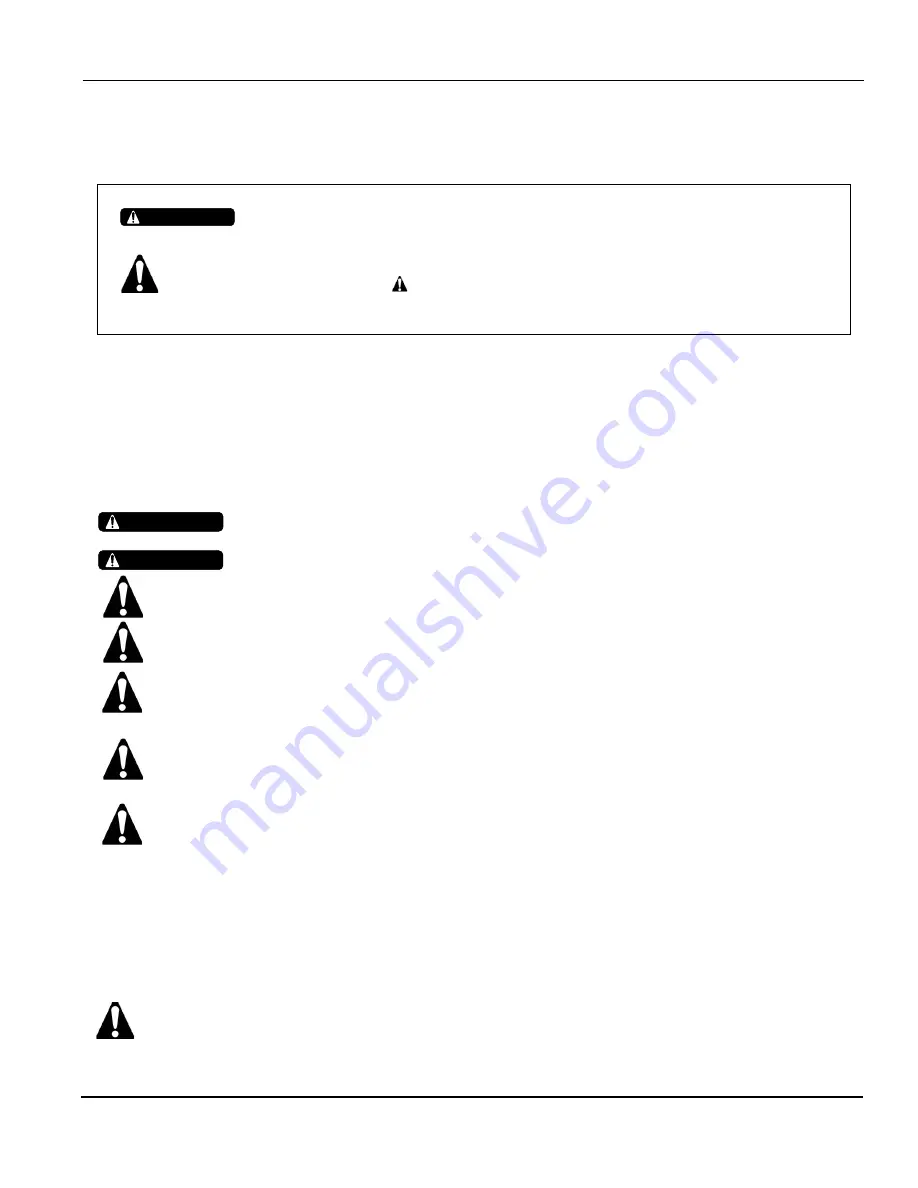
Rockford Systems, LLC.
Call: 1-800-922-7533
3
SSC-1500 Part Revolution Solid-State Control
SECTION 1—IN GENERAL
Efficient and safe machine operation depends on the development, implementation and enforcement of a safety program. This program requires,
among other things, the proper selection of point-of-operation guards and safety devices for each particular job or operation and a thorough safety
training program for all machine personnel. This program should include instruction on the proper operation of the machine, instruction on the
point-of-operation guards and safety devices on the machine, and a regularly scheduled inspection and maintenance program.
Rules and procedures covering each aspect of your safety program should be developed and published both in an operator’s safety manual, as
well as in prominent places throughout the plant and on each machine. Some rules or instructions which must be conveyed to your personnel
and incorporated in to your program include:
Danger is used to indicate the presence of a hazard which WILL cause SEVERE
personal injury if the warning is ignored.
THIS SAFETY ALERT SYMBOL IDENTIFIES IMPORTANT SAFETY MESSAGES IN THIS MANUAL.
WHEN YOU SEE THIS SYMBOL , BE ALERT TO THE POSSIBILITY OF PERSONAL INJURY, AND
CAREFULLY READ THE MESSAGE THAT FOLLOWS.
A company’s safety program must involve everyone in the company, from top management to operators, since only as a group can any
operational problems be identified and resolved. It is everyone’s responsibility to implement and communicate the information and material
contained in catalogs and instruction manuals to all persons involved in machine operation. If a language barrier or insufficient education would
prevent a person from reading and understanding various literature available, it should be translated, read or interpreted to the person, with
assurance that it is understood.
DANGER
“
”
“ ”
Safety Precautions
FOR MAINTENANCE AND INSPECTION ALWAYS REFER TO THE OEM’s (ORIGINAL EQUIPMENT
MANUFACTURER’S) MAINTENANCE MANUAL OR OWNER’S MANUAL. If you do not have an owner’s
manual, please contact the original equipment manufacturer.
(Continued on next page.)
Never
place your hands or any part of your body in this machine.
Never
operate this machine without proper eye, face and body protection.
Never
operate this machine unless you are fully trained, instructed, and have read the instruction manual.
Never
operate this machine if it is not working properly—stop operating and advise your supervisor immediately.
Never
use a foot switch to operate this machine unless a point-of-operation guard or device is provided and
properly maintained.
Never
operate this machine unless two-hand trip, two-hand control or presence sensing device is installed at
the proper safety distance. Consult your supervisor should you have any questions regarding the proper safety
distance.
Never
tamper with, rewire or bypass any control or component on this machine.
DANGER
DANGER