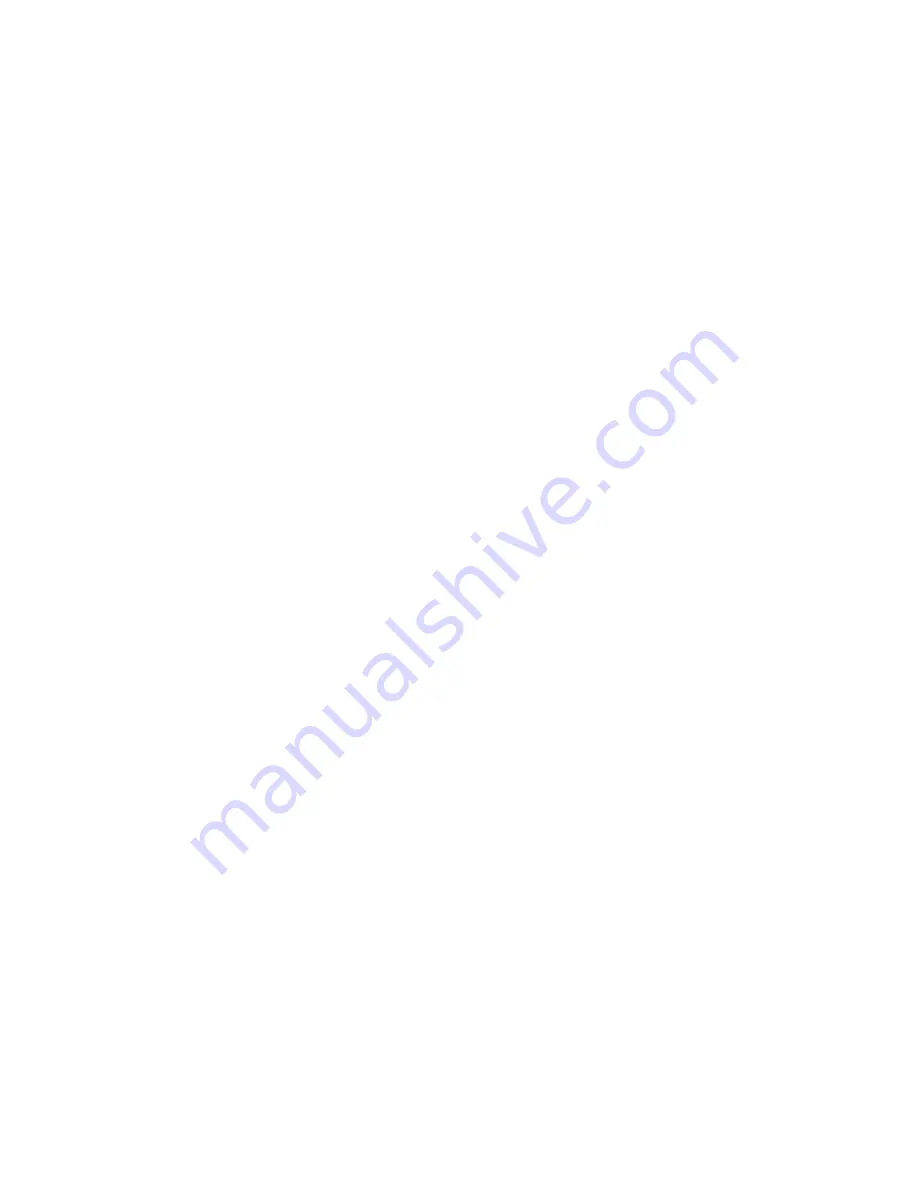
Industrial Automation Wiring and Grounding Guidelines
E115P
12
Isolation Transformer —
For applications near excessive
electrical noise generators, an isolation transformer (for
the second transformer) provides further suppression of
electromagnetic interference from other equipment. The
output actuators being controlled should draw power from
the same AC source as the isolation transformer, but not
from the secondary of the isolation transformer (Figure 9).
Constant-Voltage Transformer —
In applications where
the AC power source is especially “soft” and subject to
unusual variations, a constant-voltage transformer can
stabilize the AC power source to the processor and
minimize shutdowns. The constant-voltage transformer
must be of the harmonic neutralizing type.
If the power supply receives its AC power through a
constant-voltage transformer, the input sensors connected
to the I/O chassis should also receive their AC power
from the same constant-voltage transformer. If the inputs
receive their AC power through another transformer, the
AC source voltage could go low enough that erroneous
input data enters memory while the constant-voltage
transformer prevents the power supply from shutting down
the processor. The output actuators being controlled
should draw power form the same AC sources as the
constant-voltage transformer, but not from the secondary
of the constant-voltage transformer (9).
Ground Connection
When AC power is supplied as a separately derived
system through an isolation/step-down transformer, you
can connect it as a grounded AC system or an ungrounded
AC system. For a grounded AC system, connect one
side of the transformer secondary to the ground bus as in
Figure 7. For an ungrounded AC system, connect one
side of each test switch for the ground-fault-detector lights
to the ground bus as in Figure 8. We do not recommend
an ungrounded system. Follow local codes in determining
whether to use a grounded system.
When bringing AC power into the enclosure, do not ground
its raceway to the ground bus on the back-panel.
Connecting the raceway to the ground bus may cause the
processor to fault by introducing EMI into the grounding
circuit. Local codes may provide an exception for
permitting isolation from the raceway. For example, article
250-75 of the National Electrical Code has an exception
that explains the conditions under which this isolation
from the raceway is permitted.
Surge-Suppression
Transient EMI can be generated whenever inductive loads
such as relays, solenoids, motor starters, or motors are
operated by “hard contacts” such as pushbutton or selector
switches. The wiring guidelines are based on the
assumption that you guard your system against the effects
of transient EMI by using surge-suppressors to suppress
transient EMI at its source. Inductive loads switched by
solid-state output devices alone do not require surge-
suppression. However, inductive loads of AC output
modules that are in series or parallel with hard contacts
require surge-suppression to protect the module output
circuits as well as to suppress transient EMI.
Figure 10 shows 3 Examples of where to use suppressors.
In Example 1, although the motor-starter coil is an inductive
load, it does not need a suppressor because it is switched
by a solid-state device alone. In Example 2, the relay coil
needs a suppressor because a hard-contact switch is in
series with the solid-state switch. However, in both
Examples 1 and 2, we show a suppressor on the motor
and solenoid because it is an inductive load switched by
the hard contacts of the motor starter or relay.
Even if
they have no interaction with the control system,
regularly cycled loads of this type need suppression
if conductors connecting to these loads are: 1)
connected to the same separately derived system as
that of the control system; 2) or routed in proximity
with conductors of the control system as per the
routing guidelines.
In Example 3, the pilot light has a built-in step-down
transformer that needs a suppressor because it is an
inductive load being switched by the hard contacts of a
contact output module; without suppression, the transient
EMI would be generated inside the I/O chassis. Lights
with built-in step-down transformers that are switched by
hard contacts external to any I/O chassis may not need to
be suppressed because the noise spike they can generate
may be only approximately one tenth that of a relay or
motor starter.
In all cases, the AC power coming into the I/O modules
must be switched by the CRM contacts. Therefore, a
suppressor is needed across the line at the load side of
the CRM contacts as shown in Figures 7 and 8. The
application (voltage, net load of I/O circuits) dictates the
specific suppressor needed across the line at the load
side of the CRM contacts.
Содержание H Series
Страница 135: ...DeviceNet Media Design and Installation Guide...
Страница 144: ...Publication DNET UM072C EN P July 2004 Table of Contents iv...
Страница 170: ...Publication DNET UM072C EN P July 2004 1 26 Get Started Notes...
Страница 194: ...Publication DNET UM072C EN P July 2004 2 24 Identify Cable System Components Notes...
Страница 212: ...Publication DNET UM072C EN P July 2004 3 18 Make Cable Connections Notes...
Страница 238: ...Publication DNET UM072C EN P July 2004 4 26 Determine Power Requirements Notes...
Страница 248: ...Publication DNET UM072C EN P July 2004 5 10 Correct and Prevent Network Problems Notes...
Страница 250: ...Publication DNET UM072C EN P July 2004 A 2 Understand Select NEC Topics Notes...
Страница 263: ......
Страница 267: ...Isysnet Serial Bus System Selection Guide Pneumatic...
Страница 287: ...H Series Fieldbus DeviceNet Adapters PSSCDM12A PSSCDM18PA User Manual...