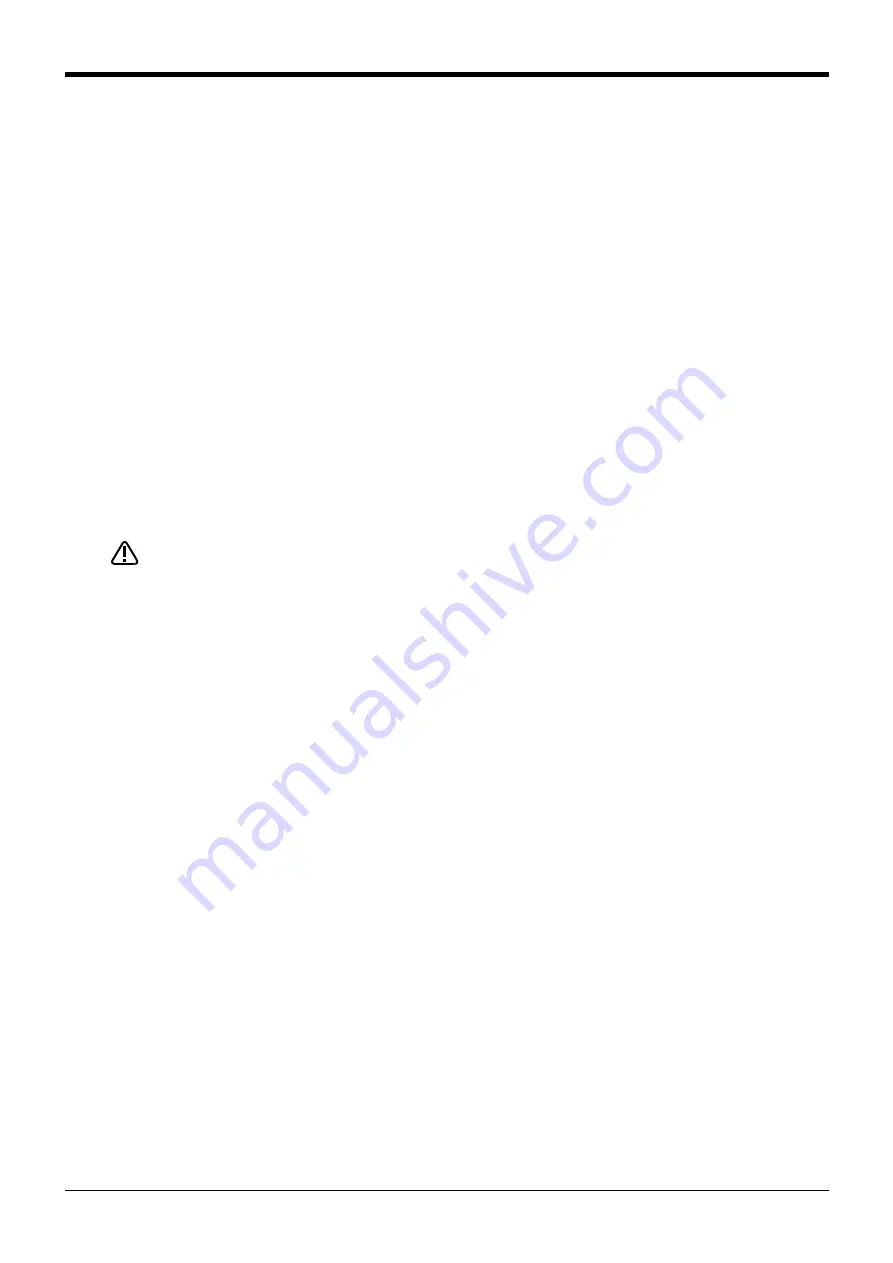
Detailed explanation of command words
4-265
(14) The filter characteristics applied on the acceleration/deceleration movement can be changed with <Fil-
ter length>. Increase the filter length to make the movement during acceleration and deceleration
smoother. Note that if the filter length is too high, the movement will slow down and it will take a long
time for the spline interpolation to end.
(15) If a signal output is set for the path point data, the general purpose output signal will be output with the
designated conditions when passing through the target path point.
(16) If the robot positioning complete condition is specified (Fine command, Fine J command, or Fine P
command), positioning completion will be confirmed at the spline interpolation end position.
(17) Even if continuous movement is designated with the Cnt command, continuous movement will not take
place at the spline interpolation start position and end position.
(18) Even if "Stop type 1" is designated for the Def Act command (interrupt condition and process definition),
if an interrupt occurs during the spline interpolation, the robot will stop with the same deceleration as
"Stop type 2".
(19) The additional axis will not move from the spline interpolation start position. Even if an additional axis
position is set for one of the interim path points, it will not be used during spline interpolation.
(20) Step feed can be executed for the MvSpl command, but step return cannot be executed. Error L2612
(Cannot execute step return) will occur.
(21) The mechanism’s control rights (GetM command) are required to execute the MvSpl command.
(22) The MvSPl command cannot be executed in a slot where the start conditions are ALWAYS or ERROR.
Error L2612 (Can't execute with these start conditions) will occur.
(23) If a value outside the setting range is set for the MvSpl command argument, error L3110 (Argument
value is out of range (MvSpl)) will occur.
If an <Acceleration/deceleration distance> too short for the <Speed> is designated,
sudden acceleration/deceleration will take place and could cause robot vibration or
a servo error. Always set an appropriate acceleration/deceleration distance.
Related instructions]
SetCalFrm (Set Calibration Frame)
[Related system variables]
M_SplPno, M_SplVar
CAUTION