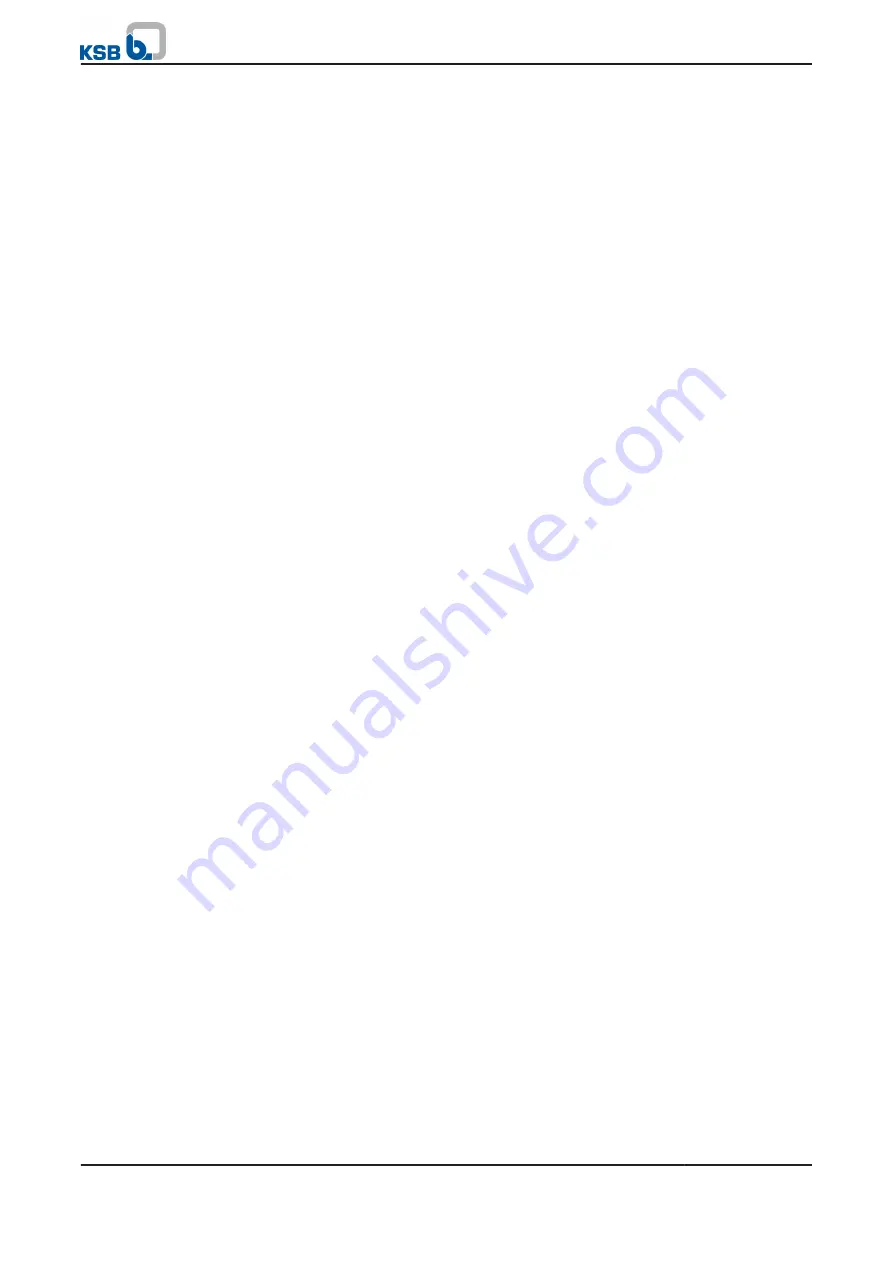
2. ID Selected PumpDrive
(3-1-1-4)
: The active master control panel can be used to
select the PumpDrive to which the control panel is connected. At the beginning
of parameterisation, 0 is displayed for all the PumpDrive IDs, as no PumpDrive IDs
have been assigned yet. When a PumpDrive is selected, its LED flashes. This
allows you to identify the PumpDrive to which the active master control panel is
connected.
3. PumpDrive ID
(3-2-1-2)
: Assignment of PumpDrive ID. KSB rule: Define the pump
on the left-hand side (active master control panel and main pump) as number 1,
then number consecutively from left to right. To do so, use ID Selected
PumpDrive
(3-1-1-4)
to switch to the relevant PumpDrive and then use
PumpDrive ID
(3-2-1-2)
to assign the relevant ID. Repeat these steps until an ID
has been assigned to every PumpDrive. After the IDs have been assigned, switch
to PumpDrive 1 so that the LED of the active master control panel flashes.
4. Multiple pump configuration role
(3-2-1-1)
: This parameter defines the role of
the respective PumpDrive in a multiple pump configuration. The system
automatically defines which PumpDrive becomes the main drive controlling the
main pump. Ensure that all PumpDrives which are not connected to sensors have
the Standard Slave role assigned to them.
5. Backup Guard Tm
(3-1-7-4)
: This parameter is used to define which Advanced
control panel assumes the active master function after voltage is supplied
simultaneously. The lowest time value that has been set activates the respective
Advanced control panel to be the active master control panel if all PumpDrives in
the system are cut in simultaneously. This time value has to be set on Pump 1
(active master control panel and main pump). Any further Advanced control
panels must then have a higher time value assigned to them. The other
Advanced control panels are thus defined as auxiliary master control panels in
the sequence given by the time frames and voltage supply.
6. AuxMain Guard Tm
(3-10-1-3)
: This parameter is used to define which PumpDrive
assumes the role of the main pump set after voltage has been applied
simultaneously. The lowest time value set activates the respective PumpDrive as
the main pump drive. This time value has to be set on Pump 1. The remaining
PumpDrives have to be assigned a higher time value. The other PumpDrive
Advanced units are thus defined as auxiliary main pumps in the sequence given
by the time frames.
7. Max. number of pumps running
(3-12-5-1)
: This parameter defines how many
PumpDrives can run simultaneously in a multiple pump configuration. The
maximum permissible number of PumpDrives equals the number of PumpDrives
connected to the KSB local bus. If there is a stand-by pump, the maximum
number of pumps has to be reduced by one. This parameter must be set to the
same value on every Advanced control panel in a multiple pump configuration,
since it is a local parameter of the individual control panels.
8. Pump changeover active
(3-12-5-5)
: If this parameter is enabled, pump
changeover will take place regularly after 24 hours of operation. A pump
changeover is also effected upon every change in the system start. Stand-by
pumps are included in the pump changeover cycle. This parameter must be set to
the same value on every Advanced control panel in a multiple pump
configuration, since it is a local parameter of the individual control panels.
9. Dig In 2 Function
(3-7-1-2)
: The function of digital input 2 has to be set to System
Start on the PumpDrive equipped with active master control panel/main pump,
as well as on the PumpDrive equipped with auxiliary master control panel/
auxiliary main pump. When digital input 2 is activated, the system starts.
10. System Reboot
(3-1-5-6)
: Restart multiple pump system. After parameterisation
has been completed, the multiple pump system has to be restarted via the active
master control panel using the System Reboot
(3-1-5-6)
parameter so that all the
set parameters are accepted.
General parameterisation of multiple pump configurations
In multiple pump configurations, the digital inputs, relay outputs and analog outputs
must be parameterised individually for each PumpDrive. Activation of the warnings
for the analog inputs has to be enabled separately for each PumpDrive. Limits and
7 Commissioning/shutdown
PumpDrive
65 of 162