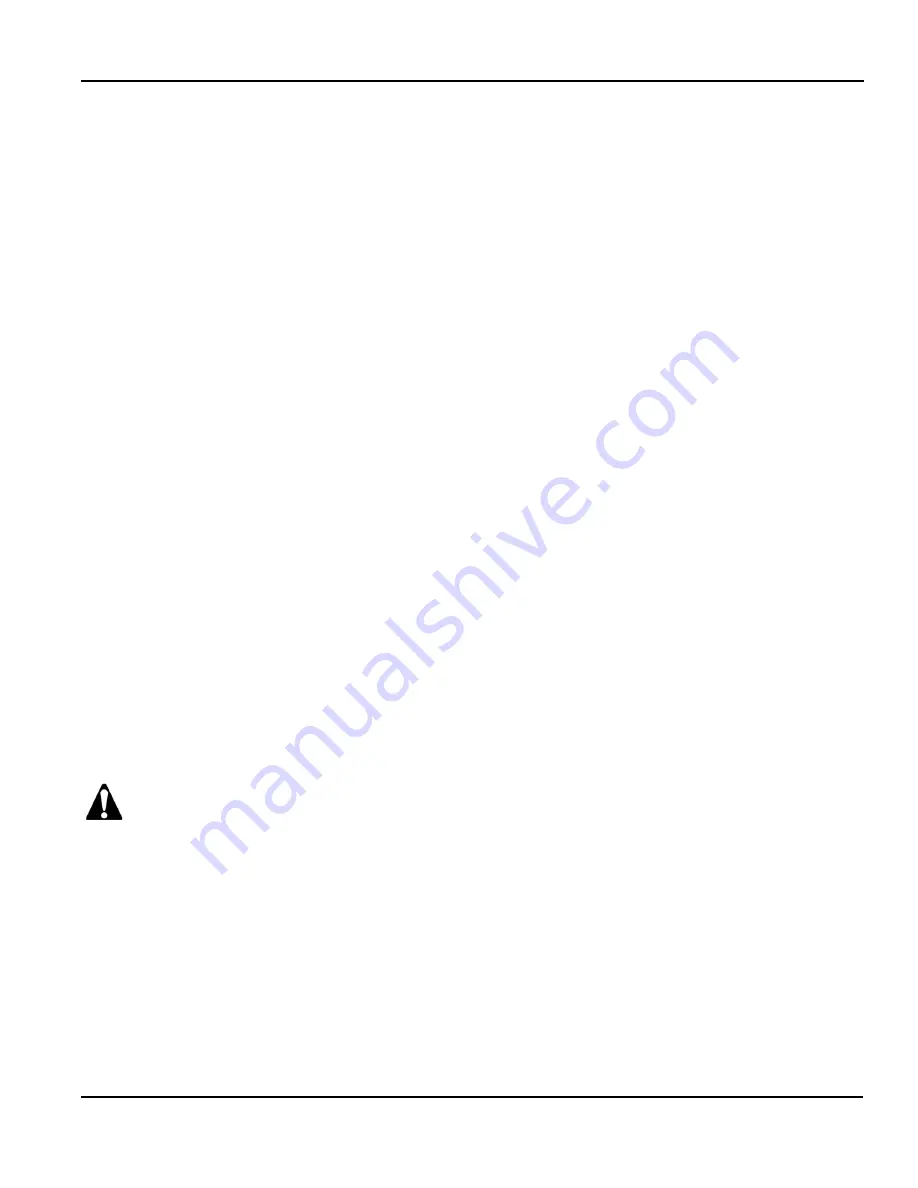
Rockford Systems, LLC
36
Call: 1-800-922-7533
SSC-1500 Part Revolution Solid-State Control
SECTION 3—INSTALLATION OF COMPONENTS
FLYWHEEL AND GEAR COVERS
According to OSHA 1910.219 and ANSI B15.1 for Mechanical Power-Transmission Apparatus, all rotating components including flywheels, gears,
sprockets and chains, sheaves and belts, shaft ends, etc., must be covered if at or below a seven-foot level from the floor or platform.
Note: ANSI
states it should be a nine-foot level.
Adequate cover material and brackets must be fabricated to retain these components in event of shaft or wheel
mounting failure.
COLLATERAL EQUIPMENT
All collateral press room and plant equipment such as spring or air slide counterbalances, die cushions, feeding equipment, and robots must be
safeguarded if they create hazards to personnel.
POINT-OF-OPERATION SAFEGUARDS
OSHA 1910.217 (c)(i) and (ii) require that:
“It shall be the responsibility of the employer (user) to provide and ensure the usage of point-of-operation guards or properly applied and adjusted
point-of-operation devices on every operation performed on a mechanical power press.”
Refer to Section 9, pages 77 - 78, for examples of point-of-operation safeguards for power presses.
Other Installation Considerations
PIPING
1.
An air lockout valve must be installed in the air line usually just before the filter-regulator-lubricator assembly to meet OSHA 1910.147 Lockout/
Tagout requirements. However, a separate lockout valve could be furnished for each air system on the machine such as counterbalance, die
cushion, clutch/brake, air cylinder, and blow-off.
2.
From the lockout valve, connect at the
In
threaded opening of the filter-regulator. Try to maintain an appropriate pipe size throughout for proper
air flow. Connect the piping to the ports using teflon tape on the male threads only. Do not allow tape to enter the interior of the filter-regulator-
lubricator, valve, or air cylinder. Before applying air pressure, make sure the filter and regulator bowls are at least hand tight.
3.
Most approved pipe or hose can be used on the press. Make sure the size is consistent throughout the system in order to avoid restriction. Keep
air runs as short as possible.
4.
See enclosed Filter-Regulator-Lubricator (FRL) Assembly Manual No. KSL-208 for additional details.
All air components require clean air. Blow all lines clean of water, dirt, scale, etc., before making final
connection. Drain water from filter bowl regularly. Should this bowl refill in a short period of time, it may indicate
the need for a larger filter in the main air supply line or an air line dryer system. The air filter must be kept clean
at all times. Never operate the machine unless the air filter is clean and water is drained.
WIRING
National Electrical Code practices, including NFPA 79, are usually followed for wiring the control system, especially color coding and the use of
numbered wire markers on
both ends of every wire
. Color coding is black for line voltage (208, 230, 460, or 575) and control at line voltage, red
for 120-V AC control circuits, blue for 24-V DC control circuits, white for current carrying ground (commonly referred to as the Neutral) and green
for any equipment grounding conductor. All terminal blocks in the control cabinet are color coded for easy identification.
a.
Install and wire the main disconnect switch (unless one already exists or is furnished in a custom control) using black wire. Follow wiring
instructions shown on the electrical schematics. Make certain this switch is capable of being locked in the off position only.
(Continued on next page.)