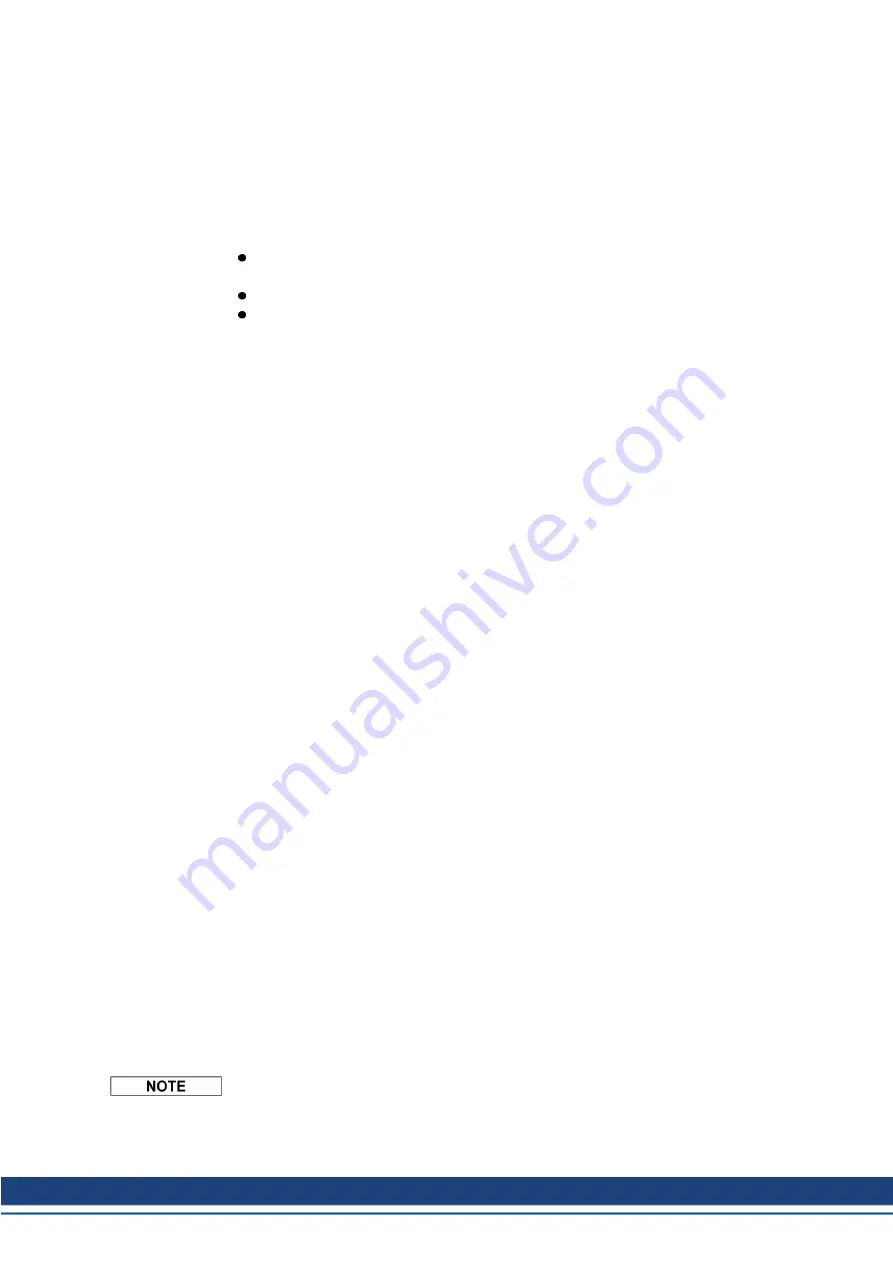
7.13 Dynamic Braking
Dynamic braking is a method to slow down a servo system by dissipating the mechanical
energy driven by the motor back EMF. The AKD has a built in advanced dynamic braking
mode which operates fully in hardware. When activated, the drive shorts the motor terminals
in phase with the back EMF (q axis) but continues to operate the non-force producing current
loop (d-axis) with 0 current. This forces all of the dynamic braking current to be stopping cur-
rent and insures the fastest stopping/amp of motor terminal current.
When current is not being limited, the mechanical energy is being dissipated in the motor
resistance.
When current is being limited, energy is returned to the drive bus capacitors.
The drive also limits the maximum dynamic braking motor terminal current via the
DRV.DBILIMIT
parameter to insure that the drive, motor, and customer load do not see
excessive currents/forces.
Whether and how the AKD uses dynamic braking depends on (
DRV.DISMODE
).
7.13.1 Regen circuit
When the amount of returned energy builds the bus capacitor voltage up enough the drive
activates the regen circuit to start dumping the returned energy in the regen resistor (also
called regenerative or brake resistor). This resistor could be internal or connected external to
the drive, depending on drive model and drive wiring.
AKD-x00306 to AKD-x00606, AKD-x04807
No internal regen resistor. Depending on the application requirements, an external resistor
can be connected.
AKD-x01206 to AKD-x02406 and AKD-x00307 to AKD-x02407
With internal resistor plus the ability to connect an external resistor depending on the applic-
ation requirements.
External regen resistors are described in the regional
AKD Accessories Manual
.
7.13.2 Functional description
When the amount of returned energy builds the bus capacitor voltage up enough the drive
activates the brake chopper to start dumping the returned energy in the regen resistor.
1. Individual drives, not coupled through the DC bus link circuit (+DC, -DC)
When the energy fed back from the motor has an average or peak power that exceeds the pre-
set level for the regen power rating, the drive generates the warning "n521 Regen Over
power”. If the power increases past the fault level, the regen circuit will switch off.
With the regen circuit switched off, the drive internal DC bus link voltage is supervised. The
drive reports an over-voltage fault if the DC bus threshold is exceeded. The drive power
stage is disabled and the load coasts to a stop with the fault message “F501 Bus Over
voltage" (
# 202). The Fault contact (terminals X8/9-10) is opened (
# 160) due to this
fault.
2. Several drives coupled through the DC bus link (+DC, -DC)
Using the built-in regen circuit, several drives of the same series can be operated from a com-
mon DC-bus link (
# 108), without any additional measures. 90% of the combined power of
all the coupled drives is always available for peak and continuous power. The switch-off on
over voltage takes place as described under 1. (above) for the drive that has the lowest
switch-off threshold (resulting from tolerances).
Observe the regeneration time (some minutes) after full load with peak regen power.
AKD Installation | 7 Technical description and data
Kollmorgen | kdn.kollmorgen.com | October 2017
43
Содержание AKD series
Страница 162: ...AKD Installation 9 Electrical Installation Wiring diagram X24 162 Kollmorgen kdn kollmorgen com October 2017 ...
Страница 179: ...9 20 6 CAN Bus Wiring AKD Installation 9 Electrical Installation Kollmorgen kdn kollmorgen com October 2017 179 ...
Страница 214: ... AKD Installation 11 Index 214 Kollmorgen kdn kollmorgen com October 2017 ...