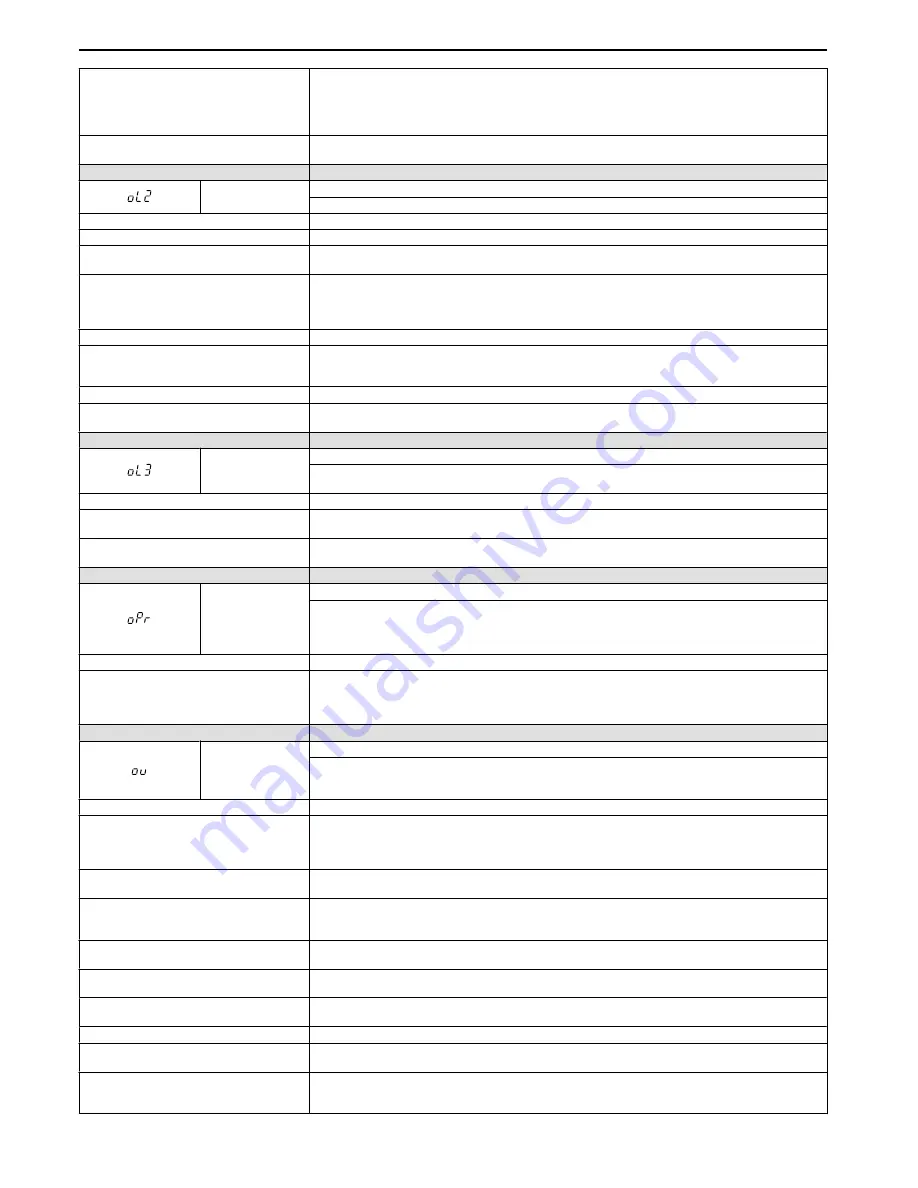
Motor overheated by overexcitation
operation.
• Overexcitation increases the motor losses and thereby the motor temperature. If applied too long,
motor damage can occur. Prevent excessive overexcitation operation or apply proper cooling to the
motor.
• Reduce the excitation deceleration gain (n3-13).
• Set L3-04 (Stall Prevention during Deceleration) to a value other than 4.
Output current fluctuation due to input phase
loss
Check the power supply for phase loss.
LED Operator Display
Fault Name
oL2
Drive Overload
The thermal sensor of the drive triggered overload protection.
Cause
Possible Solution
Load is too heavy.
Reduce the load.
Cycle times are too short during acceleration
and deceleration.
Increase the settings for the acceleration and deceleration times (C1-01 through C1-04).
Voltage is too high for the V/f characteristics.
• Adjust the preset V/f pattern (E1-04 through E1-10). This will mainly involve reducing E1-08 and
E1-10.
• Be careful not to lower E1-08 and E1-10 excessively because this reduces load tolerance at low
speeds.
Drive capacity is too small.
Replace the drive with a larger model.
Overload occurred when operating at low
speeds.
• Reduce the load when operating at low speeds.
• Replace the drive with a model that is one frame size larger.
• Lower the carrier frequency (C6-02).
Excessive torque compensation.
Reduce the torque compensation gain (C4-01) until there is no speed loss but less current.
Output current fluctuation due to input phase
loss
Check the power supply for phase loss.
LED Operator Display
Fault Name
oL3
Overtorque Detection 1
The current has exceeded the value set for torque detection (L6-02) for longer than the allowable time
(L6-03).
Cause
Possible Solution
Parameter settings are not appropriate for the
type of load.
Check the settings of parameters L6-02 and L6-03.
There is a fault on the machine side (e.g., the
machine is locked up).
Check the status of the load. Remove the cause of the fault.
LED Operator Display
Fault Name
oPr
External Digital Operator Connection Fault
The external operator has been disconnected from the drive.
Note:
An oPr fault will occur when both of the following conditions are true:
• Output is interrupted when the operator is disconnected (o2-06 = 1)
• The run command is assigned to the operator (b1-02 = 0 and LOCAL has been selected)
Cause
Possible Solution
External operator is not properly connected to
the drive.
• Check the connection between the operator and the drive
• Replace the cable if damaged
• Turn off the drive input power and disconnect the operator. Next reconnect the operator and turn the
drive input power back on.
LED Operator Display
Fault Name
ov
Overvoltage
Voltage in the DC bus has exceeded the overvoltage detection level.
• For 200 V class: approximately 410 V
• For 400 V class: approximately 820 V (740 V when E1-01 is less than 400)
Cause
Possible Solution
Deceleration time is too short and
regenerative energy flows from the motor
into the drive.
• Increase the deceleration time (C1-02, -04).
• Install a braking resistor or a dynamic braking resistor unit.
• Enable stall prevention during deceleration (L3-04 = “1”).
Stall prevention is enabled as the default setting.
Excessive braking load.
The braking torque was too high, causing regenerative energy to charge the DC bus.
Reduce the braking torque, use a braking option, or lengthen decel time.
Surge voltage entering from the drive input
power.
Install a DC reactor.
Note:
Voltage surge can result from thyristor convertor and phase advancing capacitor using same
drive main input power supply.
Ground fault in the output circuit causing the
DC bus capacitor to overcharge.
• Check the motor wiring for ground faults.
• Correct grounding shorts and turn the power back on.
Excessive regeneration when overshoot
occurs after acceleration.
• Lengthen the S-curve at acceleration end.
Drive input power voltage is too high.
• Check the voltage.
• Lower drive input power voltage within the limits listed in the specifications.
The dynamic braking transistor is damaged. Replace the drive.
The braking transistor is wired incorrectly.
• Check braking transistor wiring for errors.
• Properly rewire the braking resistor device.
Drive fails to operate properly due to noise
interference.
• Review the list of possible solutions provided for controlling noise.
• Review the section on handling noise interference and check the control circuit lines, main circuit
lines and ground wiring.
6.4 Fault Detection
126
SIEP C710606 33A OYMC AC Drive – J1000 User Manual
Содержание JZA
Страница 2: ......
Страница 24: ...1 3 Component Names This Page Intentionally Blank 22 SIEP C710606 33A OYMC AC Drive J1000 User Manual...
Страница 52: ...3 12 Wiring Checklist This Page Intentionally Blank 50 SIEP C710606 33A OYMC AC Drive J1000 User Manual...
Страница 70: ...4 9 Test Run Checklist This Page Intentionally Blank 68 SIEP C710606 33A OYMC AC Drive J1000 User Manual...
Страница 162: ...8 5 Communication Options This Page Intentionally Blank 160 SIEP C710606 33A OYMC AC Drive J1000 User Manual...
Страница 210: ...C 13 Self Diagnostics This Page Intentionally Blank 208 SIEP C710606 33A OYMC AC Drive J1000 User Manual...
Страница 230: ...Index This Page Intentionally Blank 228 SIEP C710606 33A OYMC AC Drive J1000 User Manual...
Страница 231: ...This Page Intentionally Blank SIEP C710606 33A OYMC AC Drive J1000 User Manual 229...