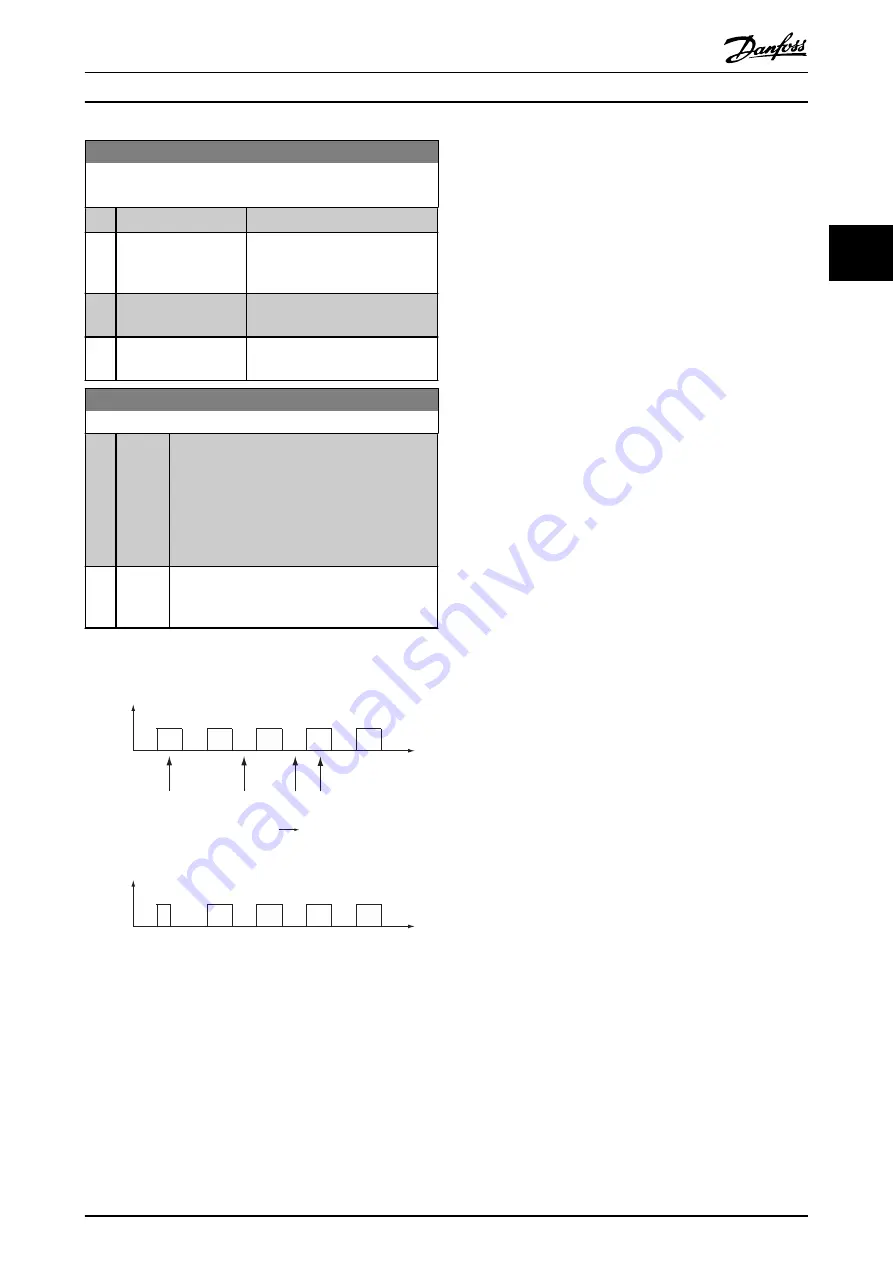
23-08 Timed Actions Mode
Used to enable and disable automatic timed actions.
Option:
Function:
[0]
*
Timed Actions Auto
Enable timed actions.
[1]
Timed Actions
Disabled
Disable timed actions, normal
operation according to control
commands.
[2]
Constant On Actions
Disable timed actions. Constant On
Actions activated.
[3]
Constant Off Actions
Disable timed actions. Constant Off
Actions activated.
23-09 Timed Actions Reactivation
Option:
Function:
[0]
Disabled After an update of time/condition U(power
cycling, setting date and time, change of
summertime, change of Hand Auto mode, change
of Constant ON and OFF, set-up change) all
activated ON actions will be overridden to OFF
actions until passing the next time for an ON
action. Any OFF actions will remain unchanged.
[1]
*
Enabled After an update of time/condition On and OFF
actions are immediately set to the actual time
programming of ON and OFF actions.
To see an example of a reactivation test, see
Timed Action
ON: RUN
OFF: STOP
Power
Cycle
P23-09:
Disabled
Power
Cycle
P23-09:
Disabled
P23-09:
Disable
Enable
Power
Cycle
P23-09:
Enabled
Status
RUNNING
STOPPED
130BB808.10
Illustration 3.8 Reactivation Test Diagram
3.21.2 23-1* Maintenance
Wear and tear calls for periodic inspection and service of
elements in the application, e.g. motor bearings, feedback
sensors and seals or filters. With Preventive Maintenance
the service intervals may be programmed into the
frequency converter. The frequency converter will give a
message when maintenance is required. 20 Preventive
Maintenance Events can be programmed into the
frequency converter. For each Event the following must be
specified:
•
Maintenance item (e.g. “Motor Bearings”)
•
Maintenance action (e.g. “Replace”)
•
Maintenance Time Base (e.g. “Running Hours” or
a specific date and time)
•
Maintenance Time Interval or the date and time
of next maintenance
NOTE
To disable a Preventive Maintenance Event the associated
must be set to
Disabled
[0].
Preventive Maintenance can be programmed from the LCP,
but use of the PC-based VLT Motion Control Tool MCT10 is
recommended.
Parameter Description
VLT
®
HVAC Drive Programming Guide
MG.11.CC.02 - VLT
®
is a registered Danfoss trademark
161
3
3