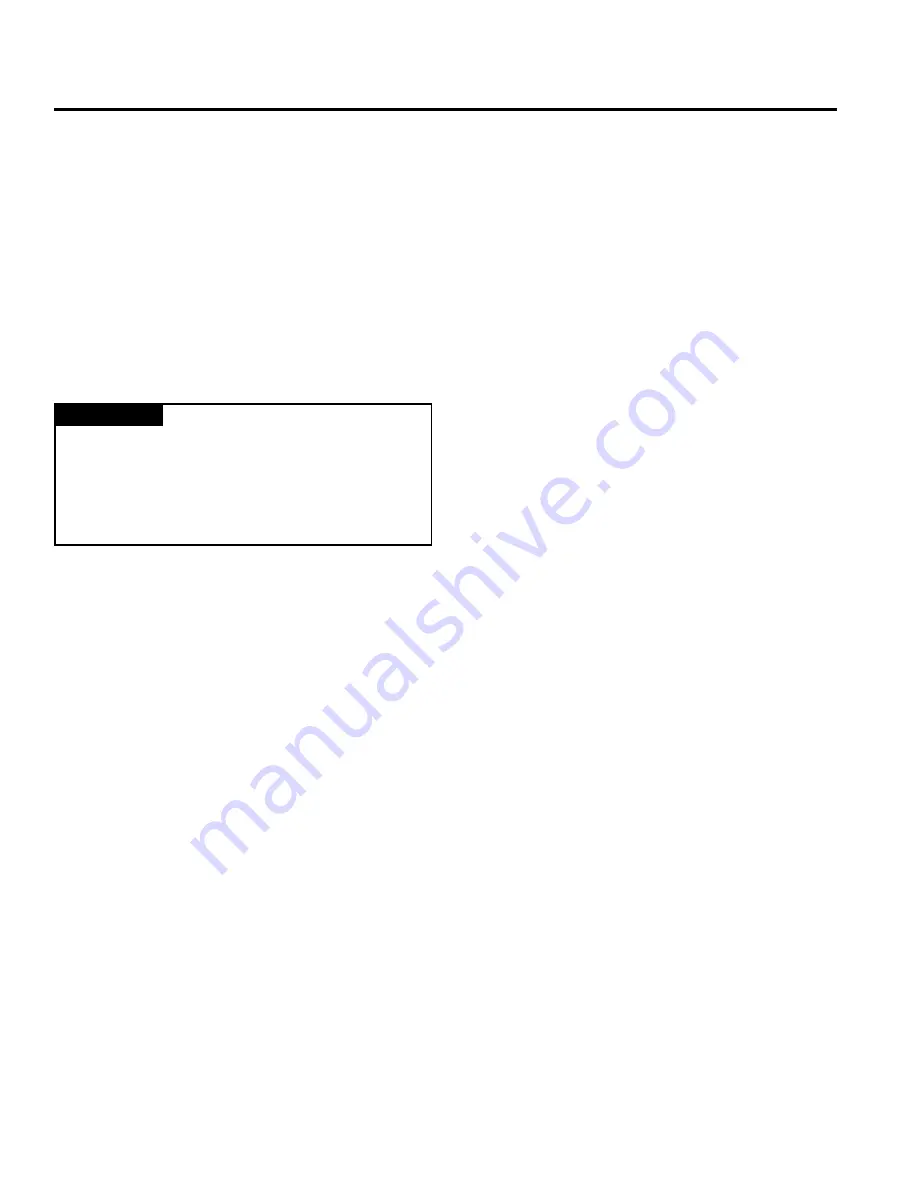
Publication PSS-UM001A-EN-P – December 2016
3-2
Use Auto Start Mode
Why Use Auto Start Mode?
Auto Start Mode offers you a quick and easy method of getting your
H Series Fieldbus I/O system ‘up and running’. If your H Series
Fieldbus I/O application can use default confi guration, you should
use Auto Start Mode to easily begin operations.
Once your adapter is:
• Installed
• Connected to the system’s I/O modules
• Online (in RSNetWorx for DeviceNet)
you only need to choose the Auto Start Mode option in the adapter’s
Parameters
window in the RSNetWorx for DeviceNet software and
the adapter begins working with a default confi guration.
IMPORTANT
Although Auto Start Mode allows your adapter to operate with a
default confi guration, you can write a custom confi guration after
operation has begun.
For more information on how to write custom confi guration for
your adapter on DeviceNet, see Chapter 5, Add the H Series
Fieldbus DeviceNet Adapter to the DeviceNet Scanner’s
Scanlist.
What Does Auto Start Mode Do?
When using Auto Start Mode, the adapter:
1.
Sets all modules on the backplane to Auto Baud
2.
Reads the Subnet module’s identity information
3.
Sets backplane modules’ addresses sequentially
4.
Generates a scanlist for the Subnet
5.
Maps I/O data, based on byte, word, double-word, or
fi xed boundaries
When this sequence of events is completed, the H Series Fieldbus
I/O modules connected to the adapter are ready to accept
connections from a scanner.
How Is I/O Data Mapped Using Auto Start
Mode?
In Auto Start Mode, you can map I/O data in the adapter’s memory
in one of the following ways:
• Byte Boundaries
• Word Boundaries
• Double
Word Boundaries
• Fixed Boundaries
Byte Boundaries
Each node’s I/O data is mapped in the adapter’s memory at the next
available byte. This option works best in applications that use Allen-
Bradley PLCs and SLCs.
Word Boundaries
Each node’s I/O data is mapped in the adapter’s memory at the next
available word. This option works best in applications that use Allen-
Bradley PLCs and SLCs.
Double Word Boundaries
Each node’s I/O data is mapped in the adapter’s memory at the next
available double word. This option works best in applications that
use Allen-Bradley Logix products.
Fixed Boundaries
The map to the fi xed location is based on the node address. Mapping
size ranges from 1 to 32 and is set using an EDS parameter. The
mapping for a node with address 1 begins on byte 2. The formula for
mapping is: 2+((N-1)(mapsize)), where N = node address.
Keep the following in mind when using fi xed boundaries:
• You specify fi xed map size using EDS parameters
• Data is mapped after status/channel words in I/O image,
beginning with byte 2
• No data area is reserved for MACID 0 (the adapter)
Requirement To Using Auto Start Mode
Your H Series Fieldbus DeviceNet adapter must be free of I/O
connections on DeviceNet when you use Auto Start Mode. If you
attempt to use Auto Start Mode after another scanner device has
established I/O connections with the adapter, your attempt to use
Auto Start Mode will be rejected. When the adapter is confi guring
itself in Auto Start Mode, no other device can establish I/O
connections to the adapter.
Содержание H Series
Страница 135: ...DeviceNet Media Design and Installation Guide...
Страница 144: ...Publication DNET UM072C EN P July 2004 Table of Contents iv...
Страница 170: ...Publication DNET UM072C EN P July 2004 1 26 Get Started Notes...
Страница 194: ...Publication DNET UM072C EN P July 2004 2 24 Identify Cable System Components Notes...
Страница 212: ...Publication DNET UM072C EN P July 2004 3 18 Make Cable Connections Notes...
Страница 238: ...Publication DNET UM072C EN P July 2004 4 26 Determine Power Requirements Notes...
Страница 248: ...Publication DNET UM072C EN P July 2004 5 10 Correct and Prevent Network Problems Notes...
Страница 250: ...Publication DNET UM072C EN P July 2004 A 2 Understand Select NEC Topics Notes...
Страница 263: ......
Страница 267: ...Isysnet Serial Bus System Selection Guide Pneumatic...
Страница 287: ...H Series Fieldbus DeviceNet Adapters PSSCDM12A PSSCDM18PA User Manual...