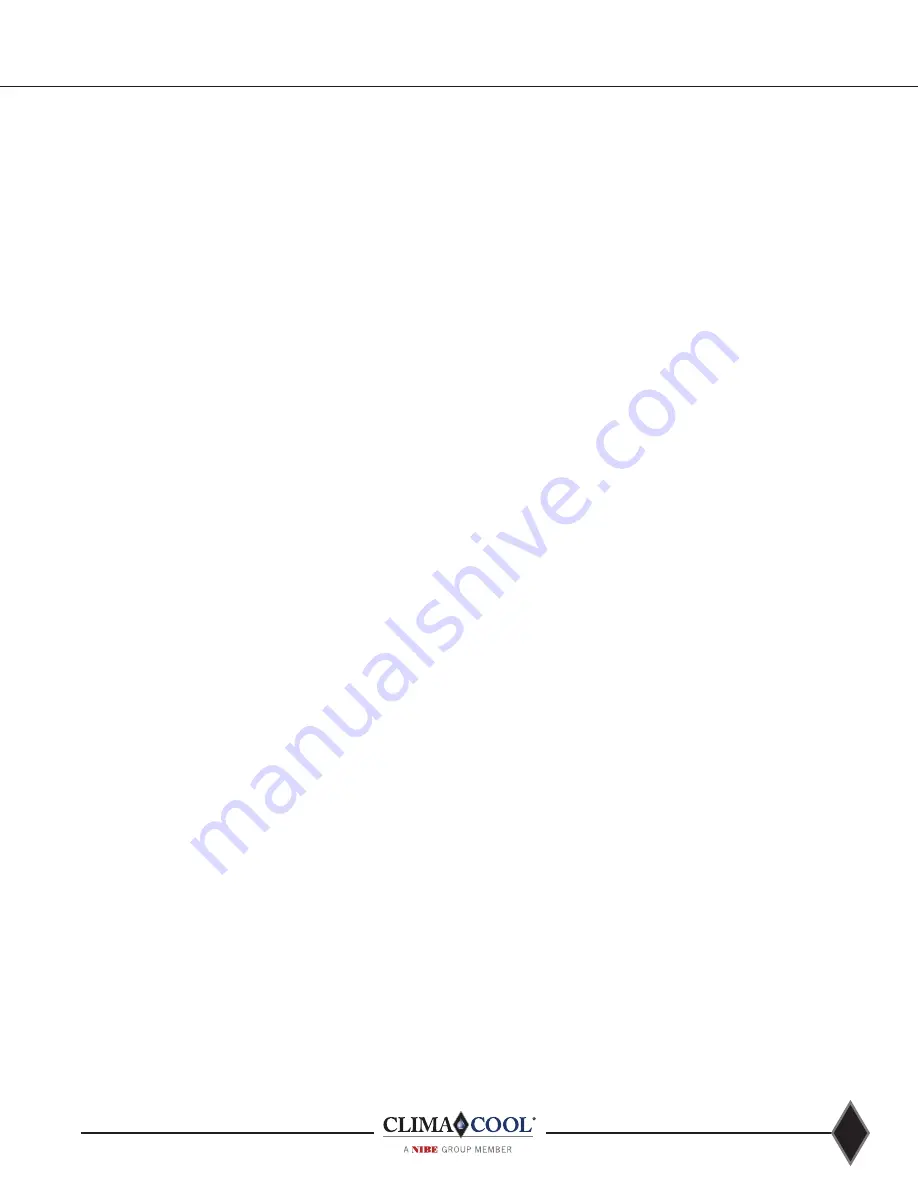
59
www.climacoolcorp.com
Copper Tubing, Brazing and System
Reprocessing Recommendations
Copper tubing must be refrigeration grade (ACR type
“L”). Be sure to install appropriate copper fittings rated
for ACR applications . Never leave refrigerant lines open
when they are not directly being installed . Never rely on
the last refrigerant connection joint at a specific section
(UCR module or condenser section) to provide structural
support for the interconnecting piping . Line pulsation may
occur at start-up and shut down of scroll compressors .
Additional line support may be required to prevent vibration
transmission or movement in the line . Ensure that all
interconnecting piping is properly and independently braced
at 7 feet minimum intervals, and within 2 feet from each
section’s final connection location, to prevent joint fracture
due to line vibrations or liquid hammering .
Use 15% silver-phosphorus braze filler rod when brazing
copper-to-copper joints . When brazing copper-to-brass
joints, apply “sta-silv” brazing paste (or equivalent)
sparingly to the joint areas, and use 45% silver-phosphorus
braze filler rod. Always purge a generous flow of dry
nitrogen (approximately 10 CFH) through the lines while
brazing to prevent internal scaling of copper oxide on
heated copper surfaces exposed to air .
When sizing the interconnecting refrigerant lines, never
use the stub-out sizes at the UCR module section as the
determining factor . For proper operation, all discharge
and liquid lines must be sized in accordance with the
recommendations provided in the following piping sections .
After installing the interconnecting piping, proper system
evacuation and reprocessing guidelines are provided in
the Refrigeration System Reprocessing section of the Split
System Interconnecting Piping on page 60 .
Liquid Line Piping Recommendations
All liquid lines should be kept as short as possible, and the
line sizing is determined to provide for a low-pressure drop
to prevent liquid line flashing. There should always be a
gradual negative elevation change when traversing from
the remote condenser location to the UCR module section .
Avoid any reversing elevation changes throughout this liquid
line run . Horizontal liquid lines should be sloped downward
in the direction of refrigerant flow at a pitch of 1/8” per foot.
The total equivalent distance between the condenser and
the UCR section (including allowances for U-bends and 90°
elbows) should not exceed 100 feet . Avoid routing liquid lines
through heated spaces which may result in undesirable flash
gas generated at the TXV inlet . Avoid insulating liquid lines .
Conforming to local and national codes is the responsibility
of the service technician or installing contractor . The service
technician should be familiar with the following codes:
•
ASHRAE Standard Safety Code for Mechanical
Refrigeration, ANSI/ASHRAE 15-1978
•
American National Standard Code for Pressure Piping,
ANSI B31 .5-1974
Factory Tested
ClimaCool modular chillers have been pressure-tested,
evacuated and both refrigeration circuits pressurized
with 50 psig of dry nitrogen prior to shipment . The split
system chillers require interconnecting refrigeration piping
between the ClimaCool UCR modular remote air cooled
chiller and the remote condenser section . The condenser
section provided by ClimaCool is typically a remote air-
cooled condenser configuration. Contact the factory for
guidelines for customer supplied, field integration to other
permissible condenser types, such as evaporative condenser
configurations. The refrigerant charge will be weighed-
in in the field based on the condenser configuration and
condenser model . The ClimaCool UCR030 model is equipped
with a 72 pound liquid receiver capacity per compressor
circuit . The UCR050 and UCR070 models have an 84 pound
liquid receiver installed per circuit . All ClimaCool UCR models
MUST be charged with R-410A refrigerant . Field installation
of additional receiver capacity may be required depending
on the refrigerant retaining volume of the remote
condenser and interconnecting piping . After the total
refrigerant amount is charged into each circuit (weighed
in using an appropriate refrigeration scale), the resulting
weight should be recorded on the UCR module data plate
for future reference . See Refrigerant Charging Procedure
on pages 61 - 62 for specific charging guidelines. Also
refer to the job specific submittal data for the appropriate
refrigerant charge amount .
UCR Modular Chiller Refrigeration
Piping Connections
The discharge and liquid line stub-out connections at the
UCR module section are equipped with shut-off valves with
capped leads . Never uncap these leads without checking
the shutoff valves to be sure that they are fully closed and
the units are ready for piping . All scroll compressors in
ClimaCool UCR modules are equipped with POE refrigeration
oil . Systems with compressors using POE oils must be kept
closed at all times except when the interconnecting piping is
being directly installed . POE oils are extremely hygroscopic
in nature and will absorb an undesirable amount of moisture
from normal ambient air within a few minutes .
Refrigeration System Re-Processing
Содержание CLIMACOOL UCR 30
Страница 19: ...17 www climacoolcorp com Voltage Phase Monitor Wiring Diagram...
Страница 29: ...27 www climacoolcorp com Evaporator Water Pressure Drop Charts...
Страница 30: ...28 www climacoolcorp com Glycol Performance Adjustments Factor Charts...
Страница 41: ...39 www climacoolcorp com Condenser Layout for RC1 007A H24 and RC1 008A H24 1 Row 2 Fan 1140RPM...
Страница 42: ...40 www climacoolcorp com Condenser Layout for RC2 019A 026A and 31A H48 and RC2 038A H44 2 Row 4 Fan 1140RPM...
Страница 43: ...41 www climacoolcorp com Condenser Layout for RC2 018A X48 RC2 026A X40 and RC2 032A X44 2 Row 4 Fan 830 RPM...
Страница 47: ...45 www climacoolcorp com 45 www climacoolcorp com Condenser Layout for RC2 048A Q82 2 Row 8 Fan 540RPM...
Страница 78: ...76 www climacoolcorp com Wiring Diagram...
Страница 79: ...77 www climacoolcorp com Wiring Diagram...
Страница 80: ...78 www climacoolcorp com Wiring Diagram CoolLogic Control Panel...
Страница 81: ...79 www climacoolcorp com Wiring Diagram CoolLogic Control Panel...