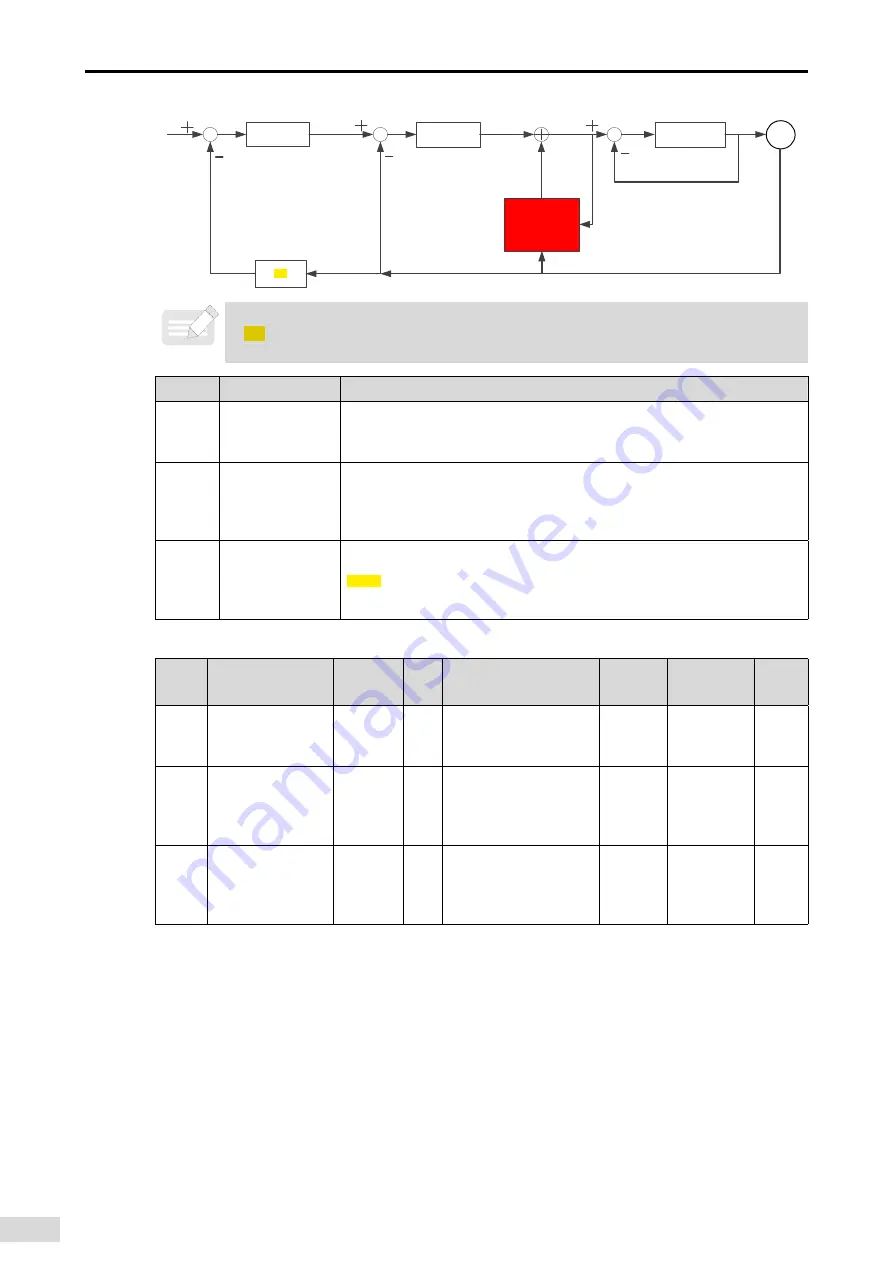
-160-
6 Gain Tuning
Speed loop
control
Current loop
control
Position
loop control
Disturbance
observer
I/S
Motor
NOTE
◆
1/S: Integral element
Para. No.
Name
Description
H08-31
Disturbance
observation cutoff
frequency
The higher the cutoff frequency is, the more easily will the vibration occur.
H08-32
Disturbance
observation
compensation
coefficient
Defines the compensation percentage for observation.
H08-33
Disturbance
observation
inertia correction
coefficient
Set this parameter only if the set inertia does not fit the actual conditions. The
acting inertia is the result of multiplying the value of H08-33 by the set inertia. It is
recommended to use the default value of H08-33.
☆ Related parameters
Para.
No.
Name
Value
Range
Unit
Function
Setting
Condition
Effective
Time
Default
H08-31
Disturbance
observation cutoff
frequency
10 to 1700 1 Hz
Defines the cutoff
frequency for disturbance
observation.
During
running
Immediately
600
H08-32
Disturbance
observation
compensation
coefficient
0 to 100
1%
Defines the compensation
percentage for
disturbance observation.
During
running
Immediately
0
H08-33
Disturbance
observation
inertia correction
coefficient
1 to 10000
1%
Defines the coefficient for
correcting the disturbance
observation inertia.
During
running
Immediately
100
6.5.7 Speed observer
The speed observer is intended to be used in applications with small load/inertia changes. It facilitates
quick positioning through improving the responsiveness and filtering high frequencies.
The block diagram for the speed observer is as follows.
Содержание SV660
Страница 178: ...177 6 Gain Tuning Figure 6 18 Example of the waveform...
Страница 359: ...358 10 Application Cases c Click OK d Click Yes...
Страница 360: ...359 10 Application Cases e Click OK f Click No...
Страница 362: ...361 10 Application Cases...
Страница 366: ...365 10 Application Cases 7 2 Controlling the servo operations through the PLC a Create a PLC program...
Страница 370: ...369 10 Application Cases b Add parameters to be monitored to monitor these parameters during PLC running...