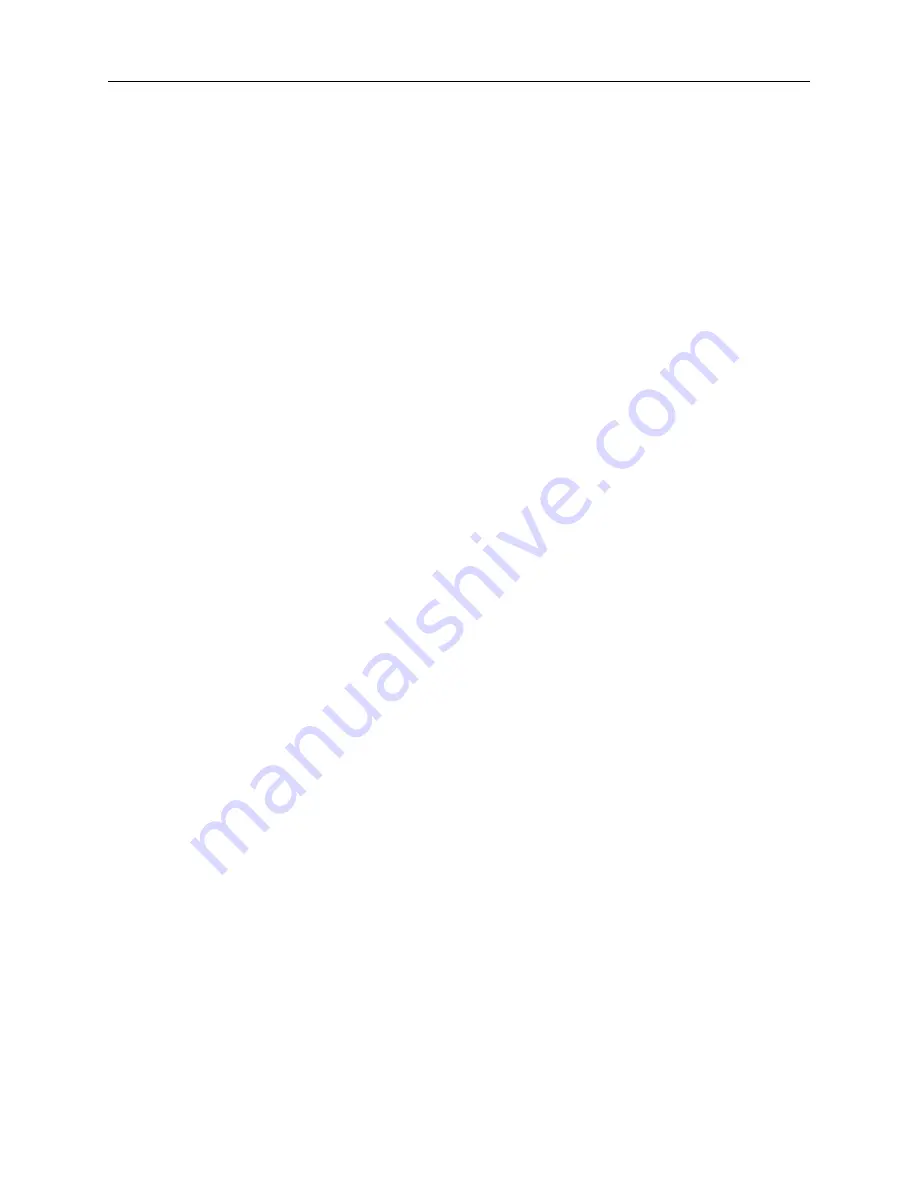
Servo Control Card
7 - 3
Flow Rate Integrator Circuit U29.
The output of U26B is summed with the Flow Rate command to effec-
tively reduce the input voltage to U29. This action results in the reduc-
tion of the Flow Rate command signal, thereby preventing the
selected pressure limit from being exceeded.
Inverting amplifier, U27B.
The output of this amplifier is summed with the output of the Main
Flow Integrator, to reduce the voltage sent to the error amplifier U27D,
thereby decreasing the error signal.
Circuit Q4.
This circuit is driven to cut-off, sending a pressure limit indication sig-
nal (PRESLIMIND) to PIO3 (U16), and eventually to the CPU. This
PRESLIMIND signal will also send Q12 into a saturation state, which
shunts R81 and reduces the gain of the error amplifier, thereby
decreasing the error signal.
Overpressure Circuit
If the actual pressure exceeds the pressure limit command by greater
than 100-150 PSI, the Overpressure Circuit (U26D) forwards an
OPLIM signal to stop the injection.
Flow Scale Circuit
Using the two flow scale signals, circuits Q5, Q6, and Q11 attenuate
the flow rate selected signal during ML/MIN and ML/HR flow scale
injections.
Standby Reset
Circuit
Driven by the INJECT signal, Q8, Q9, and Q10 control the flow rate
integrator, U29. During standby, the integrator follows the position pot.
The output of the integrator is equal in amplitude, and opposite in
polarity to the position pot. When an injection is to occur, this circuit
allows U29 to generate the position command.
Flow Rate Integrator
The master position command is generated by integrator U29. The
output of this circuit is a ramp, with a slope proportional to the input
signal (flow rate selected).
Error Amplifier
When the plunger is moving at the desired flow rate, the master posi-
tion command from U29 and the pot wiper signal from U27C are equal
but opposite in polarity. The output of error amplifier U27D is the dif-
ference between these two signals, or the position error. This error
signal is used by the drive circuits to power the motor. If pressure lim-
iting occurs, a signal from U27B reduces the error signal, and the gain
of U27D is reduced by Q12.
Feed Forward Circuit
This circuit, comprised of Q7 and U27A, provides a boost voltage to
the motor to compensate for the internal resistance of the motor. This
turning voltage varies with the Flow Rate.
Содержание ProVis Mark V
Страница 1: ...Service Manual KMP 870 98411 T 205 Rev D...
Страница 2: ......
Страница 3: ......
Страница 4: ......
Страница 15: ...Operating Guide 3 1 3 Operating Guide...
Страница 16: ...Mark V ProVis Injection System 3 2...
Страница 30: ...Mark V ProVis Injection System 7 4 Figure 7 1 Block Diagram Servo Control Card...
Страница 31: ...Servo Control Card 7 5...
Страница 37: ...Mark V ProVis Injection System 9 4 Figure 9 1 Block Diagram Control Panel Digital Logic...
Страница 39: ...Mark V ProVis Injection System 9 6 Figure 9 2 Block Diagram Control Panel DC to DC Converter...
Страница 49: ...Mark V ProVis Injection System 10 10 NOTES...
Страница 60: ...Injector Head 13 7 Figure 13 1 Block Diagram Head Card...
Страница 61: ...Mark V ProVis Injection System 13 8 NOTES...
Страница 64: ...Imaging System Interface 14 3 Figure 14 1 Connector Locations...
Страница 67: ...Mark V ProVis Injection System 14 6 Figure 14 2 Block Diagram Imaging System Interface...
Страница 71: ...Mark V ProVis Injection System 14 10 NOTES...
Страница 107: ...Mark V ProVis Injection System 15 36 NOTES...