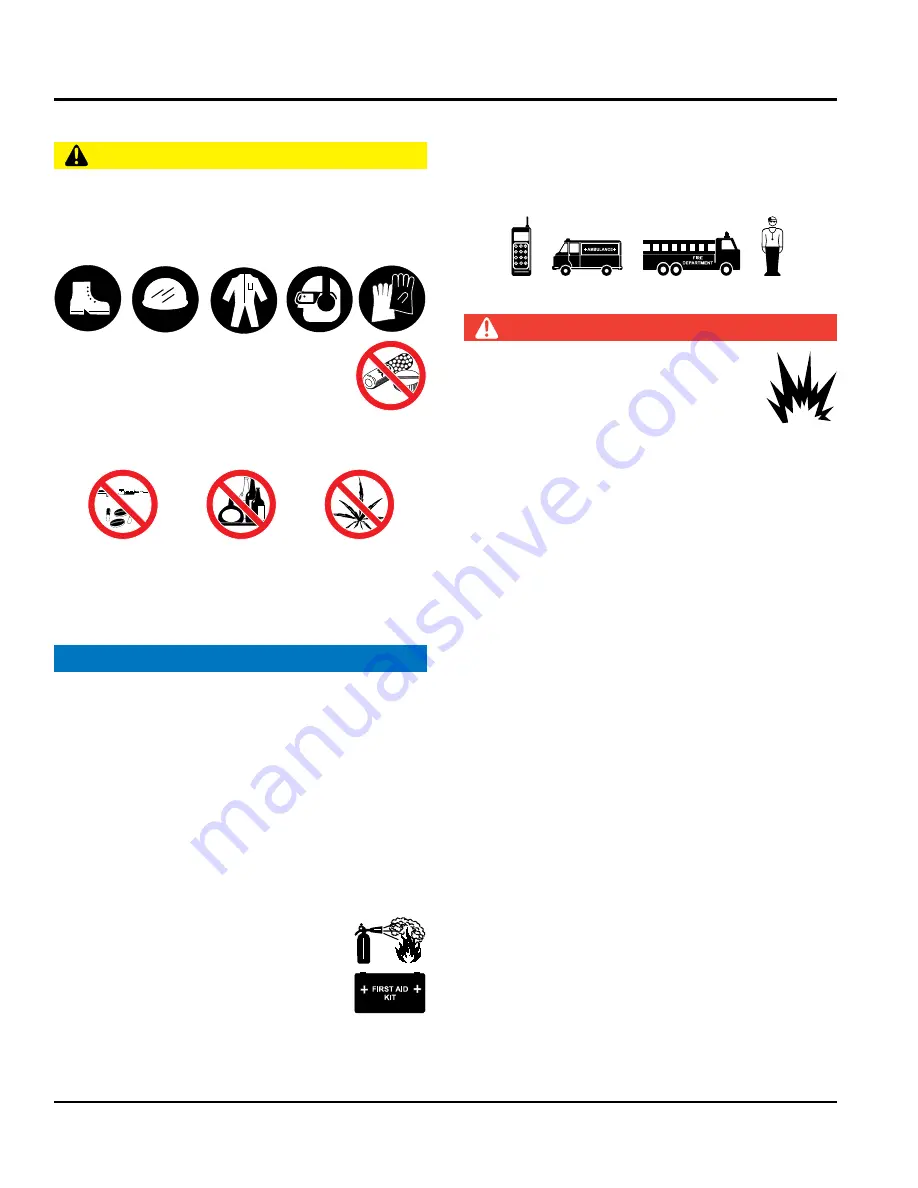
PAGE 8 — DIS185SSI4F AIR COMPRESSOR • OPERATION MANUAL — REV. #0 (12/19/16)
SAFETY INFORMATION
GENERAL SAFETY
CAUTION
NEVER
operate this equipment without proper protective
clothing, shatterproof glasses, respiratory protection,
hearing protection, steel-toed boots and other protective
devices required by the job or city and state regulations.
NEVER
operate this equipment when not
feeling well due to fatigue, illness or when
under medication.
NEVER
operate this equipment under the infl uence of
drugs or alcohol.
ALWAYS
check the equipment for loosened threads or
bolts before starting.
DO NOT
use the equipment for any purpose other than
its intended purposes or applications.
NOTICE
This equipment should only be operated by trained and
qualifi ed personnel 18 years of age and older.
Whenever necessary, replace nameplate, operation and
safety decals when they become diffi cult read.
Manufacturer does not assume responsibility for any
accident due to equipment modifi cations. Unauthorized
equipment modifi cation will void all warranties.
NEVER
use accessories or attachments that are not
recommended by MQ Power for this equipment. Damage
to the equipment and/or injury to user may result.
ALWAYS
know the location of the nearest
fi re extinguisher.
ALWAYS
know the location of the nearest
fi rst aid kit.
ALWAYS
know the location of the nearest phone or
keep
a phone on the job site.
Also, know the phone numbers
of the nearest
ambulance, doctor
and
fi re department.
This information will be invaluable in the case of an
emergency.
AIR COMPRESSOR SAFETY
DANGER
NEVER
operate the equipment in an explosive
atmosphere or near combustible materials. An
explosion or fi re could result causing severe
bodily harm or even death.
Keep the towing vehicle or equipment carrier, compressor
hoses, tools, and all personnel at least 10 feet (3 m) from
power lines and buried cables.
DO NOT
use air from this air compressor for respiration
(breathing).
Stay clear of the compressor during electrical storms! It
can attract lightning.
DO NOT
engage in horseplay with air hoses as death
or serious injury may result.
NEVER
use air compressor for respirator equipment
by which compressed air is supplied for human
consumption. The compressed air contains carbon
monoxide and other contaminants. Such air may cause
serious injury or death if used by a person for respiration.
This compressor is not designed for air pressurized
construction methods and underwater diving jobs.
NEVER
use compressed air for human consumption
such as pressurizing diving air tanks. Consumption of
compressed air can cause death while diving.