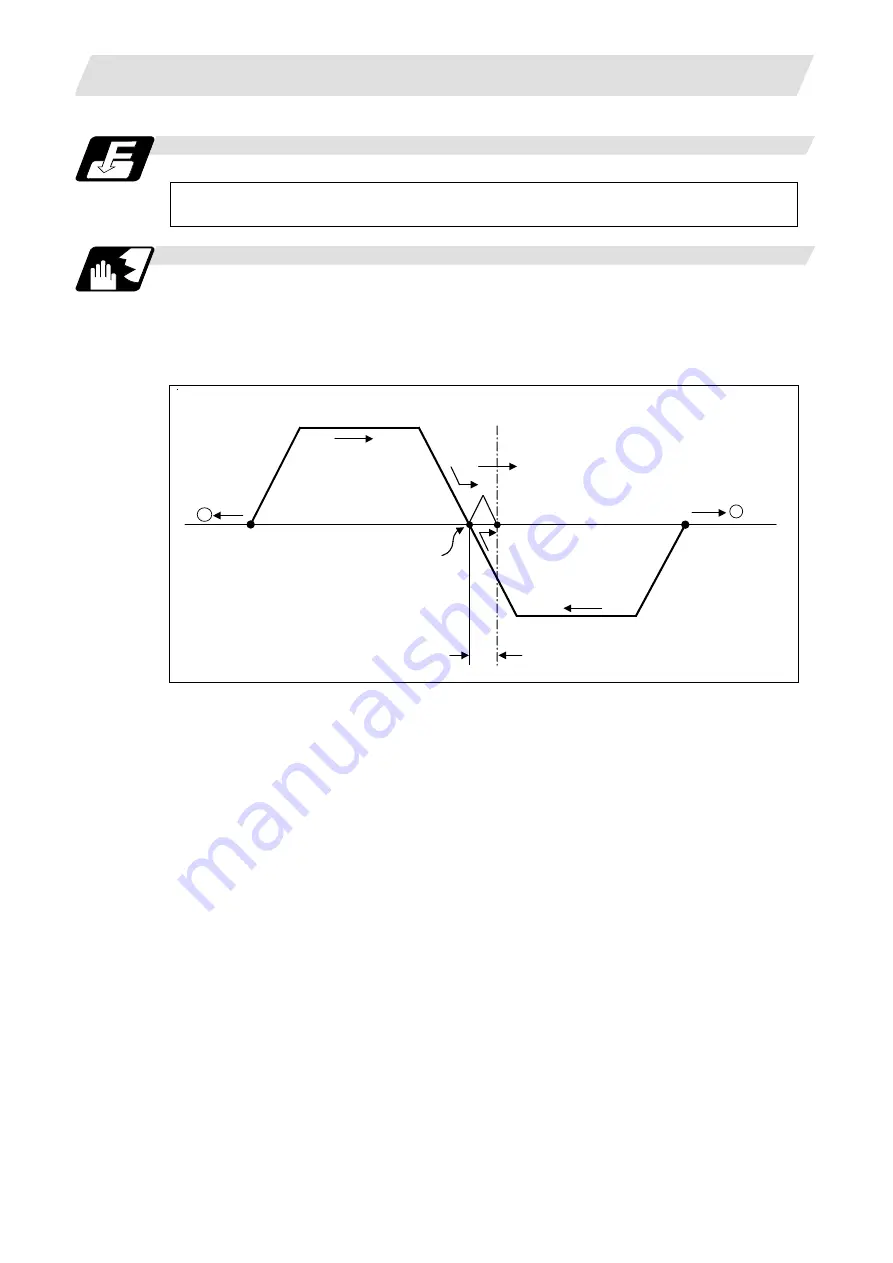
6. Interpolation Functions
6.8 Unidirectional Positioning
62
Command format
G60 X__ Y__ Z__
α
__ ;
α
: Optional axis
Detailed description
(1) The creep distance for the final positioning as well as the final positioning direction is set by
parameter.
(2) After the tool has moved at the rapid traverse rate to the position separated from the final
position by an amount equivalent to the creep distance, it move to the final position in
accordance with the rapid traverse setting where its positioning is completed.
Start point
Start point
End point
G60a
Stop once
Positioning position
[Final advance direction]
G60-a
[G60creep distance]
+
-
(3) The above positioning operation is performed even when Z axis commands have been
assigned for Z axis cancel and machine lock. (Display only)
(4) When the mirror image function is ON, the tool will move in the opposite direction as far as the
intermediate position due to the mirror image function but the operation within the creep
distance during its final advance will not be affected by mirror image.
(5) The tool moves to the end point at the dry run speed during dry run when the G0 dry run
function is valid.
(6) Feed during creep distance movement with final positioning can be stopped by resetting,
emergency stop, interlock, feed hold and rapid traverse override zero.
The tool moves over the creep distance at the rapid traverse setting. Rapid traverse override is
valid.
(7) Uni-directional positioning is not performed for the drilling axis during drilling fixed cycles.
(8) Uni-directional positioning is not performed for shift amount movements during the fine boring
or back boring fixed cycle.
(9) Normal positioning is performed for axes whose creep distance has not been set by
parameter.
(10) Uni-directional positioning is always a non-interpolation type of positioning.
(11) When the same position (movement amount of zero) has been commanded, the tool moves
back and forth over the creep distance and is positioned at its original position from the final
advance direction.
(12) Program error (P61) results when the G60 command is assigned with an NC system which
has not been provided with this particular specification.