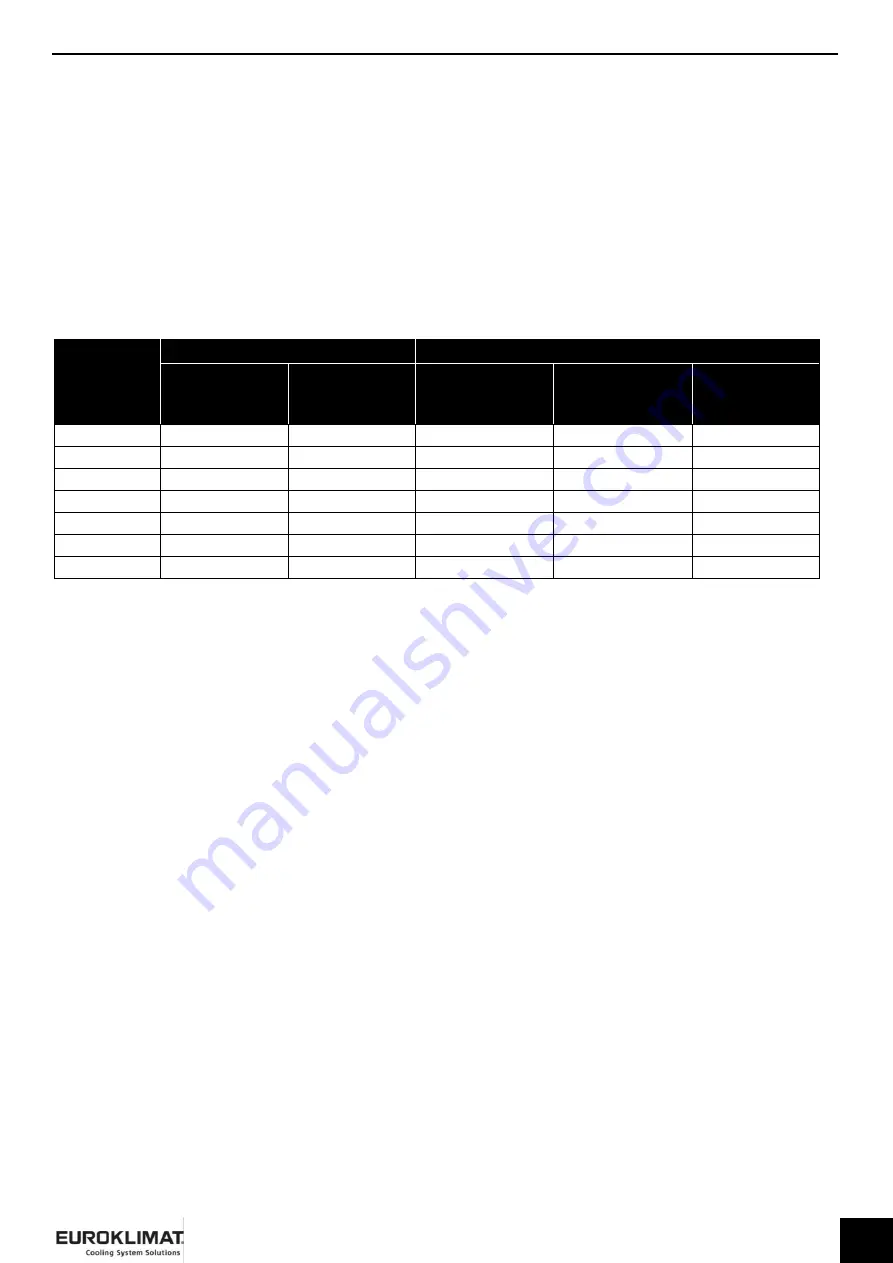
57
www.euroklimat.it
ANNEX B
Provisions for in-service inspections from European Standard UNI EN 378-4
–
ANNEX D
Refrigerating systems and heat pumps
–
Safety and environmental requirements - Part 4: Operation, maintenance,
repair and recovery
In-service inspection
D.1
During the operational life of the system, inspection and testing are carried out according to national regulations.
Information about in-service inspection from Annex D of EN 378-4:2016 can be used where no similar criteria exist in national regulations.
Table D.1
–
In-service inspection
a - The pressure of the system should be above atmospheric pressure for the tightness test.
b - Not for new equipment.
D.2
In-service inspection is carried out after service work that is likely to affect strength, or when a change in use has occurred, or when changing
to another refrigerant at a higher pressure, or after standstill for longer than two years. Components, which do not conform, are changed.
Test pressures higher than appropriate for the PS of the components are not applied.
D.3
In-service inspection is carried out after repair or significant alterations or extensions to the systems or components.
Testing should be restricted to the parts affected.
D.4
In-service inspection is carried out after reinstalling on another site.
D.5
Leak testing of the system is to be performed if serious suspicion of lea
ks is raised. For the purposes of this paragraph, “inspected for
leakage” means that the equipment or system is examined primarily for leakage using direct or indirect measuring methods, foc
using on
those parts of the equipment or system most likely to leak. Frequency of inspection for leakage varies from:
—
once every 12 months for systems with 3 kg or more of refrigerant except for hermetically sealed systems containing less than 6 kg;
—
once every 6 months for applications containing 30 kg or more of refrigerant;
—
once every 3 months for applications containing 300 kg or more of refrigerant.
The systems should be inspected for leakage within one month after a leak has been repaired to ensure that the repair has been effective.
For applications containing 3 kg or more of refrigerant the operator should maintain records on the quantity and type of refrigerant installed,
any quantities added and the quantity recovered during maintenance, servicing and final disposal.
For applications containing 300 kg or more of refrigerant, the operator should install leakage indication systems. These leakage indication
systems should be inspected at least once every 12 months to ensure their proper functioning.
Where a properly functioning appropriate leakage indication system is in place, the frequency of the inspections may be halved.
High leakage rates are unacceptable. Action should be taken to eliminate every detected leak.
NOTE: Fixed refrigerant detectors are not leak detectors because they do not locate the leak.
D.6
Safety devices are checked on site: annually for safety switching devices (see EN 378-2:2016 6.3.4.3.3), emergency signals and alarm
systems; every five years for external pressure relief devices.
D.7
Pressure relief valves and bursting discs are visually checked in accordance with EN 378-2:2016, 6.3.4.3.1, 6.3.4.3.4, and 6.3.4.3.5 and leak
tested annually.
D.8
For unit systems and self-contained systems, in-service inspection is carried out after repairs have been made. If loss of refrigerant is evident
the whole system is leak tested.
D.9
Where piping, piping supports, components and component supports are not insulated, they should be visually inspected. Insulated piping
and components should be visually inspected if the vapour barrier is damaged or if it does not function as intended.
Subclause
Inspection
Test
External visual
EN 378-2:2016,
Annex G
Corrosion
Pressure test for
system
Refrigerant leakage
indication system
a
Safety device check
D.2
X
X
X
D.3
X
X
D.4
X
X
D.5
X
D.6
X
D.7
X
X
D.9
X
b