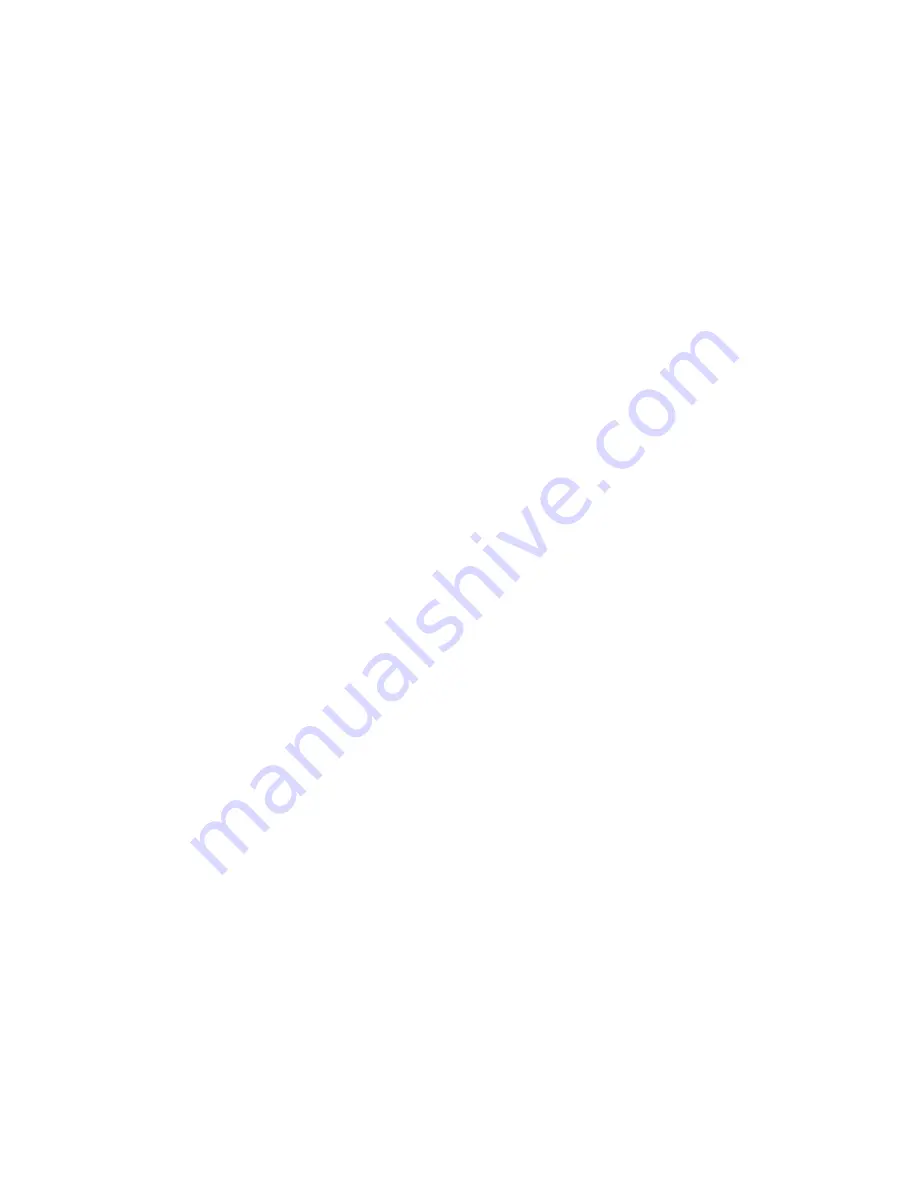
17
Chapter 2: Electronics and operation
The following sections are to be found in this chapter:
-
CC-Pilot
-
Information display
-
Real time clock
-
Operation
-
Operation using the rotary knob
-
Operation using the simulated Number Pad
-
Main menu points
-
Compact menu
-
Comfort menu
-
Com.G@te menu
-
Function numbers and their meaning
-
Configure user menus
-
Select user menus