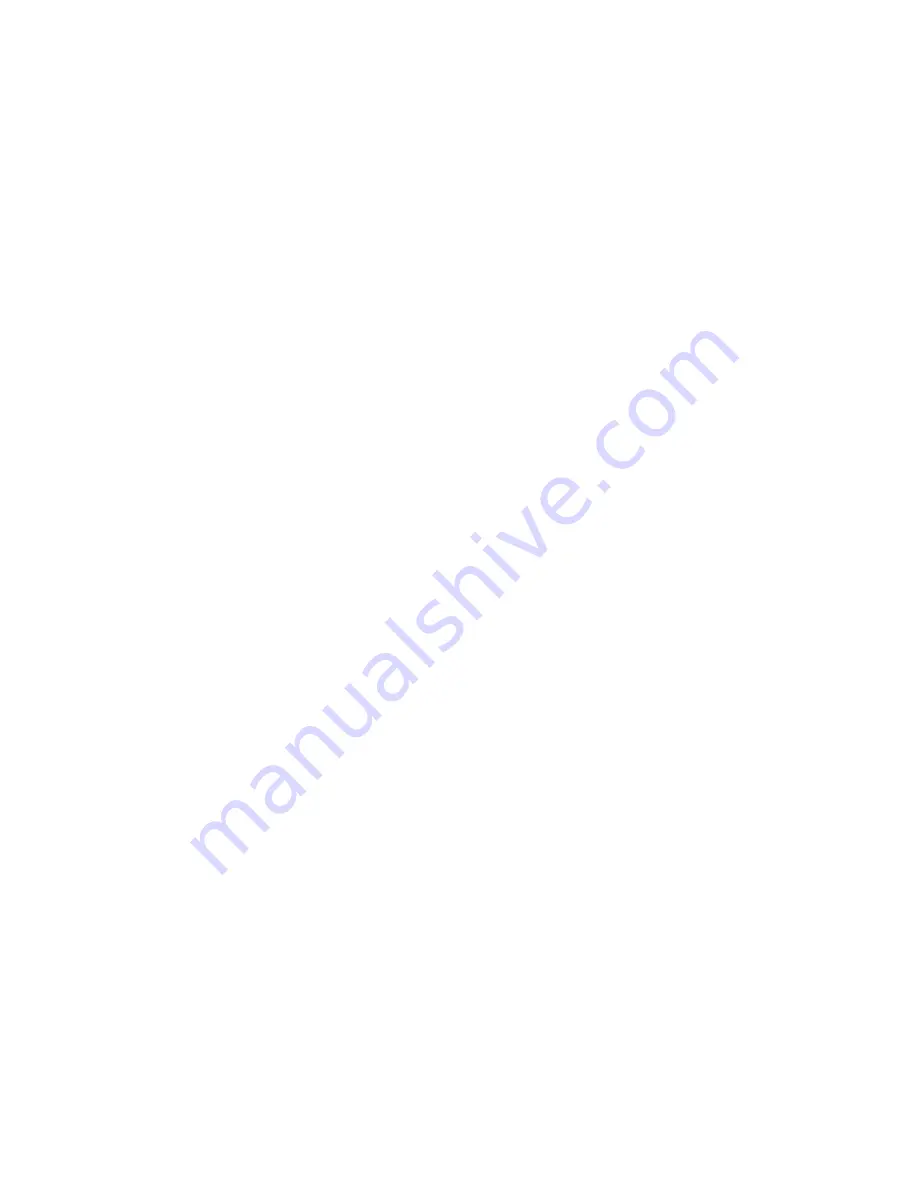
Manual Version e1-4.3.0.ae-R3.
Page
76
5.4.6
Standby Configuration Menu
The standby parameters options screen is displayed on next page. Each of the options is briefly
explained.
Process Purge High
Allows for the user to set the nitrogen pressure in the process chamber for purging the system during
the load/unload cycle.
Process Purge Low
Allows for the user to set the pressure that the process chamber is pumped down to when purging the
system during the load/unload cycle.
Process Standby
Allows the user to set the process chamber base pressure for the pump-down process.
Exp Purge High
Allows for the user to set the nitrogen pressure in the expansion chamber for purging the system during
the load/unload cycle.
Exp Purge Low
Allows for the user to set the pressure that expansion chamber is pumped down to when purging the
system during the load/unload cycle.
Exp Standby
Allows the user to set the base pressure in the expansion chamber for the pump-down process.
ATM Pressure
Allows the user to define the set point for the atmospheric pressure light to come on during the venting
process.
V9 Low Pressure Point
Allows user to define the pressure at which Valve 9 opens.
Load Purge Cycles
Allows user to set the number of purge cycles for during the load cycle.
Unload Purge Cycles
Allows user to set the number of purge cycles for during the unload cycle.
Load Sample Timeout
Allows the user to set the amount of time for which the nitrogen vent gas continues to when the
chamber is at atmospheric pressure.
Содержание SPTS Xactix e1 Series
Страница 1: ...Manual Version e1 4 3 0 ae R3 2015 04 Xactix e1 Series System Manual ...
Страница 38: ...Manual Version e1 4 3 0 ae R3 Page 36 Figure 23 Shroud ventillation connection Shroud ventilation connection ...
Страница 40: ...Manual Version e1 4 3 0 ae R3 Page 38 Figure 26 Showerhead stop installed ...
Страница 48: ...Manual Version e1 4 3 0 ae R3 Page 46 Figure 29 Chamber ventilation shroud moved to back ...
Страница 49: ...Manual Version e1 4 3 0 ae R3 Page 47 Figure 30 Chamber ventilation shroud pulled forward ...
Страница 83: ...Manual Version e1 4 3 0 ae R3 Page 81 ...
Страница 86: ...Manual Version e1 4 3 0 ae R3 Page 84 ...
Страница 101: ...Manual Version e1 4 3 0 ae R3 Page 99 Figure 46 Gax box heater ...
Страница 103: ...Manual Version e1 4 3 0 ae R3 Page 101 Figure 48 Vacuum interlock switches Chamber vacuum switch Main vacuum switch ...
Страница 109: ...Manual Version e1 4 3 0 ae R3 Page 107 9 Set number of purge cycles to 0 and Hard Pump Time to 10 minutes ...