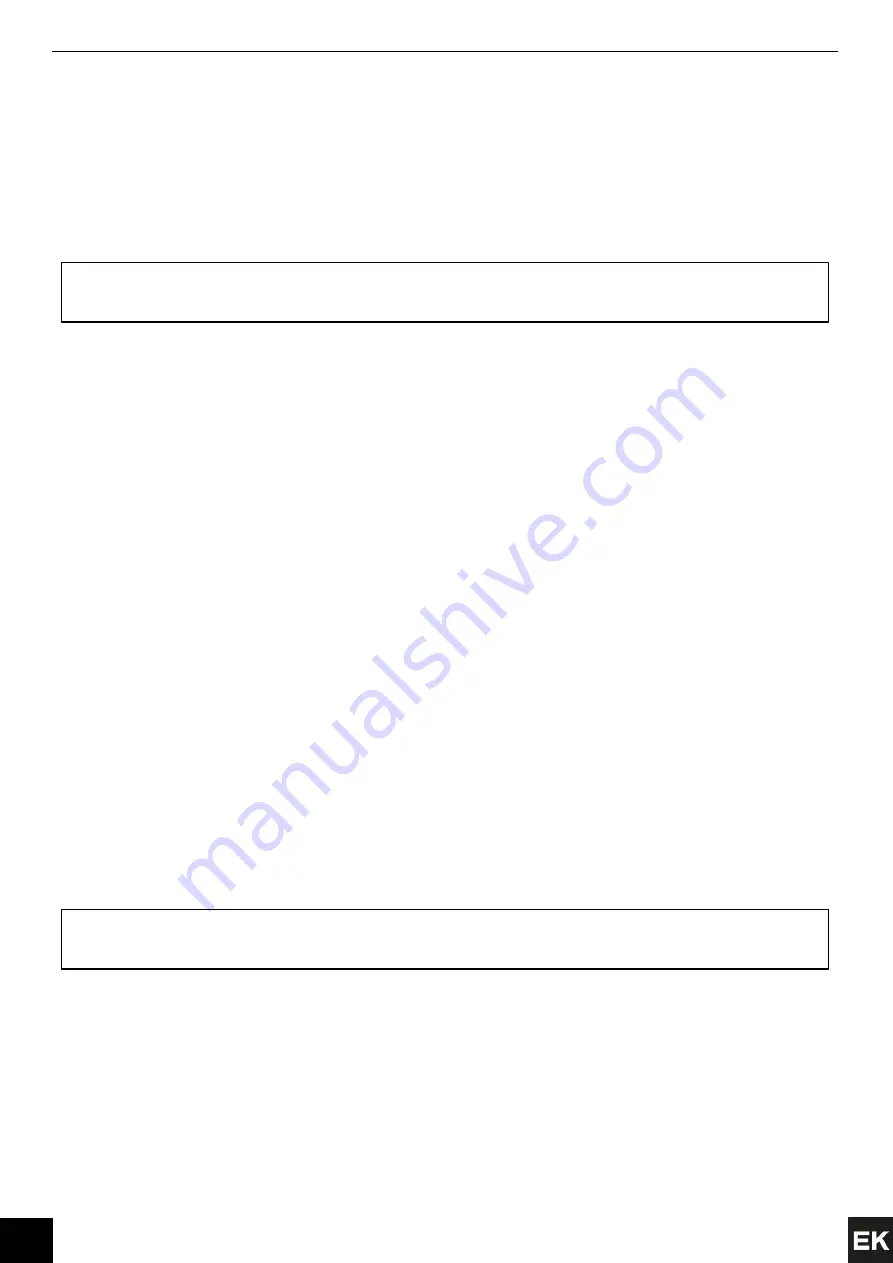
44
www.euroklimat.it
6.0
MAINTENANCE AND FAULTS
6.1
GENERAL INFORMATION AND MAINTENANCE LOGICS
Technological equipment, which is often in constant operation and at times under stressful conditions, always requires maintenance in order to
be able to work in optimum conditions, at full capacity. The most frequent and repetitive operations for keeping the equipment clean and in
working order are grouped under the entry
“
ROUTINE MAINTENANCE
”
while more intermittent and special operations constitute part of what
is called
“
SUPPLEMENTARY MAINTENANCE
”.
General safety rules
Before proceeding with inspections, maintenance and checks, carefully follow the guidelines set out below:
•
check that the master switch is open
(“OFF”
position);
•
check there are no moving parts;
•
comply with the current accident prevention regulations;
•
use suitable personal protective accident prevention equipment (gloves, eyewear, etc.) for all operations.
All operations, except those related to external visual inspections, must only be carried out by specialised, skilled personnel. For operations not
included in this manual, or if in doubt
, contact the Manufacturer’s Tech
nical Assistance Office directly.
For constant efficiency and a long machine operating life, it is essential that the machine undergoes regular checks and maintenance: a detailed
visual inspection of the equipment and general clean are always advantageous for good working.
Relatively simple and cheap inspections and operations come under this category of interventions, which, on the one hand, guarantee good
working over time, and, on the other, make it possible to prevent faults that could later become much more serious, if neglected.
6.2
ROUTINE MAINTENANCE
Obviously, the more care that is taken when carrying out maintenance, the longer the equipment will last and the better the operating
performance will be.
The first and most important maintenance technician is the operator who works directly on the machine
’s work c
ycles. Identifying anomalies
immediately (abnormal noise, different behaviour from usual, unreliable results) could prevent serious damage and expensive repair costs.
There are simple operations, which are not dangerous that all employees can carry out and, if necessary, report the identified anomalies to their
managers or to the Manufacturer’s Technical Assistance Office
.
Recommended activities for operators
The following simple operations, which can also be implemented every day, must be carried out according to the safety rules.
•
inspect the equipment visually from the outside and identify any faults or excessive noise
•
check for alarms on the microprocessor display
•
check that the water inlet/outlet temperatures are normal on the microprocessor display
Maintenance must also be carried out during the foreseen guarantee period and planned systematically f
or the whole of the machine’s
life. Failure to comply with correct maintenance exonerates the Manufacturer from any resulting damage or malfunctioning.
Under no circumstances may operators work on the equipment to solve problems, they are strictly limited to reporting them. All
machine intervention must only be carried out by specialized and authorised personnel.