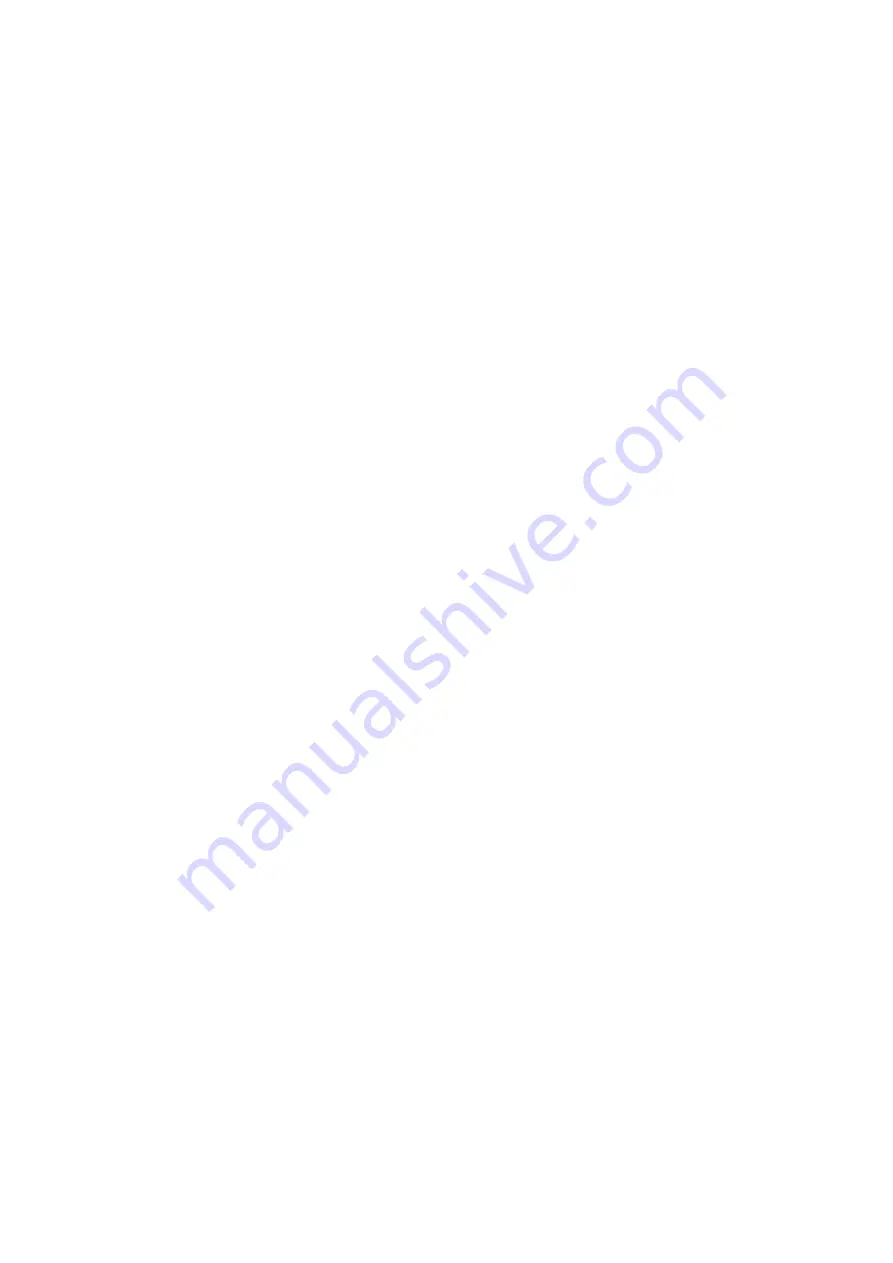
76
Chapter XI Common Equipment Faults
and Troubleshooting Methods
1. Shake during machine operation
Reason and solution: the level of the machine is not adjusted properly. Use a level meter to adjust
the level of the machine and tighten the screws fixing the foot cup.
The steps for adjusting the machine level are as follows:
①
Suspend the four legs of the machine
②
Adjust the level of the left and right of the machine
③
Adjust the level of the back and forth of the machine (only one foot in front should be
adjusted. An area can be fixed with 3 points), put down the suspended foot cup of
the machine and tighten the screws for fixing the foot cup.
2. Electric shock when touching the machine
Reason and solution:
The ground wire of the machine has poor contact or is not grounded, and induced electricity
with a certain voltage will be released through the servo driver during the operation of the
machine.
This problem can be solved by grounding protection. The specific method is to lead a wire
from the rear cover screw of the machine and connect it to the dedicated ground wire of the
workshop. (Note: do not confuse or misconnect electrostatic wires with ground wires)
3. The machine makes the sound of "beeping" for a long time.
Reason and solution:
Computer hardware failure. Check whether the memory module is firmly inserted and
reinsert it after pulling it out. Or, the computer maintenance personnel check for other faults.
4. The system prompts that X axis or Y axis cannot be moved when running the program
Reason 1: poor interface contact of motion control card.
Solution: close the program, pull out the interface of the motion control line, check whether
there is any blockage or deflection at the interface, and reconnect after eliminating the
problem.
Reason 2: poor contact at X or Y filter or falling off.
Solution: close the power supply and open the machine casing to confirm whether there is
any poor contact.
Reason 3: loose wiring of the motion control card.