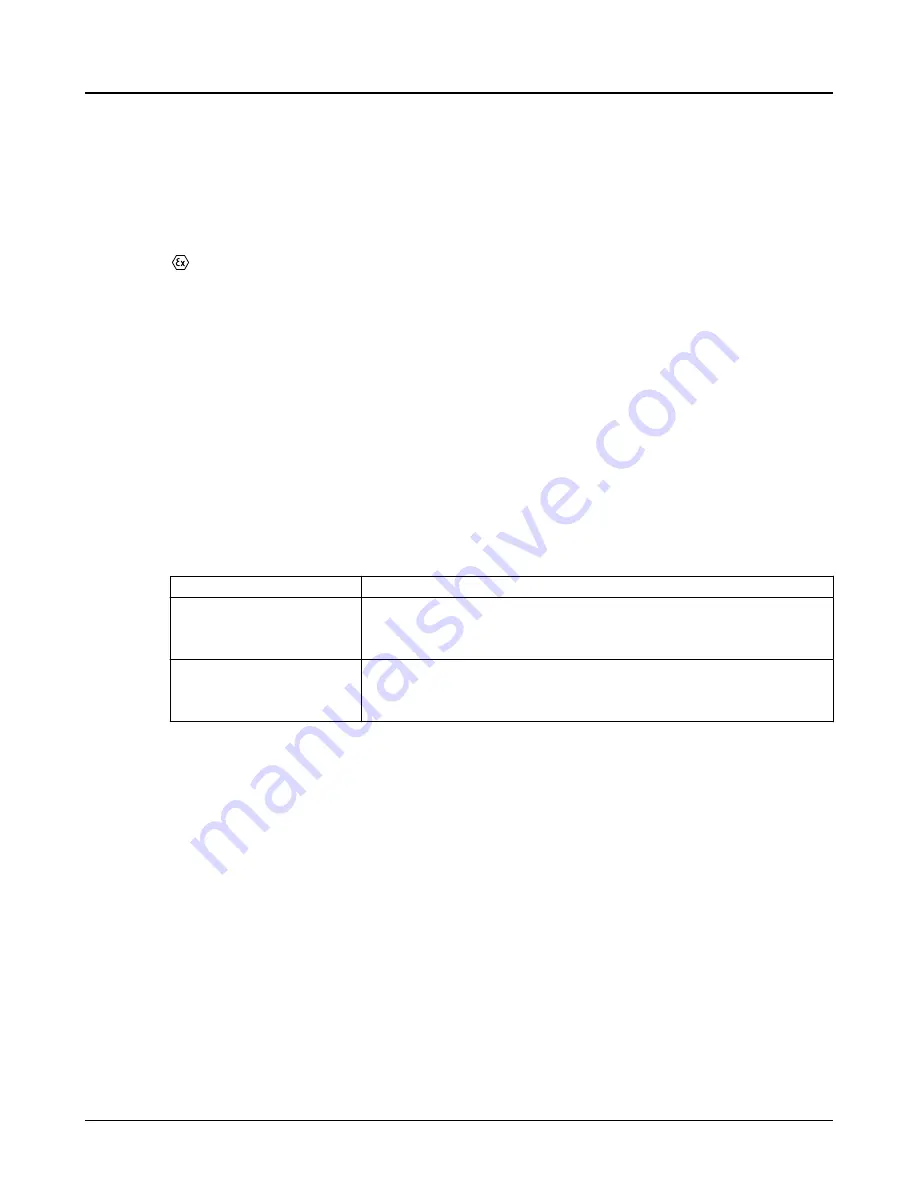
•
Beware of the starting jerk, which can be powerful.
•
Rinse the components in water after you disassemble the pump.
•
Do not exceed the maximum working pressure of the pump.
•
Do not open any vent or drain valve or remove any plugs while the system is pressurized. Make
sure that the pump is isolated from the system and that pressure is relieved before you disassem-
ble the pump, remove plugs, or disconnect piping.
•
Never operate a pump without a properly installed coupling guard.
•
The coupling guard used in an ATEX classified environment must be constructed from a non-
sparking material.
1.1.2.3.3 Hazardous liquids
The product is designed for use in liquids that can be hazardous to your health. Observe these rules
when you work with the product:
•
Make sure that all personnel who work with biologically hazardous liquids are vaccinated against
diseases to which they may be exposed.
•
Observe strict personal cleanliness.
•
A small amount of liquid will be present in certain areas like the seal chamber.
1.1.2.3.4 Wash the skin and eyes
1.
Follow these procedures for chemicals or hazardous fluids that have come into contact with your
eyes or your skin:
Condition
Action
Chemicals or hazardous fluids
in eyes
1.
Hold your eyelids apart forcibly with your fingers.
2.
Rinse the eyes with eyewash or running water for at least 15 minutes.
3.
Seek medical attention.
Chemicals or hazardous fluids
on skin
1.
Remove contaminated clothing.
2.
Wash the skin with soap and water for at least 1 minute.
3.
Seek medical attention, if necessary.
1.1.2.4 Ex-approved products
Follow these special handling instructions if you have an Ex-approved unit.
Personnel requirements
These are the personnel requirements for Ex-approved products in potentially explosive atmospheres:
•
All work on the product must be carried out by certified electricians and ITT-authorized mechanics.
Special rules apply to installations in explosive atmospheres.
•
All users must know about the risks of electric current and the chemical and physical characteristics
of the gas, the vapor, or both present in hazardous areas.
•
Any maintenance for Ex-approved products must conform to international and national standards
(for example, IEC/EN 60079-17).
ITT disclaims all responsibility for work done by untrained and unauthorized personnel.
Product and product handling requirements
These are the product and product handling requirements for Ex-approved products in potentially explo-
sive atmospheres:
1.1 Introduction and Safety
3175 Installation, Operation and Maintenance Instructions
7
Содержание Goulds Pumps 3175
Страница 1: ...Installation Operation and Maintenance Instructions 3175 ...
Страница 2: ......