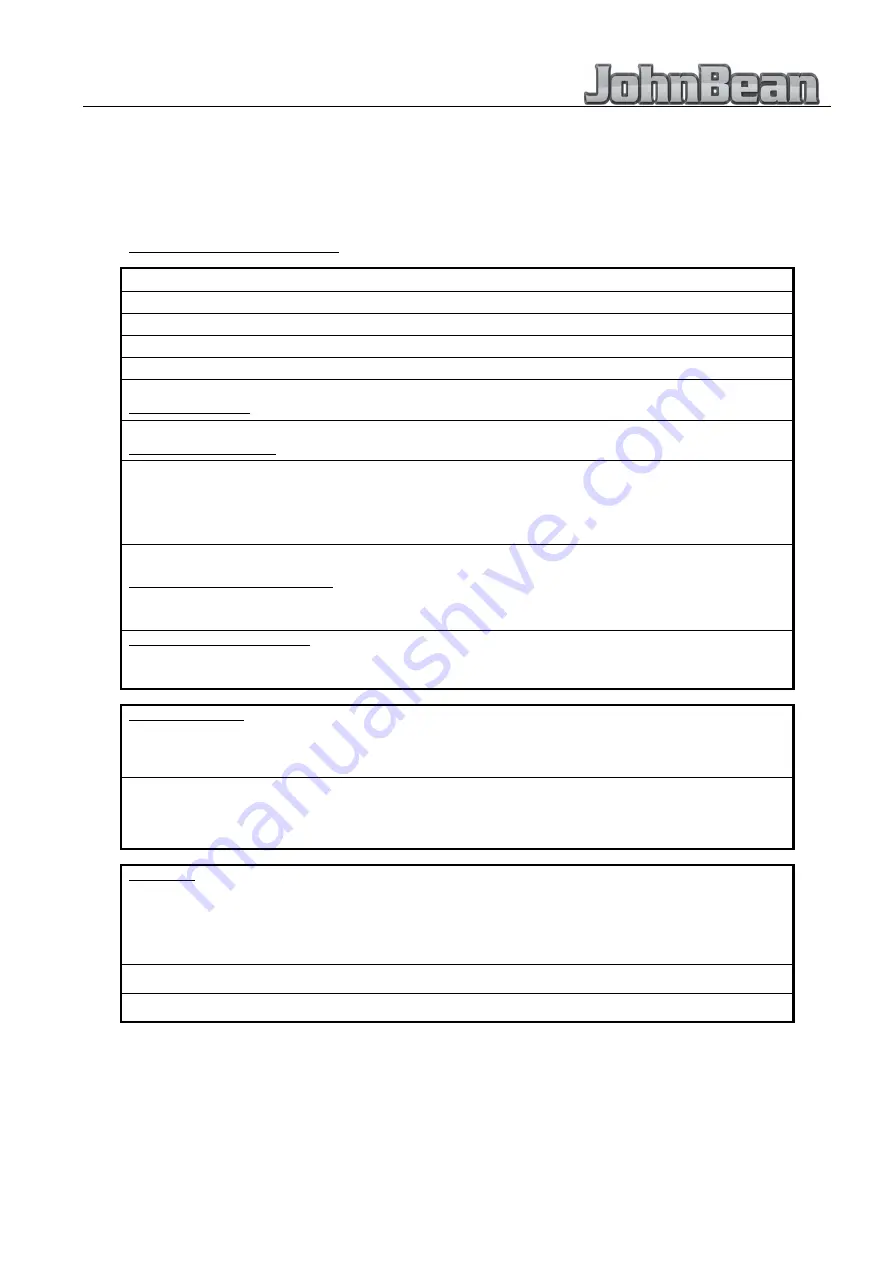
REV 02 OCT 2020 JLT4500-IOM-F
59
11.2 ANNUAL CHECKS
Check report
This report is record of all audits for operation conducted and recorded by an inspector or expert.
This lift was audited on DATE: ______________________________ and subjected to testing for operational readiness.
Describe deficiencies found (if any)
Extent of the Check:
Pending Checks (if any):
If there are (no*) concerns to limit this lift for operation. Additional verification is not required. (* = Delete if not applicable)
Place and Date
Inspector’s Signature
Name and address in block letters
Job Description and Company
Operator or Agent
Notes on defects
Place and Date
Signature
Issues Fixed
Place and Date
Signature
Verification
This Lift has been verified on _______________________________.
The unsatisfactory performance of the first examination has not been corrected?
Содержание JLT4500S
Страница 3: ...REV 02 OCT 2020 JLT4500 IOM F 3 ...
Страница 13: ...REV 02 OCT 2020 JLT4500 IOM F 13 Fig 3 General Specifications Service Bay Layout ...
Страница 46: ...REV 02 OCT 2020 JLT4500 IOM F 46 9 1 PARTS BREAKDOWN OF FINAL ASSEMBLY Fig 38 FINAL ASSEMBLY ...
Страница 49: ...REV 02 OCT 2020 JLT4500 IOM F 49 9 3 PARTS BREAKDOWN OF PARTS ON COLUMNS Fig 40 PARTS ON COLUMNS ...
Страница 52: ...REV 02 OCT 2020 JLT4500 IOM F 52 9 5 PARTS BREAKDOWN OF SYNCHRONIZING SYSTEM Fig 42 SYNCHRONIZING SYSTEM ...
Страница 54: ...REV 02 OCT 2020 JLT4500 IOM F 54 9 6 PARTS BREAKDOWN OF CARRIAGE AND ARMS ...
Страница 64: ...REV 02 OCT 2020 JLT4500 IOM F 64 Check Report Summary Description Date and Name ...
Страница 65: ...REV 02 OCT 2020 JLT4500 IOM F 65 12 ELECTRICAL DIAGRAM 12 1 WIRING DIAGRAM FOR THREE PHASES SHEET 1 3 ...
Страница 66: ...REV 02 OCT 2020 JLT4500 IOM F 66 12 2 WIRING DIAGRAM FOR SINGLE PHASE SHEET 2 3 ...
Страница 67: ...REV 02 OCT 2020 JLT4500 IOM F 67 12 3 WIRING DIAGRAM OF CONTROL BOXES SHEET 3 3 ...
Страница 68: ...REV 02 OCT 2020 JLT4500 IOM F 68 12 4 WIRING DIAGRAM OF THE ELECTRICAL SYSTEM ...
Страница 70: ...REV 02 OCT 2020 JLT4500 IOM F 70 13 FOUNDATION PLAN ...