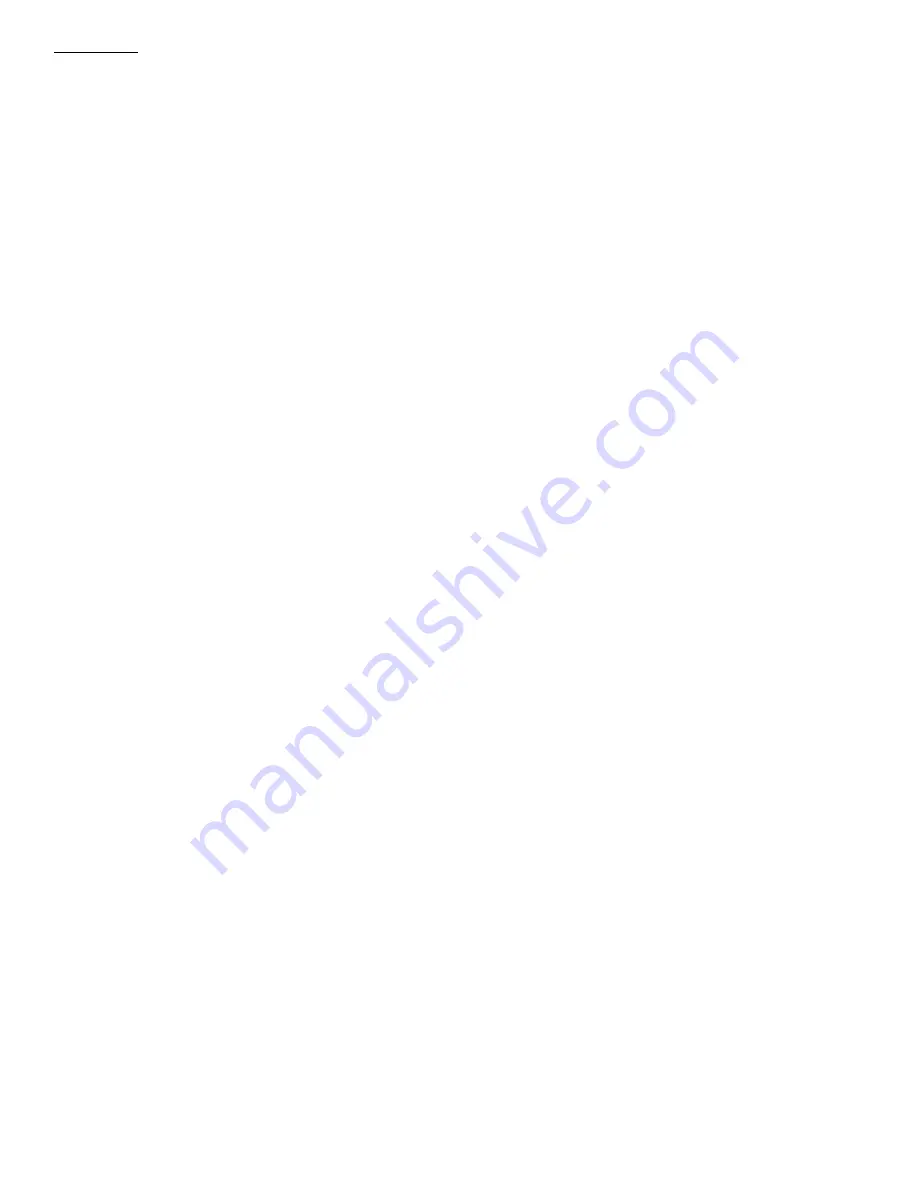
63-4309—2
34
80% of 4000, or 3200 CFM. The return fan is then con-
trolled to maintain its output at 3200 CFM.
A return air mounted static pressure input is available
for monitoring/alarming only. There is no control function
associated with the return air static pressure input.
DISCHARGE AIR TEMPERATURE CONTROL
The W7600 control system allows separate program-
mable setpoints and control bands for discharge air heating
and cooling. The system controls to the cooling setpoint
unless heat mode changeover is enabled. Heat mode may
be enabled by space or return air temperature, as selected by
the user. Heat operation is based on distinct setpoints and
conditions such as morning warm-up, occupied heat mode,
and night setback. Control outputs are available for staged,
floating or modulating economizer, cooling and heating.
With floating control, the system calculates the open and
close time duration of the equipment, and adjusts open and
close time duration to the speed of the motor. For modulat-
ing outputs, the system takes direct control of valve or
damper position. A discharge air low temperature feature is
provided as a general temperature control safety and alarm
point.
Under conditions that require cooling, the system evalu-
ates whether an economizer may be used for outdoor air
cooling before mechanical cooling is energized. Control
outputs are available for air and water economizer. A
minimum position function is programmable with modu-
lating economizer only, while floating control assumes a
mechanical minimum position.
When the economizer is unable to satisfy demand for
cooling, the system will enable mechanical cooling. The
W7600 allows configuration of up to 12 compressor or
unloader stages for mechanical cooling to be sequenced on
and off to maintain discharge temperature. These stages
must be configured into compressor loops to enhance cool-
ing control. A compressor loop includes a compressor
unloader, liquid line solenoid valve and low pressure safety
switch. A maximum of four compressor loops may be
configured.
There are three user programmable options for control
of a compressor loop. The first option is called the
no low
pressure delay
method, and it simultaneously turns on the
compressor and liquid line solenoid valve. As the name
indicates, there is no delay for the low pressure safety
switch, and an alarm is sounded only if low pressure input
falls within a programmable low pressure start delay. With
the second control option, called
low pressure delay type 1
,
the liquid line solenoid valve is opened, but the compressor
is not energized until the low pressure input closes. The low
pressure alarm may still be enabled, based on the low
pressure start delay, which was described above. With the
third option, called
low pressure delay type 2
, the compres-
sor is started and a vacuum is initiated. When the low
pressure switch sends an input signal to the W7600 Control
Module, the liquid line solenoid valve is then energized.
With a multiple compressor/unloader operation and the
lead/lag option disabled, the system energizes Compressor
1 first and sequences through unloader stages on a call for
cooling. Then the system moves on to Compressor 2 and
unloaders. When cooling demand decreases, the unloaders
sequence off first and Compressor 2 sequences off after all
the unloaders for Compressor 1 are de-energized. On a
compressor failure, the affected cooling stage is locked out
but cooling function continues with other loops. User pro-
grammable minimum on/off/interstage time delays are avail-
able for compressors. In addition to staged control, the
system allows floating and modulating control as noted
above. If any system failure occurs, and the pump out
selection was chosen, the system pumps out the compres-
sors when the control shuts down. At the same time, the
remaining outputs are turned off.
The W7600 also provides discharge air temperature
reset upward on a programmable schedule that is selected
from space, return air or outside air. The system incorpo-
rates an unoccupied mode feature to de-energize fan and
cooling equipment. Mechanical cooling safeties and limits
include compressor high pressure, compressor oil pressure,
outdoor temperature cooling lockout and periodic compres-
sor pump out.
Under conditions that require heating, the system con-
trols discharge air temperature by enabling heating equip-
ment. On a call for heating, the system will effect a
changeover to heat mode and energize staged, floating or
modulating heat outputs. In this manner, heat mode may be
enabled by a sensor monitoring space or return air tempera-
ture. Also, heat operation is based on setpoints and condi-
tions of morning warm-up, occupied heat mode and night
setback. Once per minute, the control determines whether
the heat mode or cool mode is required. Minumum on and
off timer for heat and cool must be satisified before a
changeover can occur.
OCCUPIED WARM-UP OPERATION
Occupied warm-up operation can occur when the con-
trol determines that a transition from unoccupied mode to
occupied mode has occurred. The occupied mode determi-
nation can be made from several input sources. The unit is
unoccupied
unless one of the following is true:
• Time clock digital input is configured and active.
• Internal TOD schedules indicate occupied and the
USE_INT_TOD programmable variable is true.
• CNAP network has written occupied to the unit.
• CNAP network has written that a VAV zone is calling
for unit operation.
When the W7600 determines the building transition to
occupied, the warm-up control logic is enabled. A program-
mable delay timer is started to delay the decision to go into
heat mode. This delay is intended to allow the supply fan to
get air flow established before reading the warm-up control
sensor. The warm-up control uses the building space air
temperature or the return air temperature to control the
building heat. When the warm-up input temperature is
below the occupied warm-up temperature setpoint, the
VAV control is placed in the heat mode and the
VAV Box
Open
output is turned on. The discharge air is controlled to
the discharge air heat setpoint. When the warm-up input temp-
erature rises above the se HEAT_HYSTERESIS,
the system changes over to the discharge air cooling mode
and the
VAV Box Open
output is turned off.
PM7600B
OPERATION
Содержание PM7600B
Страница 44: ...63 4309 2 44 NOTES PM7600B PROGRAMMING ...