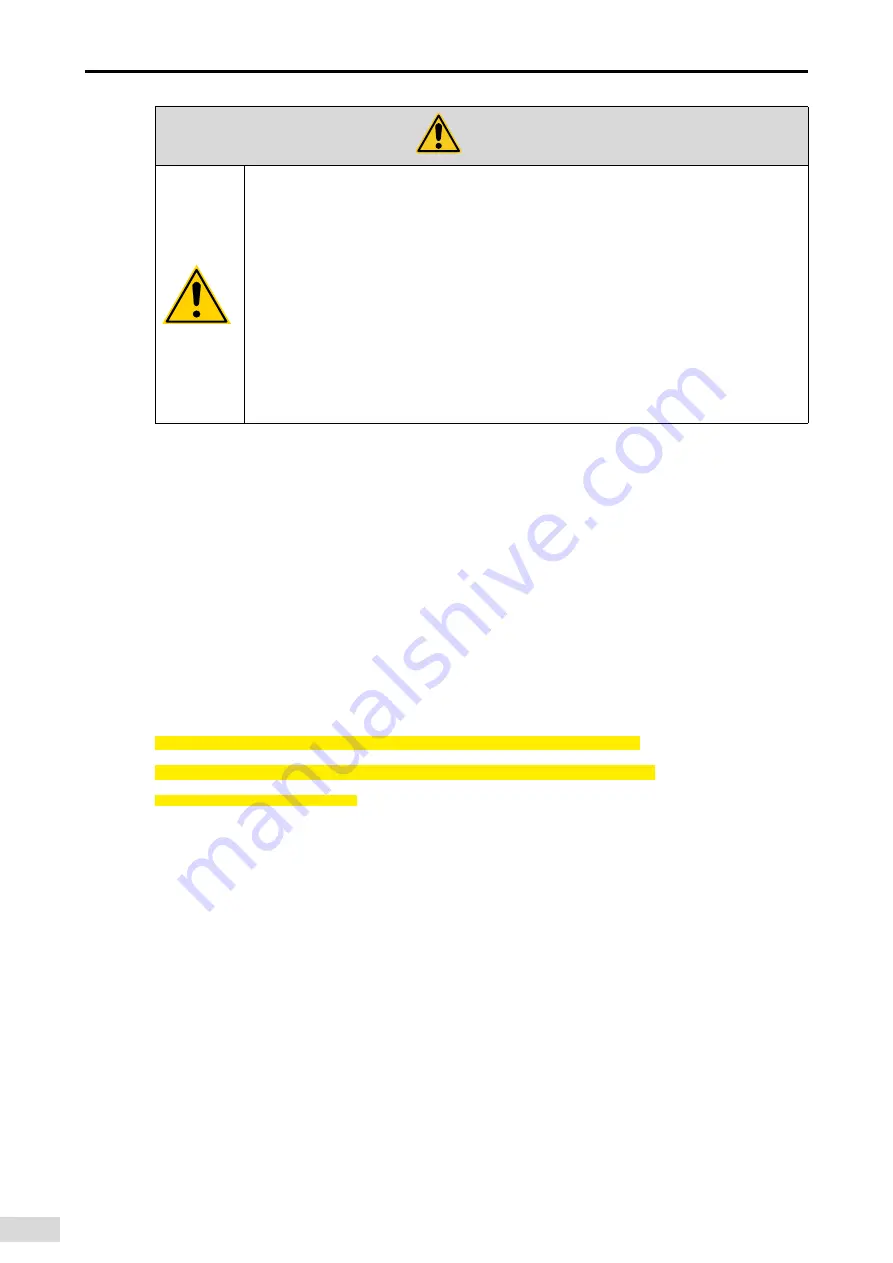
-424-
11 Appendix
8"3/*/(
◆
The design of safety-related systems requires specialist knowledge. To ensure that a complete
control system is safe, the whole system needs to be designed according to recognized safety
principles. The use of individual sub-systems such as drives with STO function, which are
intended for safety-related applications, does not in itself ensure the safety of the complete
system.
◆
The STO function can be used for stopping the servo drive in emergency stop situations.
◆
In normal operating mode, it is recommended not to stop the servo drive by using the STO
function. If a drive running is stopped by using STO, the drive perform a coast to stop. If this is
not acceptable, the system must be stopped using the correct mode instead of the STO function.
◆
This publication is a guide to the application of Inovance STO function, and also on the design of
safety-related systems for machinery control.
◆
It is the responsibility of the designer of the end product or application to ensure that it is safe
and in compliance with the relevant regulations.
2 Risk assessment
■
When using the safety function STO, be sure to perform risk assessment of the servo system in
advance. Make sure that the safety integrity level of the standards is met.
■
The following residual risks can be present even when the safety functions operate. Therefore,
safety must always be given consideration during risk assessment.
■
If external forces (such as gravitational force with a vertical axis) are applied when the safety
functions are operating, the motor will rotate due to the action of these external forces. Use a
separate mechanical brake to secure the motor.
■
If the servo drive fails, the motor may operate within a range of 180 electrical degrees. Make sure
that safety is ensured even in hazardous situations.
■
The number of rotations and movement distance for each type of motor are listed below.
Rotational motor: 1/6 rotation max. (rotation angle at motor shaft conversion)
Direct drive motor: 1/20 rotation max. (rotation angle at motor shaft conversion)
Linear servo motor: 30 mm max.
Содержание SV660
Страница 178: ...177 6 Gain Tuning Figure 6 18 Example of the waveform...
Страница 359: ...358 10 Application Cases c Click OK d Click Yes...
Страница 360: ...359 10 Application Cases e Click OK f Click No...
Страница 362: ...361 10 Application Cases...
Страница 366: ...365 10 Application Cases 7 2 Controlling the servo operations through the PLC a Create a PLC program...
Страница 370: ...369 10 Application Cases b Add parameters to be monitored to monitor these parameters during PLC running...