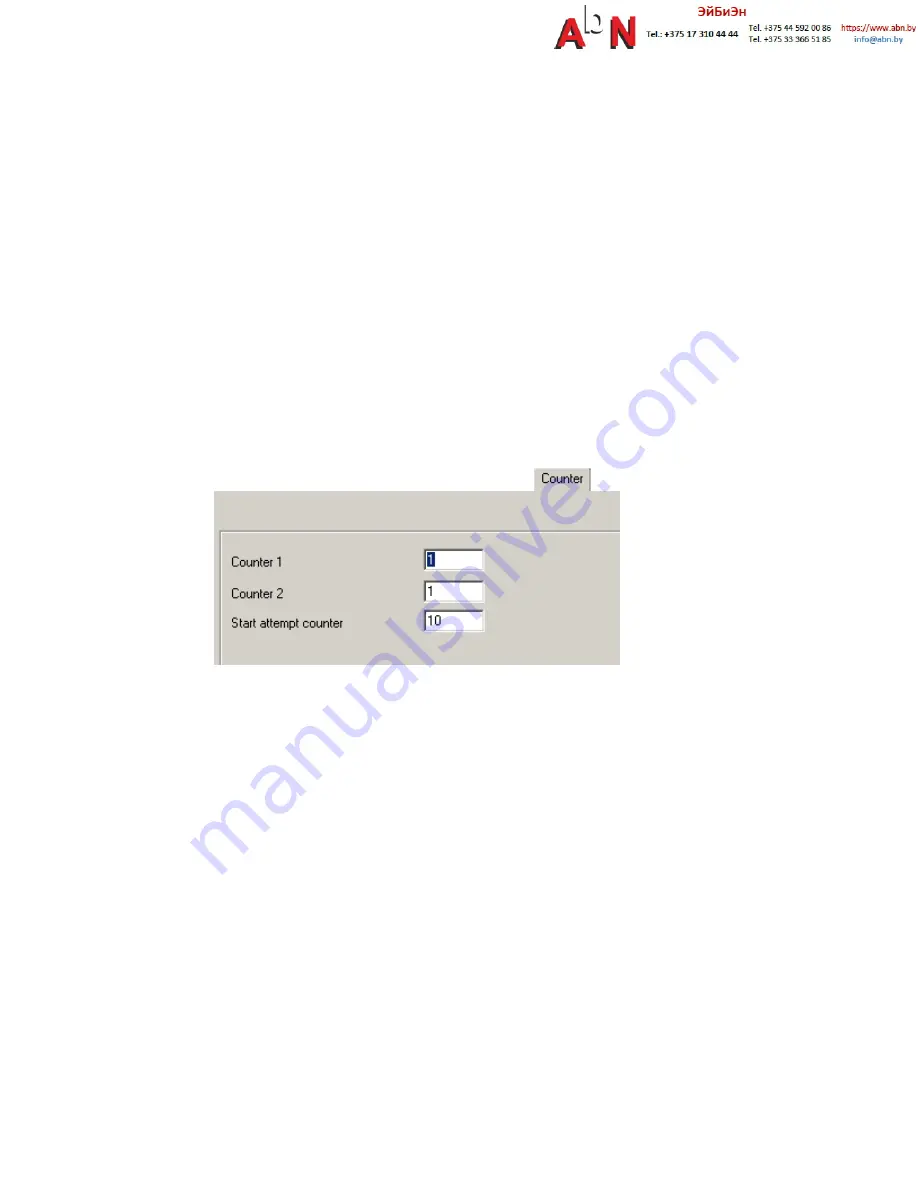
EP OS MOTOR MANAGEMENT SY STEM – INSTRUCTION MANUAL
CHAPTER 5: WinESG
5.
21
Soft starter time:
use on soft starter typical. Transition to by-pass will occur after
this time expires.
Soft stop time:
use on soft starter typical. Transition from by-pass to soft starter
stop control will occur after this time expires.
Under current delay time:
fault or warning is indicated if a current is below under current
threshold for the set amount of time.
Start attempts time:
indicates the allowable time to make the number of start
attempts set in start attempt counter (Counter 3).
5.3.2.6 Parameterization Counter panel
The counter panel provides a means for setting two parameterizable counters: Counter 1 and Counter 2. They are
selectable from 0 to 65535 in steps of 1. Details are available in logic documentation. Counter 3 is used for Start
attempt counter, and it is settable from 1 to 40. This is the number of start attempts allowed within a specified timer
(Start attempts time). Refer to Figure 5-12 for the WinESG parameterization counter panel.
Figure 5-12-: WinESG parameterization counter panel
5.3.2.7 Parameterization Control panel
The control panel provides a means for setting the controls of the local/remote switch, the remote and local devices
and the device behavior In case of fault. Refer to figure 5-13 for the WinESG parameterization control panel.
Содержание EntelliPro ES Series
Страница 2: ...This page was intentionally left blank ...
Страница 8: ...This page was intentionally left blank ...
Страница 182: ...CHAPTER 4 COMMUNICATION EPOS MOTOR MANAGEMENT SYSTEM INSTRUCTION MANUAL 4 45 This page was intentionally left blank ...
Страница 255: ...EPOS MOTOR MANAGEMENT SYSTEM INSTRUCTION MANUAL 6 20 CHAPTER 6 ENTELLIPRO CP3 and CP5 APPLICATION ...