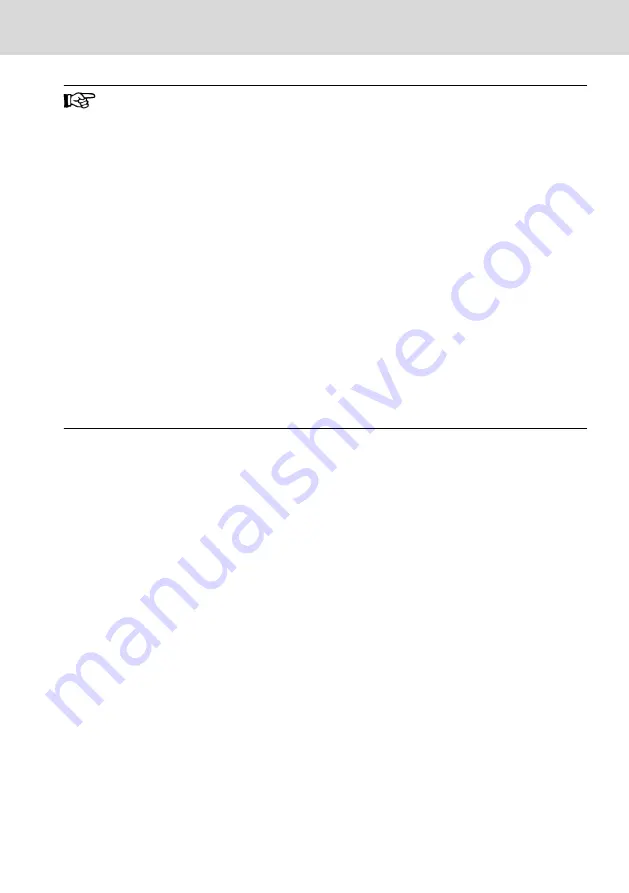
●
The failure rates of components used in the calculation process of
related safety parameters mentioned above are based on the Sie-
mens database: SIEMENS NORM SN_29500.
●
The PFH value is less than 2% of the total failure budget of a SIL3
safety loop.
●
"Mission Time" and "Proof Test Interval":
– The "Mission Time" of all components used must be observed
and complied with. After the "Mission Time" of a component
has elapsed, the component must be discarded or replaced. It
is not allowed to continue operating the component!
– After the component was discarded ("Mission Time" has
elapsed), it must be ensured that it cannot be reused (e.g., by
disabling it).
– There is no specified "Proof Test Interval" for the drive system.
Therefore, the "Mission Time" cannot be reset by a "Proof Test
Interval".
●
The safety function operates in High Demand Mode, where the
safety function is only performed on demand, in order to transfer
the EUC into a specified safe state, and where the frequency of
demands is greater than one per year.
EFC x610 Series
Bosch Rexroth AG
Appendix
DOK-RCON03-EFC-X610***-IT05-EN-P
387/389
Содержание EFC 3610 Series
Страница 18: ...Bosch Rexroth AG EFC x610 Series XVI DOK RCON03 EFC X610 IT05 EN P ...
Страница 332: ...Fig 15 15 0020 N 03_0025 N 03 Bosch Rexroth AG Accessories EFC x610 Series 300 389 DOK RCON03 EFC X610 IT05 EN P ...
Страница 333: ...Fig 15 16 0025 A 05 EFC x610 Series Bosch Rexroth AG Accessories DOK RCON03 EFC X610 IT05 EN P 301 389 ...
Страница 336: ...Fig 15 21 0250 N 05 Bosch Rexroth AG Accessories EFC x610 Series 304 389 DOK RCON03 EFC X610 IT05 EN P ...
Страница 421: ...Notes EFC x610 Series Bosch Rexroth AG ...