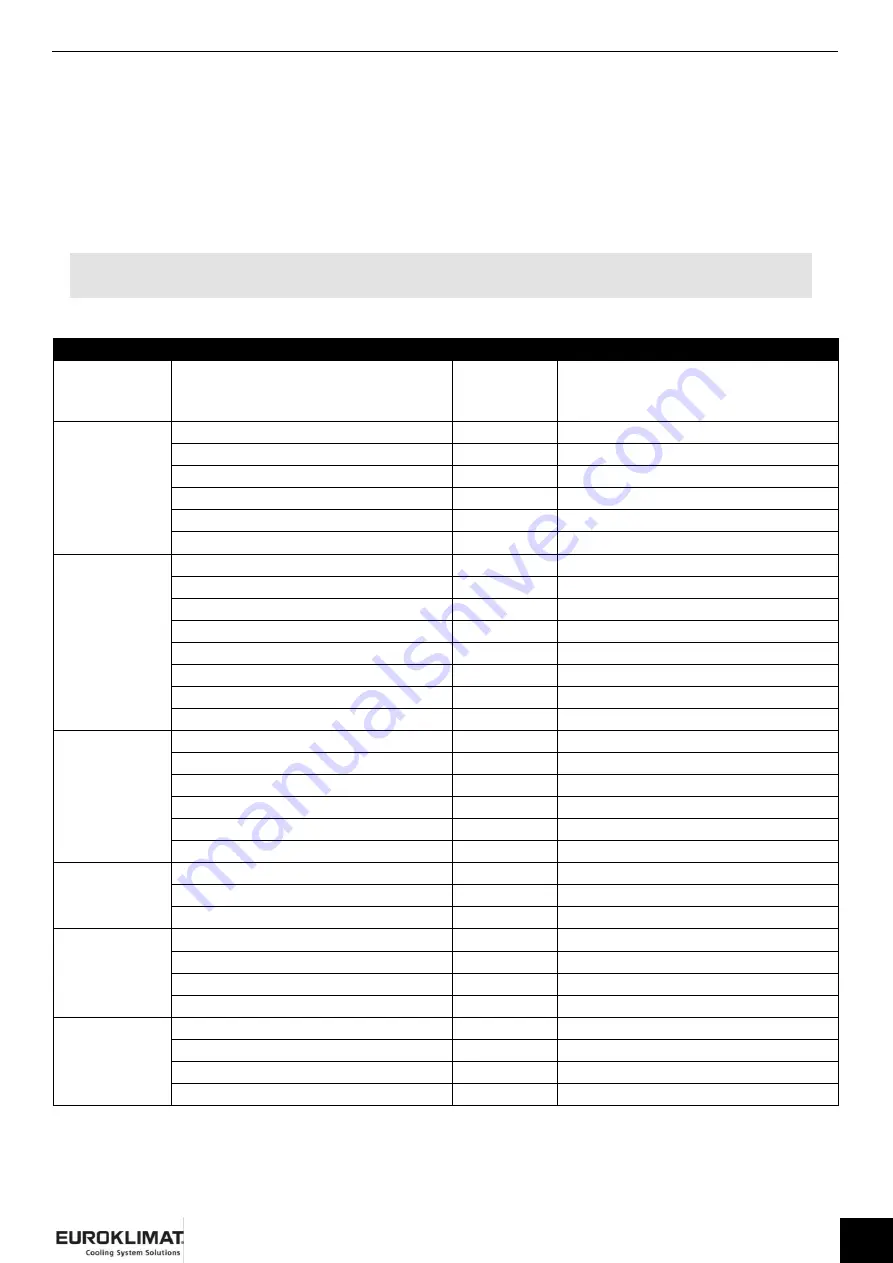
45
www.euroklimat.it
Activities for specialised maintenance technicians
Specialised maintenance technicians must know all of the procedures and correct methods for operating on the equipment (the Safety Manager
must ensure that the person is suitable and has all of the necessary requisites to carry out the work). The following operations are purely
indicative and of a general nature. Each piece of equipment must be assessed within the context of the system in which it is inserted, for the
duration of its use and for the environmental conditions in which it operates.
The Manufacturer is limited to indicating the operations to be carried out and the recommended frequency. Specialised maintenance technicians
must have the necessary skills to work in conditions of maximum safety.
ROUTINE MAINTENANCE
Section
Operation
Frequency
Procedure
GENERAL
Internal visual check of the components
3 months
Visual inspection
External cleaning of the equipment
3 months
Manual cleaning operation
Internal cleaning of the components
3 months
Manual cleaning operation
Inspection integrity mechanical structure
3 months
Visual inspection
Rebooting the unit
after every stop
Closure master switch
(“1”
position)
Final operation check
after reboot
Unit authorisation and visual inspection
COMPRESSOR
Oil replacement
12 months
Specialised operation
Oil level check (if the warning light is on)
3 months
Visual inspection
Inspection vibrations and noise
3 months
Visual inspection
Check adjustments and safety devices
3 months
Check activation safety devices
Check motor insulation
12 months
Check with specific instrument
Check oil filter (if present)
3 months
Visual inspection
Check suction filter (if present)
6 months
Visual inspection
Supply check
3 months
Opening electrical junction box
ELECTRICAL
Check line voltage
3 months
Measurement with ammeter on each phase
Check contactors and thermals
6 months
Visual and mechanical (intervention)
Tightening terminals
6 months
Inspection with device on each terminal
Inspection load absorption
6 months
Measurement with ammeter on each single component
Check ground insulation
6 months
Check with specific instrument
Check hours operation
3 months
Microprocessor reading
AERAULIC
Cleaning condensing coil
3 months
Cleaning wings with bristle brush
Check air flow
6 months
Measurement flow on the exchanger
Check rev regulator
3 months
Microprocessor reading
REFRIGERATION
Inspection working pressures
3 months
Manometer or microprocessor reading
Gas temperature check
3 months
Thermometer or microprocessor reading
Check overheating and undercooling
3 months
Inspection on operation
Inspection potential leaks
6 months
Leak detectors
HYDRAULIC
Filter check
3 months
Inspection and cleaning, if necessary
Inspection circulation pumps
3 months
Noise and potential leaks
Check water flows and cleaning exchanger
6 months
Inspections of flow and pressure drop
Temperature check
3 months
Microprocessor reading
All maintenance must be carried out with the machine at a standstill. Make sure that the master
switch is open (“0” position) and
that there are no moving parts.