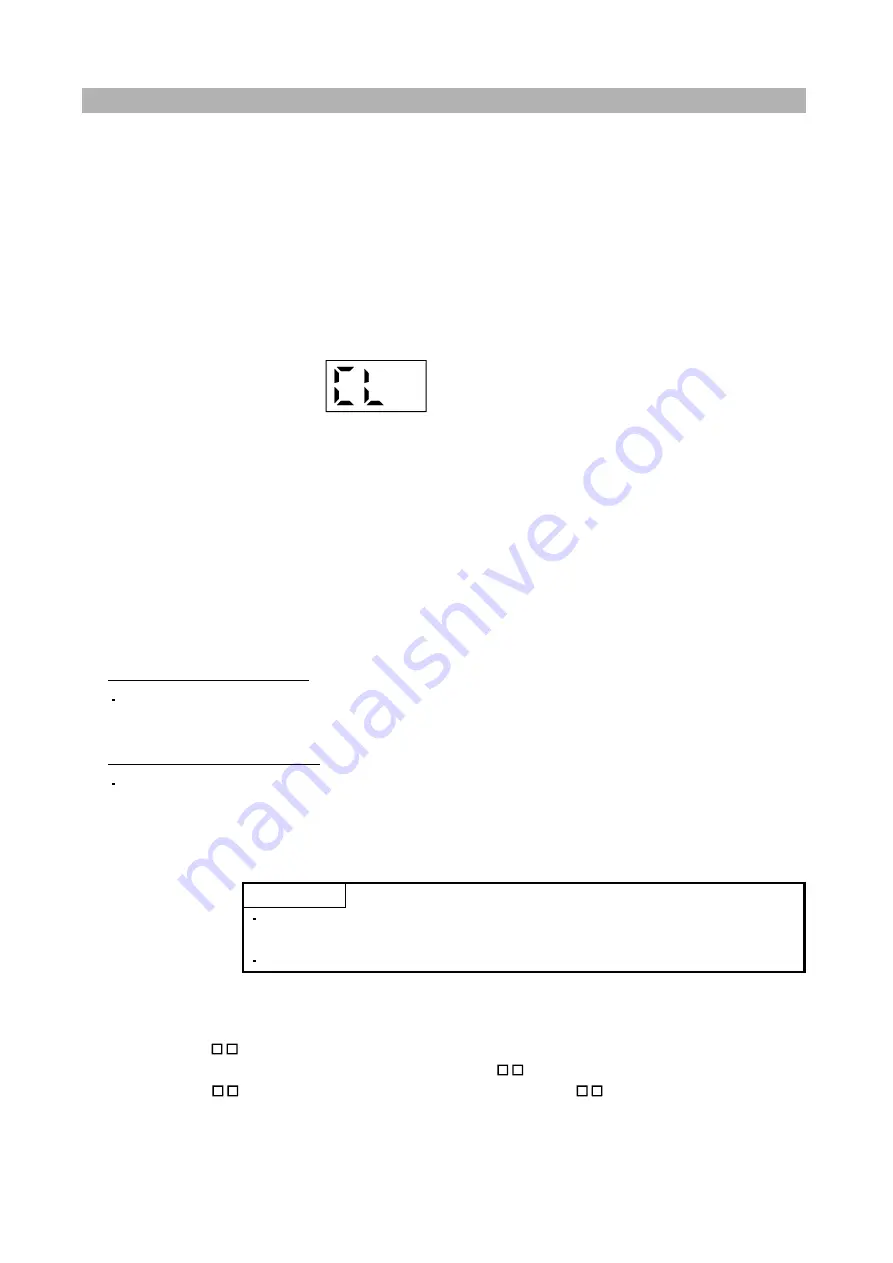
- 5 -
Introduction
(2) Power on and off procedures
(a) Power-on
Switch the power on in the following procedure. Always follow this procedure at power-on.
1) Turn off the servo-on (SON).
2) Make sure that command and start signal from the controller are not input.
3) Switch on the control circuit power supply.
At power-on, "888" appears instantaneously, but it is not an error.
In the position control mode, data is displayed in 2[s] or later after displaying "CL" (cumulative
feedback pulses in pulse unit) (initial value), or by pressing the "MODE", "UP" or "DOWN" button.
Displayed contents differ depending on each control mode. Refer to section 5.3 for details.
4) Switch on the main circuit power supply.
(b) Power-off
1) Make sure that command and start signal from the controller are not input.
2) Turn off the servo-on (SON).
3) Switch off the main circuit power supply.
4) Switch off the control circuit power supply.
(3) I/O signal wiring check during the energization
Input signal wiring confirmation
On/off status of the input signals of CN1 connector can be checked using the external I/O signal display.
By using this function, input signal wiring can be checked. (Refer to section 5.8.)
Output signal wiring confirmation
Output signals of CN1 connector can be turned on/off forcibly using the DO output. By using this function,
output signal wiring can be checked. (Refer to section 5.9.)
(4) Parameter setting
POINT
Some parameters are made valid when power is switched off, then on after
setting. Refer to chapter 4 for details.
For the positioning mode, refer to section 13.7.
Set the parameters as necessary, such as selecting the control mode and the regenerative option.
In the position control mode, the servo amplifier can be used just by changing the basic setting parameters
(parameter No. PA ) mainly.
As necessary, set the gain/filter parameters (parameter No. PB ), the extension setting parameters
(parameter No. PC ) and the I/O setting parameters (parameter No. PD ).
For the internal speed control mode and the internal torque control mode, refer to chapter 4.
Содержание MELSERVO-JN Series
Страница 31: ... 22 MEMO ...
Страница 49: ...2 6 2 INSTALLATION MEMO ...
Страница 181: ...5 30 5 DISPLAY AND OPERATION SECTIONS MEMO ...
Страница 199: ...6 18 6 GENERAL GAIN ADJUSTMENT MEMO ...
Страница 251: ...9 4 9 DIMENSIONS 2 SCR connector system 3M Receptacle 36210 0100PL Shell kit 36310 3200 008 Unit mm 34 8 39 5 22 4 11 0 ...
Страница 303: ...11 46 11 OPTIONS AND PERIPHERAL EQUIPMENT MEMO ...
Страница 351: ...12 48 12 SERVO MOTOR MEMO ...
Страница 445: ...13 94 13 POSITIONING MODE MEMO ...