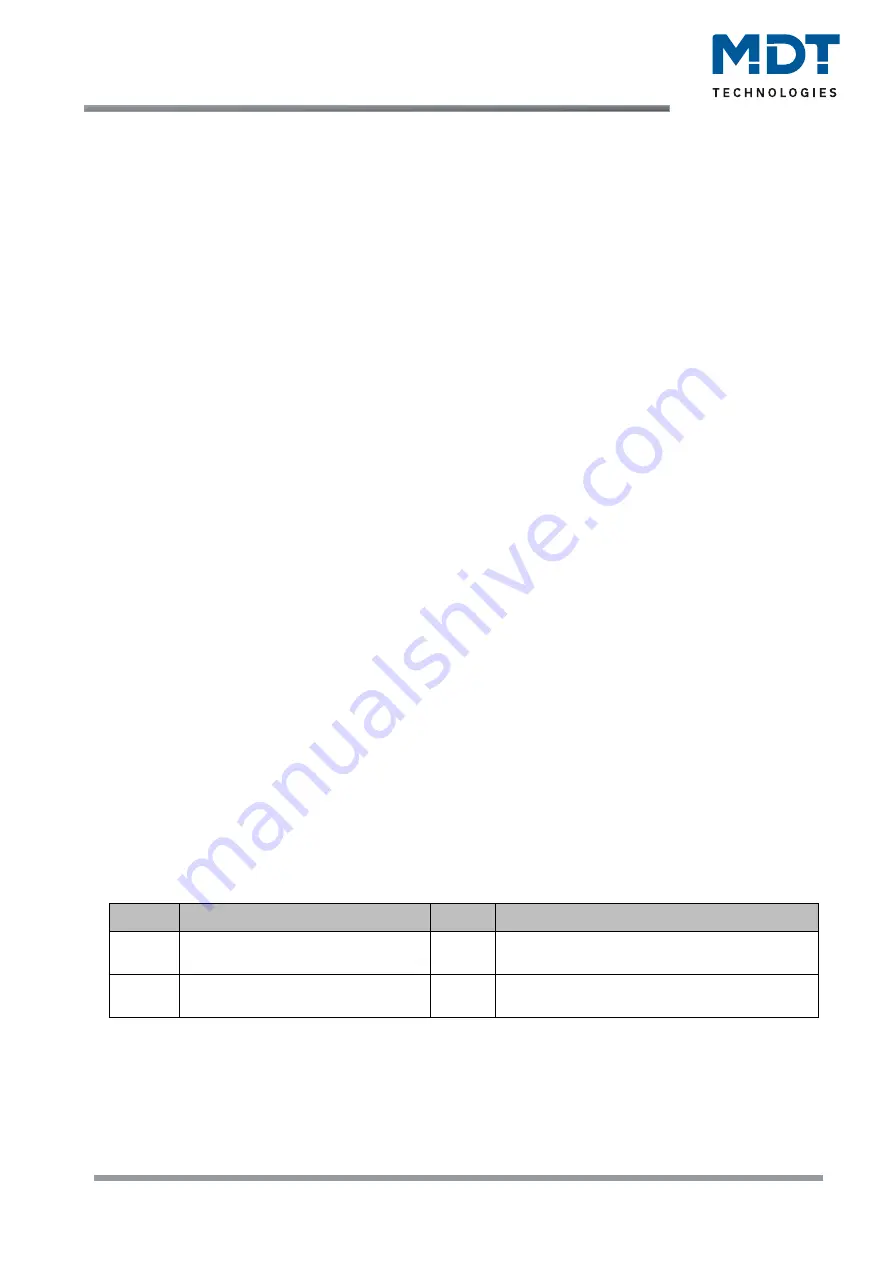
Technical Manual
Glass Room Temperature Controller Smart SCN-RTRGx.02
MDT technologies GmbH •
51766 Engelskirchen • Papiermühle 1
•
Germany
Phone: +49-2263-
880 • [email protected] • www.mdt.de
64
64
The system used can be selected via the "
System
" setting. If there is a common system for the
cooling & heating process, the setting 2 pipe/1 circuit is to be selected. If the cooling process and
heating process are controlled by two individual units, the setting 4 pipe/2 circuit is to be selected.
With the setting “
Switchover
Heating/Cooling
” It is also possible to select between manual
switching between “Heating” and “Cooling” via an object and automatically via the temperature.
2 Pipe system (2 pipe/1 circuit):
In a common pipe system for the cooling and heating process, there is only one communication
object that controls the control value. The change from
“Heating” to “Cooling” or from “Cooling to
Heating” is made by a changeover. This can also be used simultan
eously for changing between
heating and cooling medium in the system. This ensures, for example, that warm water flows in a
heating/cooling ceiling during “Heating” and cold water during “Cooling”. In this case only one
common controller (PI, PWM or 2-point) can be selected for the control value. The direction of
action can also only be defined identically for both processes. However, the individual control
parameters for the selected controller can be parameterized independently of each other.
4 Pipe system (4 pipe/2 circuit):
If there is a separate pipe system for the heating and cooling process, both processes can also be
parameterized separately. Consequently, separate communication objects exist for both control
values. This makes it possible to control the heating process e.g. via a PI control and the cooling
process e.g. via a 2-step control, as both processes can be controlled by different devices. For each
of the two individual processes, completely individual settings for the control value and the
heating/cooling system are therefore possible.
Switchover
Heating/Cooling:
Using this setting, it is possible to set whether the controller automatically switches between
“Heating” and “Cooling”
or whether this process is to be carried out manually via a communication
object. With automatic switchover, the controller evaluates the setpoints and knows which mode it
is currently in based on the set values and the current actual temperature. If, for example, “Heating”
was previously active, the controller switches over as soon as the setpoint for the cooling process is
reached. As long as the controller is in the dead zone, the controller remains set to “Heating”, but
does not heat as long as the setpoint for the heating process is not exceeded.
If the switchover "via object" is selected, an additional communication object is displayed via which
the switchover can be made. With this setting, the controller remains in the selected mode until it
receives a signal via the communication object. As long as the control
ler is in “Heating” mode, for
example, only the setpoint for the heating process is considered, even if the controller is actually
already in “Cooling” mode from the setpoints. A start of the cooling process is therefore only
possible when the controller receives a signal via the communication object that it should switch to
the cooling process. If the controller receives a 1 via the communication object, the heating process
is switched on, with a 0 the cooling process.
The following table shows the associated communication objects:
Number Name/Function
Length Usage
32
Switchover Heating/Cooling
–
0=Cooling / 1=Heating
1 Bit
Switching between
“
Heating
”
and
“
Cooling
”
Mode:
33
Status Heating/Cooling
–
0=Cooling / 1=Heating
1 Bit
Sending the status whether
“
Heating
”
or
“
Cooling
”
mode.
Table 67: Communication objects
–
Heating/Cooling switchover