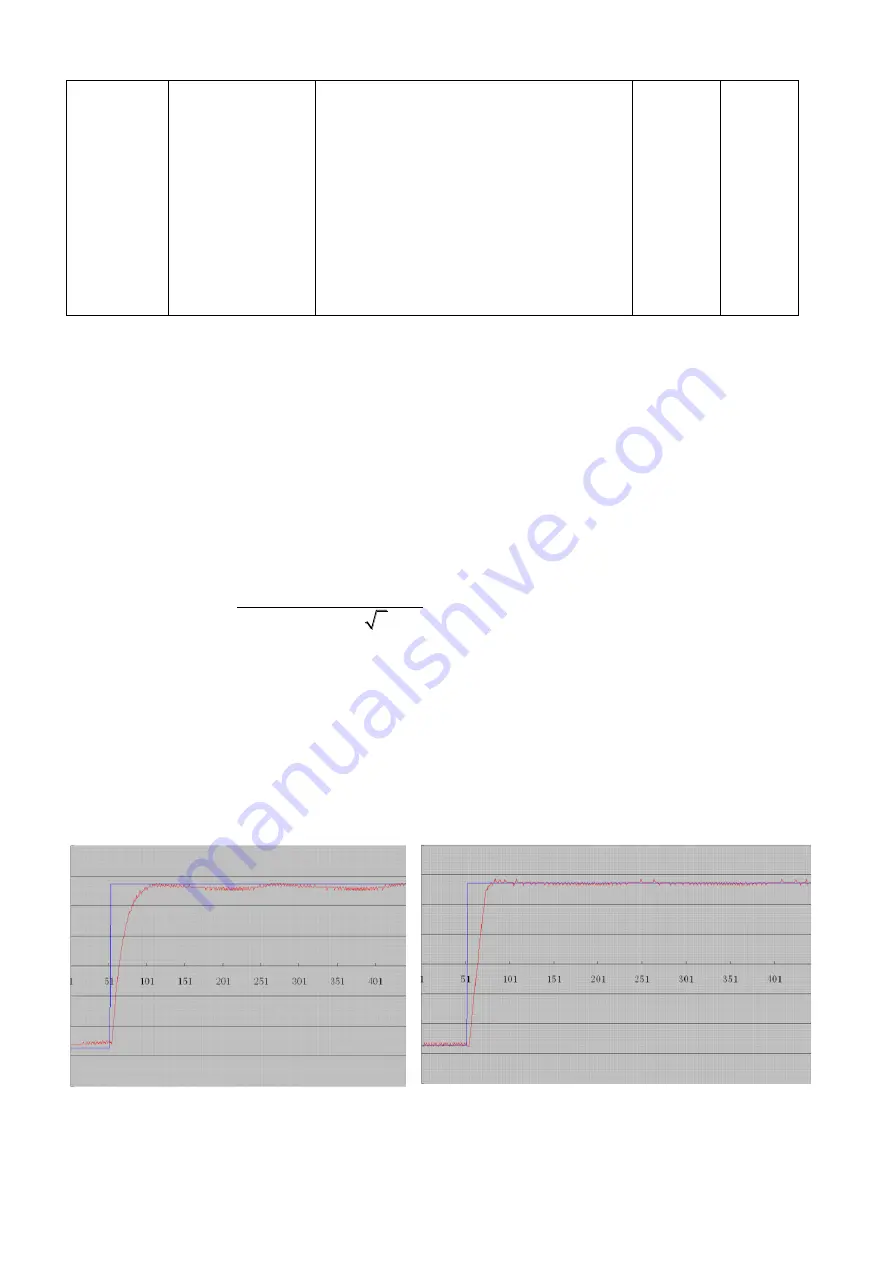
91
d2.05
Speed_Fb_N
Reduces the noise during motor operation
by reducing the feedback bandwidth of
velocity loops (smoothing feedback signals
of encoders). When the set bandwidth
becomes smaller, the motor responds
slower.
The formula is F=Speed_Fb_N*20+100.
For example, to set the filter bandwidth to
"F = 500 Hz‖, you need to set the
parameter to 20.
7
0~45
Proportional gain of velocity loop Kvp: If the proportional gain of the velocity loop increases, the responsive
bandwidth of the velocity loop also increases. The bandwidth of the velocity loop is directly proportional to the
speed of response. Motor noise also increases when the velocity loop gain increases. If the gain is too great,
system oscillation may occur.
Integral gain of velocity loop Kvi: If the integral gain of the velocity loop increases, the low-frequency intensity
is improved, and the time for steady state adjustment is reduced; however, if the integral gain is too great,
system oscillation may occur.
Adjustment steps:
Step 1: Adjust the gain of velocity loop to calculate the bandwidth of velocity loop
Convert the load inertia of the motor into the inertia Jl of the motor shaft, and then add the inertia Jr of the
motor itself to obtain Jt = Jr + Jl. Put the result into the formula:
*
*
_
Vc_Loop_BW
Kvp *
* 204800000* 2 * 2
p
t
t
I
K
Encoder
R
J
To calculate the bandwidth of the velocity loop
Vc_Loop_BW
according to the adjusted the gain of velocity loop Kvp, only adjust Kvi according to actual
requirements.
Adjust the impact of Kvp and Kvi, as shown in Fig. 8-2.
For the effect of Kvp adjustment, see the first to the fourth from left of Fig. 8-2. Kvp gradually increases from
the first to the fourth from left. The value of Kvi is 0.
For the effect of Kvi adjustment, see the first to the fourth from right of Fig. 8-2. Kvi gradually increases from
the first to the fourth from right. The value of Kvp remains unchanged.
Left 1
Right 1
Содержание CD2S Series
Страница 7: ...7...
Страница 8: ...8 1 3 3 Power Brake and Encoder cable of Motors...
Страница 12: ...12 Fig 2 3 Installation direction...
Страница 15: ...15 3 1 2 Wiring Diagram Fig 3 1 Wiring diagram of CD2S driver...
Страница 16: ...16 3 1 3 X1 interface of CD2S Driver Fig 3 2 X1 interface Fig 3 3 Wiring diagram of X1 interface...
Страница 23: ...23 Fig 4 3 Separate regulation of bits...
Страница 82: ...82...
Страница 96: ...96 8 4 Debugging example 8 4 1 Oscilloscope 1 Enter oscilloscope 2 Parameters for Oscilloscope...
Страница 98: ...98 In Auto Reverse mode Kvp 110...
Страница 100: ...100 The oscilloscope is as following max following error is 69 inc Fig 2 Kpp 30 Vff 100...
Страница 101: ...101 The oscilloscope is as following max following error is 53 inc Fig 3 Kpp 30 Vff 50...
Страница 102: ...102 The oscilloscope is as following max following error is 230 inc...