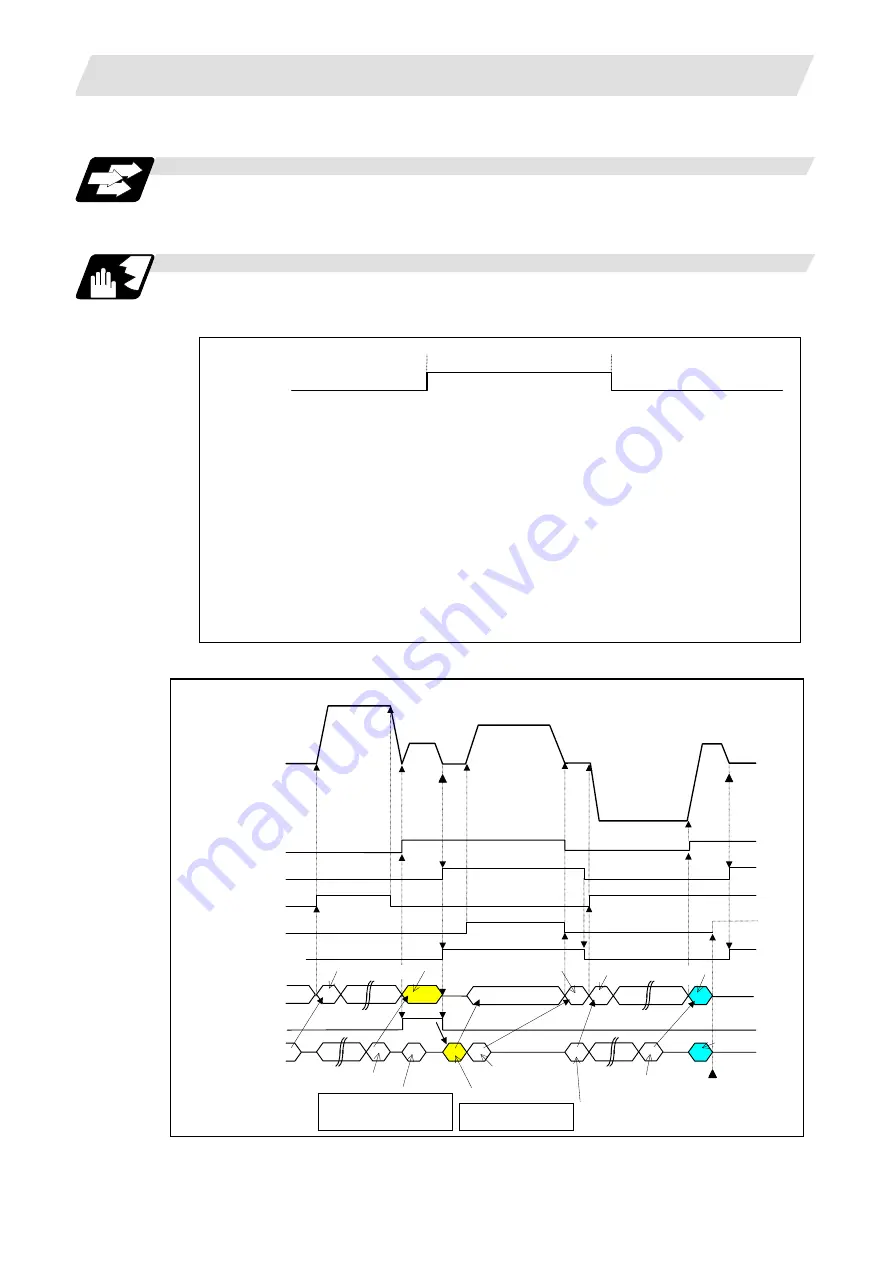
10. Spindle Functions
10.5 Spindle/C Axis Control
154
10.5 Spindle/C Axis Control
Function and purpose
This function enables one spindle (MDS-A/B-SP and later) to also be used as a C axis (rotation
axis) by an external signal.
Detailed description
(1) Spindle/C axis changeover
Changeover between the spindle and C axis is done by the C axis SERVO ON signal.
At servo OFF ................. Spindle (C axis control not possible)
At servo ON ................... C axis (spindle control not possible)
The C axis is in a reference position return incomplete state.
C axis
Spindle
Spindle
Servo ON
•
Reference position return state
Reference position return is incomplete when the Z phase has not been passed.
Reference position return is complete when the Z phase has been passed.
•
C axis position data
The NC's internal C axis position data is updated even for the spindle rotation
during spindle control.
The C axis coordinate position counter is held during spindle control, and is
updated for the amount moved during spindle control when the C axis servo
READY is turned ON. (The C axis position at servo ON may differ from the
position just before the previous servo OFF.)
(2) Changeover timing chart example
∗
2
Reference position
return complete status
Blocks being calculated
Recalculation request
Blocks being executed
C axis command
(automatic operation)
Spindle forward run/
reverse run start
Servo ON
Servo READY
Motor speed
C axis
movement
Program error
(P430)
Reference position
return complete
Reference position return complete
Orientation
Orientation
Spindle
reverse run
Reverse
run
∗
2
∗
1
∗
1
Forward
run
Spindle
forward run
C axis command
Servo ON
C axis command
C axis command
recalculation
Servo OFF
Spindle
reverse
run
C axis
command
Spindle forward
Spindle reverse run
Servo ON
Servo OFF
Servo ON
Servo ON
Program error because the
reference
position
return is
incomplete at this calculation.
Reference
position
return
complete at recalculation