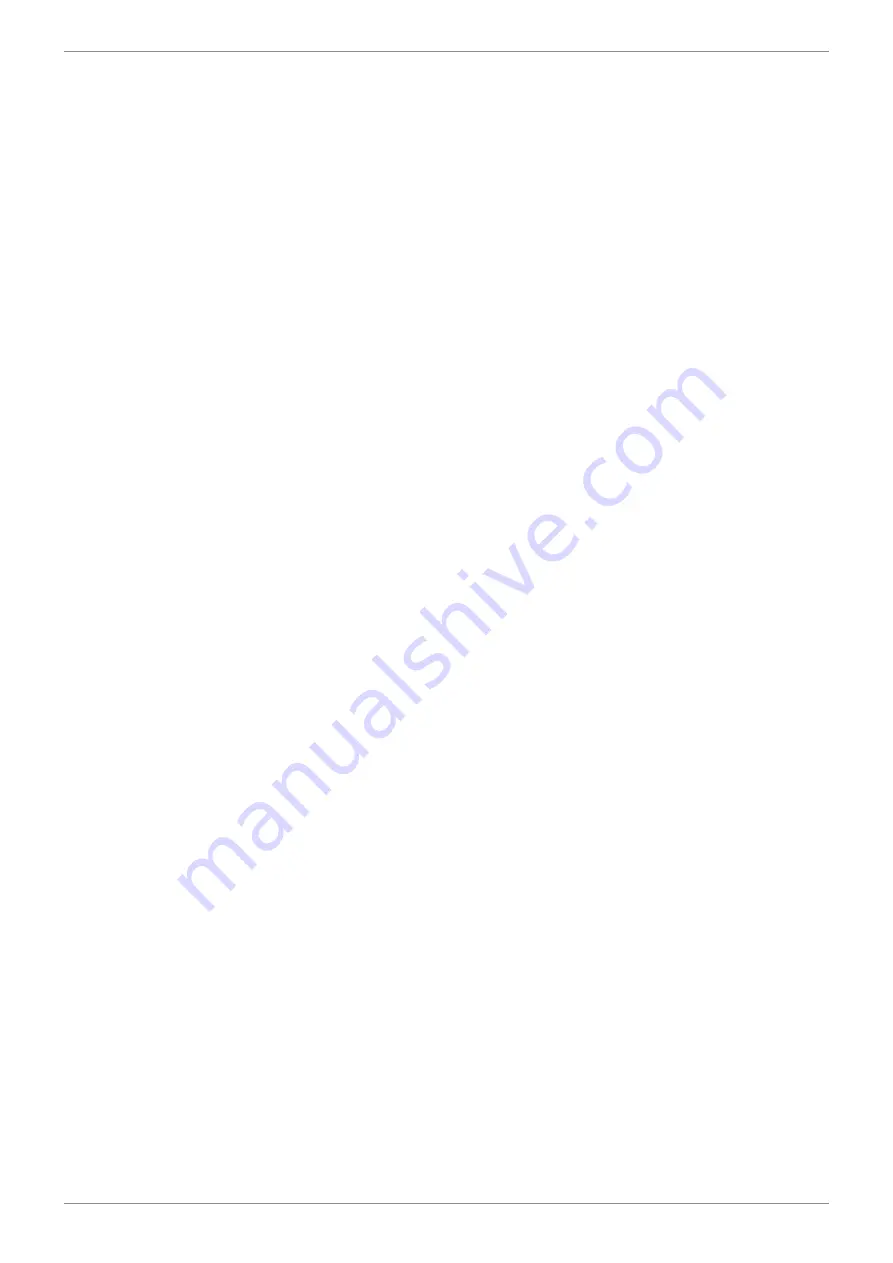
Jetter AG
Programming | 8
User Manual – JetControl 365MC
111 / 148
8.22 Motion control
The Motion Control is programmed in the Motion API interface in the program-
ming language STX.
The seamless integration of axis functions into the controller is an essential fea-
ture of the Jetter AG control technology. This makes point-to-point positioning
(PtP), technology functions (MC), as well as path control and certain robot func-
tions easy to realize. This universal motion controller is called
Motion Control
eXtended (MCX)
.
MCX features
■
Centralized generation of all command positions for single axes and axis
groups
■
Seamless integration into the controller
■
Jerk control to minimize machine vibrations
■
Online generation of cam discs
■
Combination of technology and path groups
■
Cascading of axis groups
■
Programming using SI units
■
Consideration of mechanical parameters
Amount of axes
JX2 system bus (CAN 1, X19):
■
Up to 16 servo amplifiers JM-100/JM-200 in PtP mode
■
6 axes max. in MCX mode
Jetter Ethernet system bus (X14/X15):
■
Up to 64 servo amplifiers JM-200-ETH in PtP mode
■
12 axes max. in MCX mode
Prerequisite:
The total number of axes must not exceed the maximum possible number of axes
of the controller.
Mixed operation of MCX axes via Ethernet and JX2 system bus is not supported.
Technology group
■
Virtual leading axis
■
External encoder as leading axis
■
Cascaded groups
■
Programming the whole group via leading axis
■
Dynamic coupling and decoupling of following axes
■
Print mark for high-precision position correction
■
Up to 6 active technology groups with up to 24 cams and 100 segments each