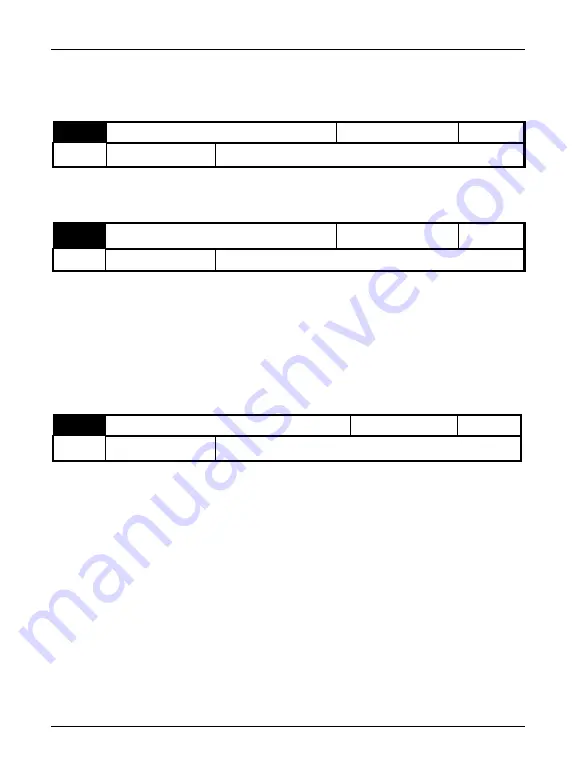
CV3100 series and MINI series high performance general purpose inverter instruction manual
6-56
If the inverter can’t receive correct data during the interval time defined by this
parameter, it will take for communication failure and stop running or maintain the
status according to setting of communication failure action manner.
P8.03
Response delay
Factory setting
5ms
Setting range
0-1000ms
This parameter defines the delay time during the inverter correctly receiving the
information code from PC and then sending out data frames back to PC.
P8.04
Linkage proportion setting
Factory setting
1.00
Setting range
0.01-10.00
This parameter is used to set weight coefficient of frequency command received from
PC by RS485 interface. The actual running frequency is equal to the value off this
parameter multiplying with frequency setting command value received by RS485
interface. More running frequency proportion can be set by this parameter in Linkage
control system .
6.10 Protection parameter
P9.00
Motor overload stall prevention factor
Factory setting
105%
Setting range
30%—110%
In order to carry out effective overload protection for different model motors
,
setting motor overload stall prevention factor reasonably and limiting inverter
allowable output max current are necessary. Motor overload stall prevention factor is
the percentage of motor rated current to inverter rated output current.
When the inverterand motor are at the same power rate, motor overload stall
prevention factor can be set to 100% generally.
When the capacity of inverter is big than motor, the factor setting shall be
reasonable in order to execute effective overload stall prevention to the motor, shown
as the following Diagram: