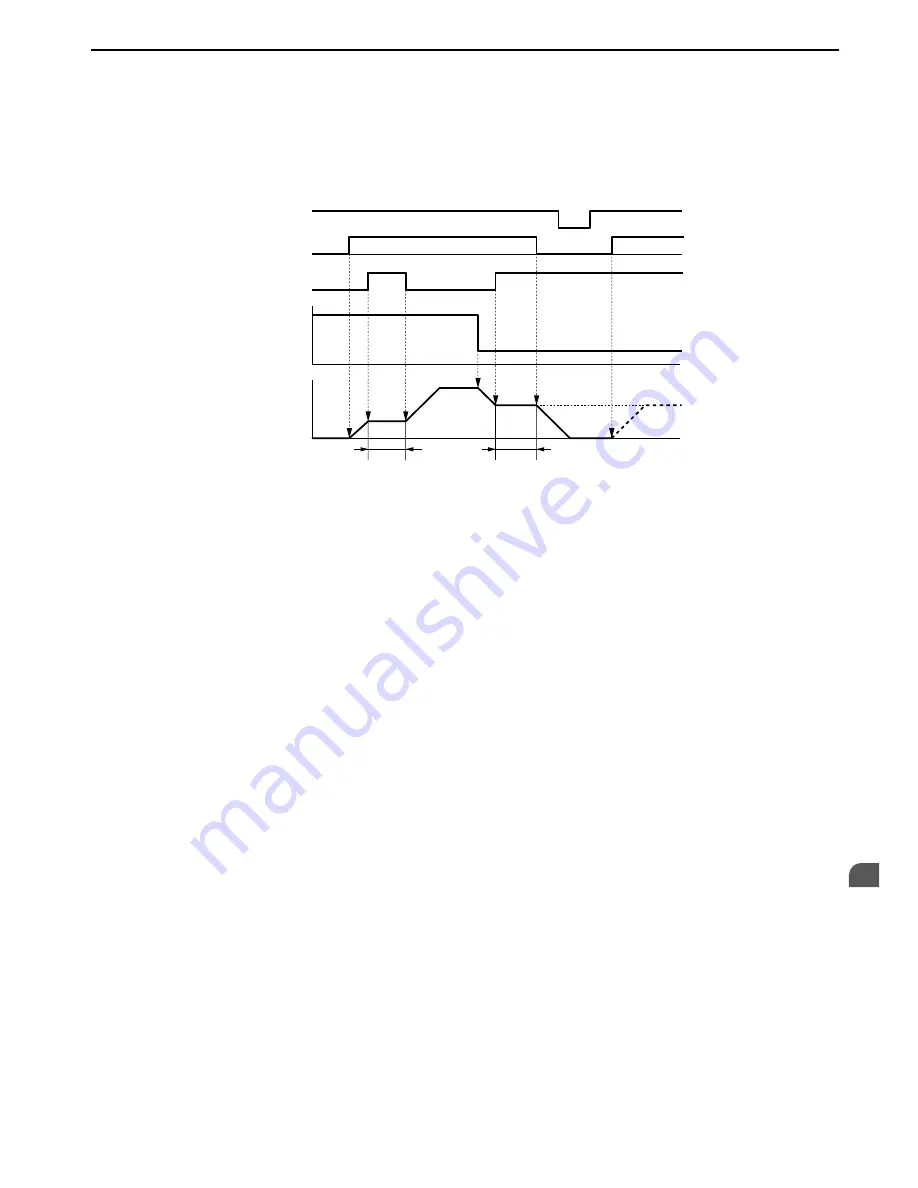
The frequency reference value will be reset to 0 Hz when the Run command is canceled or the drive power is switched
off. The drive will start from 0 Hz when restarted.
Setting 1: Enabled
• Acceleration Hold
The last hold value will be saved when the Run command or the drive power is switched off. The drive will use the value
that was saved as the frequency reference when it restarts. The accel/decel hold input must be enabled the entire time or
else the hold value will be cleared.
Power supply
Forward Run / Stop
Hold Accel/Decel
Frequency reference
Output frequency
d4-01 = 1
d4-01 = 0
Hold
Hold
OFF
OFF
OFF
OFF
OFF
ON
ON
ON
ON
ON
ON
Figure 5.12 Frequency Reference Hold with Accel/Decel Hold Function
• Up/Down
The frequency reference value will be saved when the Run command or the drive power is switched off. The drive will
use the frequency reference that was saved when it restarts.
Clearing the Value that was Saved
Depending on which function is used, the frequency reference value that was saved can be cleared by:
• Releasing the acceleration hold input.
• Setting an Up or Down command while no Run command is active.
5.4 d: Reference Settings
SIEP C710606 33A OYMC AC Drive – J1000 User Manual
85
5
Parameter Details
Содержание JZA
Страница 2: ......
Страница 24: ...1 3 Component Names This Page Intentionally Blank 22 SIEP C710606 33A OYMC AC Drive J1000 User Manual...
Страница 52: ...3 12 Wiring Checklist This Page Intentionally Blank 50 SIEP C710606 33A OYMC AC Drive J1000 User Manual...
Страница 70: ...4 9 Test Run Checklist This Page Intentionally Blank 68 SIEP C710606 33A OYMC AC Drive J1000 User Manual...
Страница 162: ...8 5 Communication Options This Page Intentionally Blank 160 SIEP C710606 33A OYMC AC Drive J1000 User Manual...
Страница 210: ...C 13 Self Diagnostics This Page Intentionally Blank 208 SIEP C710606 33A OYMC AC Drive J1000 User Manual...
Страница 230: ...Index This Page Intentionally Blank 228 SIEP C710606 33A OYMC AC Drive J1000 User Manual...
Страница 231: ...This Page Intentionally Blank SIEP C710606 33A OYMC AC Drive J1000 User Manual 229...