products for cleaning.
Make sure that liquids never get inside the ROLLER’S thread cutting machine.
4.2. Inspection/Repair
WARNING
WARNING
Pull out the mains plug before carrying out maintenance or repair work!
This work may only be performed by qualifi ed personnel.
The motor of ROLLER’S Robot has carbon brushes. These are subject to wear
and must therefore by checked and changed by qualifi ed specialists or an
authorised ROLLER customer service workshop from time to time.
eng eng
5. Behaviour in the event of faults
5.1. Fault: Machine does not start.
Cause:
Remedy:
● Emergency stop button not released.
● Release emergency stop button on foot switch.
● Thermal protection switch has tripped.
● Press thermal protection switch on foot switch.
● Worn carbon brushes.
● Have the carbon brushes changed by qualifi ed personnel or an authorised
ROLLER customer service workshop.
● Connecting lead and/or foot switch defective.
● Have the connecting lead and/or foot switch inspected/repaired by an
authorised ROLLER customer service workshop.
● Machine defective.
● Have the machine checked/repaired by an authorised ROLLER customer
service workshop.
5.2. Fault: Machine does not pull through
Cause:
Remedy:
● ROLLER’S dies are blunt.
ROLLER’S
ROLLER’S
● Change ROLLER’S dies.
● Unsuitable thread-cutting material.
● Use thread-cutting materials ROLLER’S Smaragdol or ROLLER’S Rubinol.
● Overloading of the electricity mains.
● Use a suitable power source.
● Too small a cross-section of the extension lead.
● Use cable cross-section of at least 2.5 mm².
● Poor contact at the connectors.
● Check connectors, use another outlet if necessary.
● Worn carbon brushes.
● Have the carbon brushes changed by qualifi ed personnel or an authorised
ROLLER customer service workshop.
● Machine defective.
● Have the machine checked/repaired by an authorised ROLLER customer
service workshop.