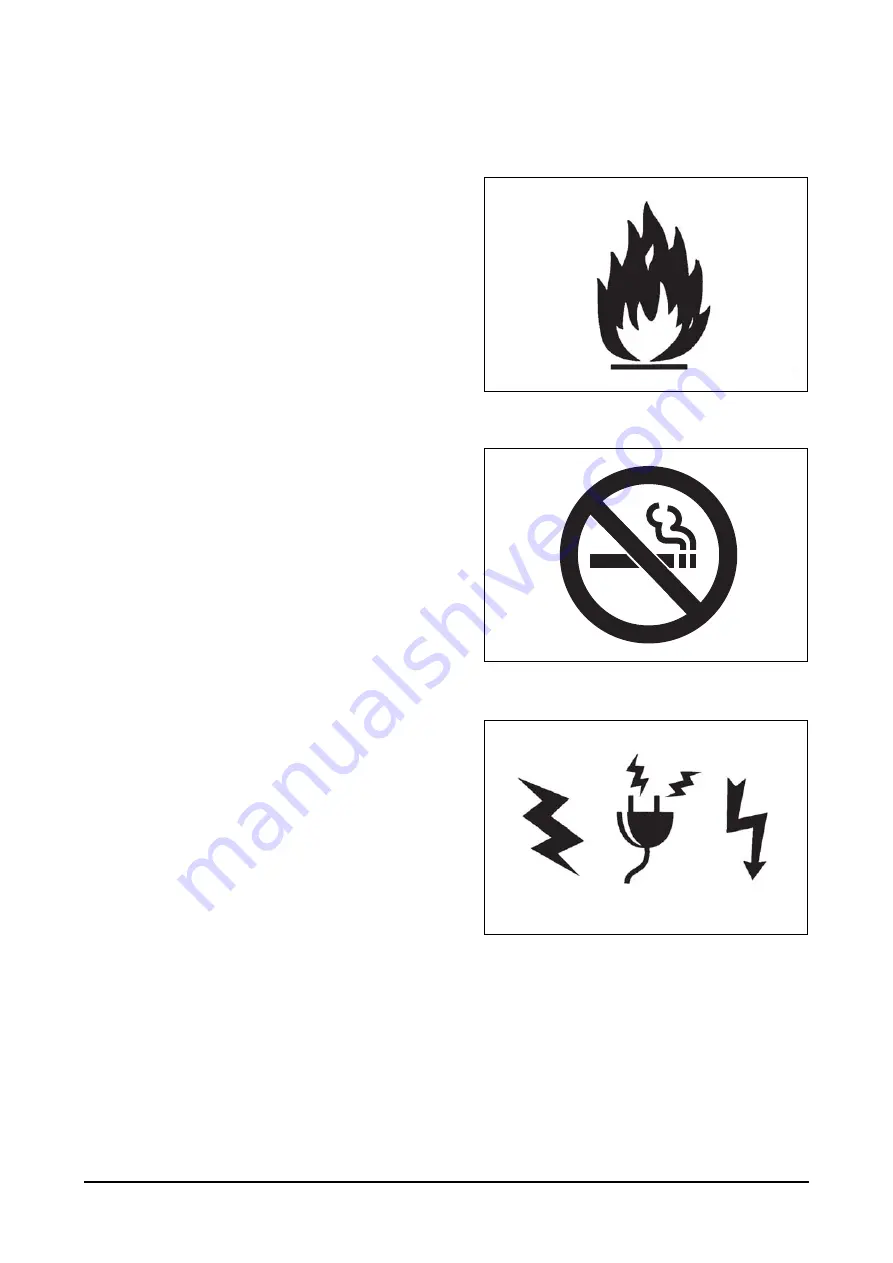
Safety Regulations & Specifications
- 6 -
1.1.8. Handle compressed natural gas safety
Natural gas is highly flammable and explosive and may be extremely cold. The following cautions must
be taken to avoid personal injury or engine damage.
Do not smoke when installing or servicing
the engine or fuel system.
Installation or servicing of natural gas
equipment must only be conducted in well
ventilated, natural gas compatible areas.
Do not install or service equipment in an
enclosed area where ignition sources are
present without ensuring that an
undetected gas leak may be safely
vented without being ignited.
Do not vent natural gas or permit leaks
inside an enclosed area.
Bleed natural gas lines before installing or
servicing any component connected to
the fuel lines.
1.1.9. Venting an operable engine to relieve
natural gas pressure
To avoid personal injury an operable
natural gas engine must be kept in a well
ventilated area away from open flames
and sparks.
If the engine can run, use the following
venting procedure to relive the natural gas
pressure downstream of the shutoff valve.
1) Shut off manual valves on natural gas
supply tanks and main shutoff valve
on natural gas fuel supply line.
2) Start engine and run until it stalls due to fuel starvation.
3) Check to make sure gauge pressure at point on the natural gas fuel line to be vented has been
reduced to zero. If not, repeat step 1) Then repeat step 2).
4) Disconnect vehicle batteries using switch in battery compartment or by disconnecting battery
ground cable.
5) Slightly loosen the CNG fuel line fitting to be serviced in a well ventilated area to allow any
remaining gas to vent.
6) Completely open the fitting that was slightly opened and allow to vent in a well ventilated area.
EB8O2001
EB8O2002
EB8O2003
Содержание GL08K
Страница 1: ...950106 050004EN GL08K GAS VEHICLE ENGINE Operation Maintenance Manual ...
Страница 2: ......
Страница 4: ......
Страница 6: ......
Страница 151: ...Maintenance 145 7 Vehicle wiring harness EH3M5012 Truck engine Bus engine ...
Страница 193: ...Appendix 187 Engine Assembly Bus EJ3OM012 ...
Страница 194: ...Appendix 188 Engine Assembly Truck EJ3OM013 ...
Страница 195: ...Special Tool List 950106 080002 ...
Страница 196: ......