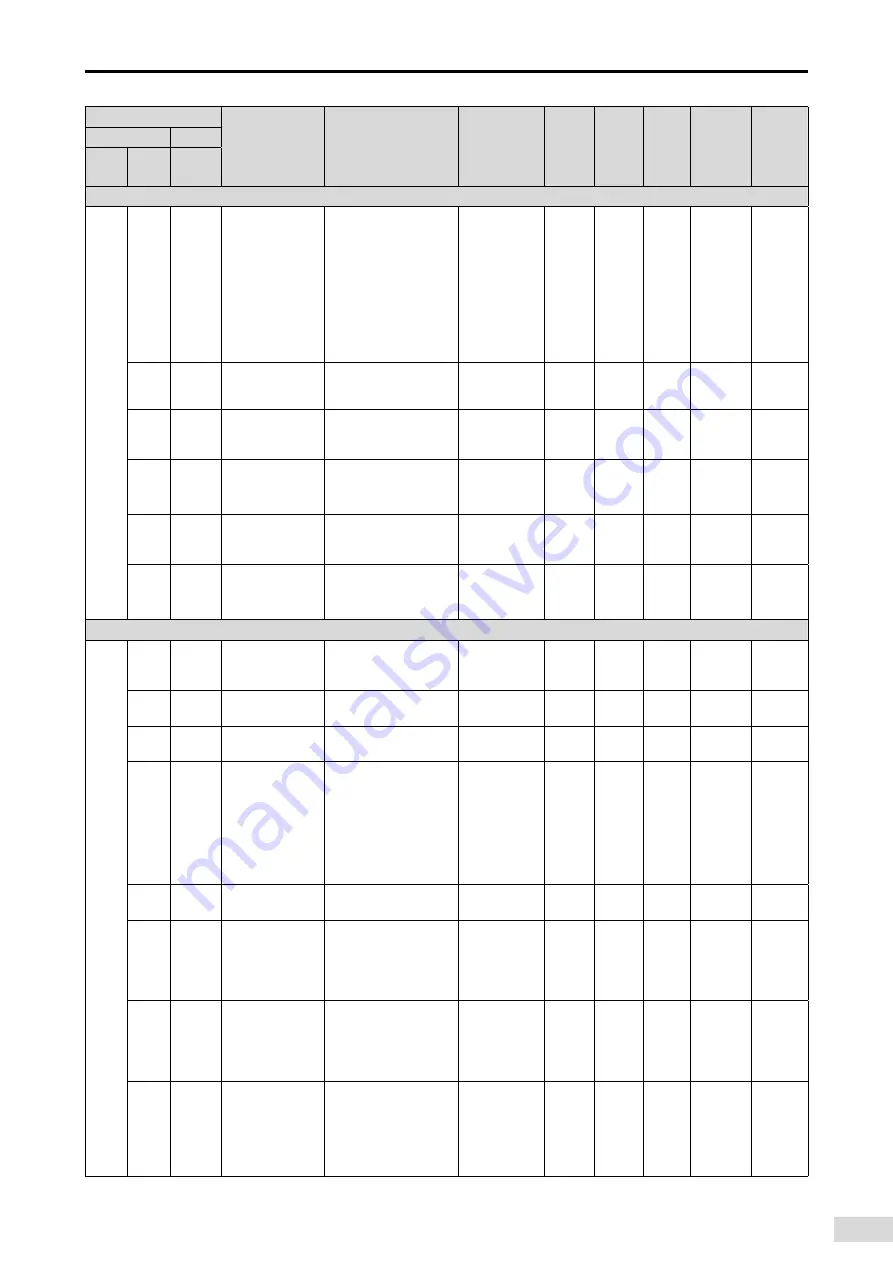
-391-
11 Appendix
Parameter Group
Name
Option Description
Value Range Default
Min.
unit
Width
Setting
Condition
Effective
Time
Hexadecimal Decimal
Group
Index
Code
Para.
No.
2004h/H04 Terminal Output Parameters
2004
01h H04-00 DO1 function
selection
0: No definition
1: Servo ready
2: Motor rotating
9: Brake output
10: Warning
11: Fault
25: Comparison output
32: STO EDM
0–32
1
1
16 bits During
running
Immedi-
ately
02h H04-01 DO1 logic selec-
tion
0: Normally open
1: Normally closed
0–1
0
1
16 bits During
running
Immedi-
ately
03h H04-02 DO2 function
selection
0–32
See the description of
H04-00 for details.
0–32
11
1
16 bits During
running
Immedi-
ately
04h H04-03 DO2 logic selec-
tion
0–1
See the description of
H04-01 for details.
0–1
0
1
16 bits During
running
Immedi-
ately
05h H04-04 DO3 function
selection
0–32
See the description of
H04-00 for details.
0–32
9
1
16 bits During
running
Immedi-
ately
06h H04-05 DO3 logic selec-
tion
0–1
See the description of
H04-01 for details.
0–1
0
1
16 bits During
running
Immedi-
ately
2005h/H05 Position control parameters
2005
05h H05-04
First-order low-
pass filter time
constant
-
0–65535
0
0.1 ms 16 bits At stop Immedi-
ately
06h H05-05
Average filter time
constant 1
-
0–1280
0
0.1 ms 16 bits At stop Immedi-
ately
07h H05-06
Average filter time
constant 2
-
0–1280
0
0.1 ms 16 bits At stop Immedi-
ately
14h H05-19
Speed
feedforward
control selection
0: No speed
feedforward
1: Internal speed
feedforward
2: 60B1 as speed
feedforward
3: Zero phase control
0–3
1
1
16 bits At stop Immedi-
ately
24h H05-35 Duration limit of
homing
-
0–65535
50000 0.1s
16 bits During
running
Immedi-
ately
33h H05-50
Numerator of the
mechanical gear
ratio in absolute
position rotation
mode
-
1–65535
1
1
16 bits At stop Immedi-
ately
34h H05-51
Denominator of
mechanical gear
ratio in absolute
position rotation
mode
-
1–65535
1
1
16 bits At stop Immedi-
ately
35h H05-52
Pulses per
revolution of the
load in absolute
position rotation
mode (low 32
bits)
-
0–4294967295
0
1p
32 bits At stop Immedi-
ately
Содержание SV660
Страница 178: ...177 6 Gain Tuning Figure 6 18 Example of the waveform...
Страница 359: ...358 10 Application Cases c Click OK d Click Yes...
Страница 360: ...359 10 Application Cases e Click OK f Click No...
Страница 362: ...361 10 Application Cases...
Страница 366: ...365 10 Application Cases 7 2 Controlling the servo operations through the PLC a Create a PLC program...
Страница 370: ...369 10 Application Cases b Add parameters to be monitored to monitor these parameters during PLC running...