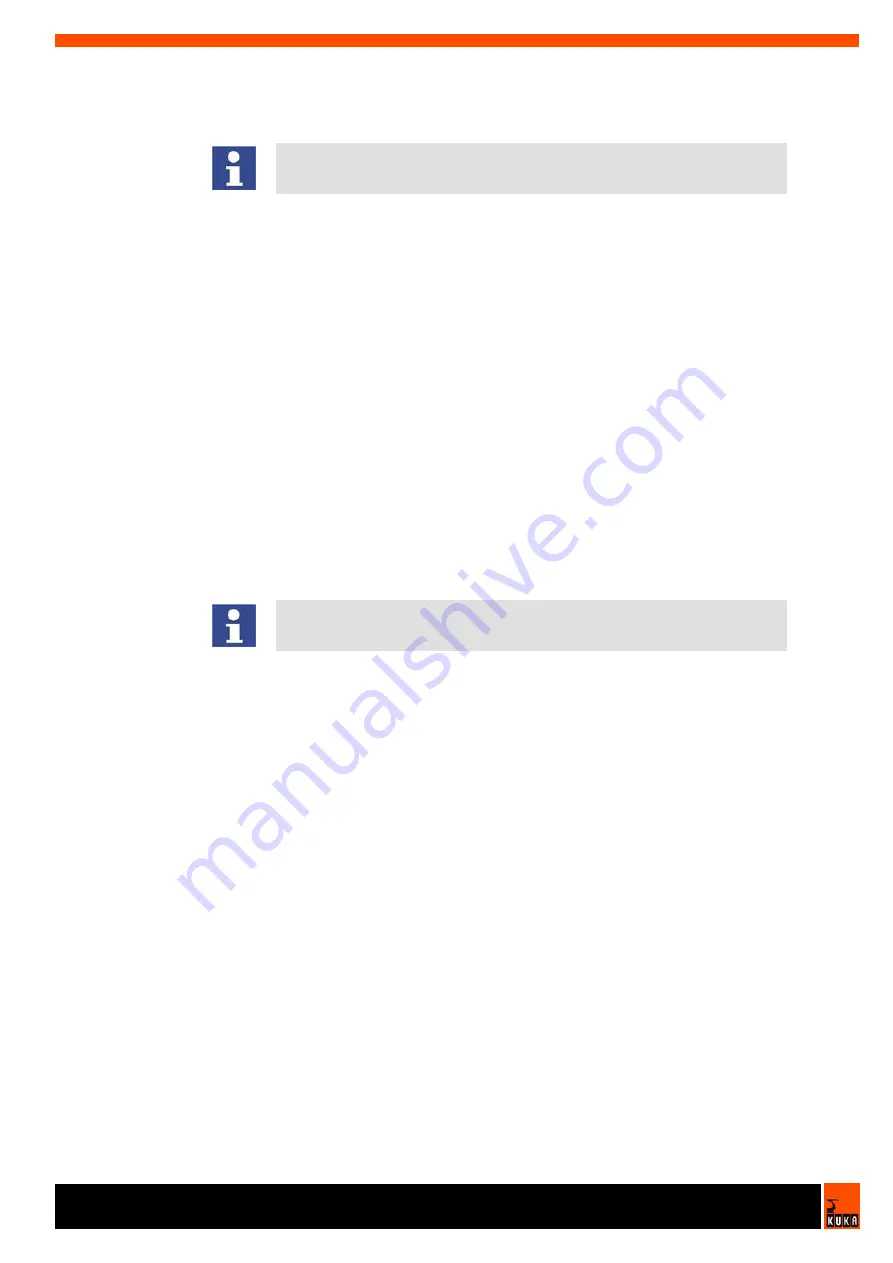
V3.3 11.07.2007 KRC-AD-KRC2ed05-BA en
4. Safety
4.3.12
KUKA.SafeRobot (option)
KUKA.SafeRobot is an option with software and hardware components.
Properties
Connection to an external safety logic
Monitoring that can be activated using safe inputs
Freely definable axis-specific monitoring
Safe monitoring of axis-specific and Cartesian velocities and accelerations
Safe standstill monitoring
Safe stop via Electronic Safety Circuit (ESC) with safe disconnection of the
drives
Monitoring of the mastering
Brake test
Functional principle
The robot moves within the limits that have been configured and activated.
The actual position is continuously calculated and monitored against the safe-
ty parameters that have been set.
The SafeRDC monitors the robot system by means of the safety parameters
that have been set. If the robot violates a monitoring limit or a safety parame-
ter, it is stopped.
The safe inputs and outputs of the SafeRDC are of a redundant design and
LOW active.
4.4
Personnel
User
The user of a robot system is responsible for its use. The user must ensure
that it can be operated in complete safety and define all safety measures for
personnel.
System integrator
The robot system is safely integrated into a plant by the system integrator.
The system integrator is responsible for the following tasks:
Installing the robot system
Connecting the robot system
Implementing the required facilities
Issuing the declaration of conformity
Attaching the CE mark
Operator
The operator must meet the following preconditions:
The operator must have read and understood the robot system documen-
tation, including the safety chapter.
The operator must be trained for the work to be carried out.
Work on the robot system must only be carried out by qualified personnel.
These are people who, due to their specialist training, knowledge and ex-
perience, and their familiarization with the relevant standards, are able to
assess the work to be carried out and detect any potential dangers.
This option may only be retrofitted after consultation with the KUKA Robot
Group.
Further information is contained in the KUKA System Technology
KU-
KA.SafeRobot
documentation.
Содержание KR C2 edition05
Страница 8: ...8 157 V3 3 11 07 2007 KRC AD KRC2ed05 BA en KR C2 edition05...
Страница 42: ...42 157 V3 3 11 07 2007 KRC AD KRC2ed05 BA en KR C2 edition05 2 9 2 KCP connector X19 Connector pin allocation...
Страница 72: ...72 157 V3 3 11 07 2007 KRC AD KRC2ed05 BA en KR C2 edition05 Connector pin allocation...
Страница 76: ...76 157 V3 3 11 07 2007 KRC AD KRC2ed05 BA en KR C2 edition05...
Страница 84: ...84 157 V3 3 11 07 2007 KRC AD KRC2ed05 BA en KR C2 edition05...
Страница 157: ...157 157 V3 3 11 07 2007 KRC AD KRC2ed05 BA en...