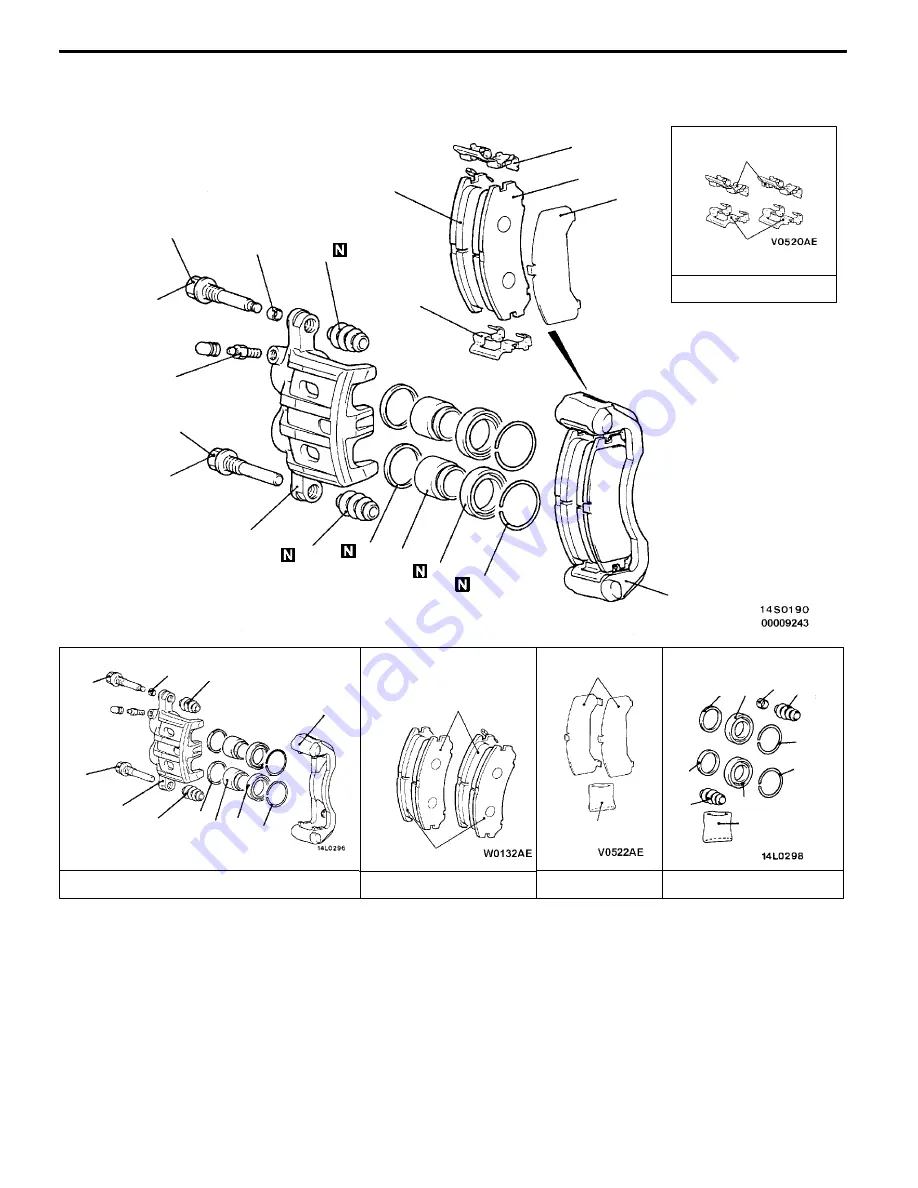
BASIC BRAKE SYSTEM -
Disc Brake
35A-22
DISASSEMBLY AND REASSEMBLY
35100820044
10
11
12
13
14
1
2
3
4
5
6
7
8
9
74 Nm
8 Nm
74 Nm
Brake caliper kit
Pad set
Seal and boots kit
14
5
2
3
5
1
10
5
9
8 7 6
4
13
12
9
3 5
5
7
6
Grease
<FRONT>
Clip set
14
14
Shim set
6
7
9
Grease
11
Disassembly steps
"
A
A
1. Guide pin
"
A
A
2. Lock pin
3. Bushing
4. Caliper support (pad, clip, shim)
5. Pin boot
6. Boot ring
A
A
"
7. Piston boot
A
A
"
8. Piston
A
B
"
9. Piston seal
10. Caliper body
11. Pad and wear indicator assembly
12. Pad assembly
13. Outer shim
14. Clip
Содержание Space Runner 1998
Страница 35: ...ENGINE 4G6 11A ENGINE 4G9 11B 11A 1 ENGINE CONTENTS 11109000276...
Страница 74: ...NOTES...
Страница 119: ...13A 1 FUEL CONTENTS GASOLINE DIRECT INJECTION GDI 4G6 13A GASOLINE DIRECT INJECTION GDI 4G9 13B FUEL SUPPLY 13C...
Страница 354: ...NOTES...
Страница 355: ...13C 1 FUEL SUPPLY CONTENTS 13509000197 GENERAL INFORMATION 2 FUEL TANK 3...
Страница 418: ...NOTES...
Страница 436: ...NOTES...
Страница 460: ...NOTES...
Страница 519: ...AUTOMATIC TRANSMISSION On vehicle Service 23 59 OIL SEAL LAYOUTsub 04 O A H B C D E F G I J K L M N...
Страница 532: ...NOTES...
Страница 567: ...REAR AXLE 2WD 27A REAR AXLE 4WD 27B 27A 1 REAR AXLE CONTENTS 27109000246...
Страница 660: ...NOTES...
Страница 714: ...NOTES...
Страница 722: ...NOTES...
Страница 732: ...NOTES...
Страница 772: ...NOTES...
Страница 912: ...NOTES...
Страница 913: ...INTERIOR 52A SUPPLEMENTAL RESTRAINT SYSTEM SRS 52B 52A 1 INTERIOR AND SUPPLEMENTAL RESTRAINT SYSTEM SRS CONTENTS...
Страница 954: ...NOTES...