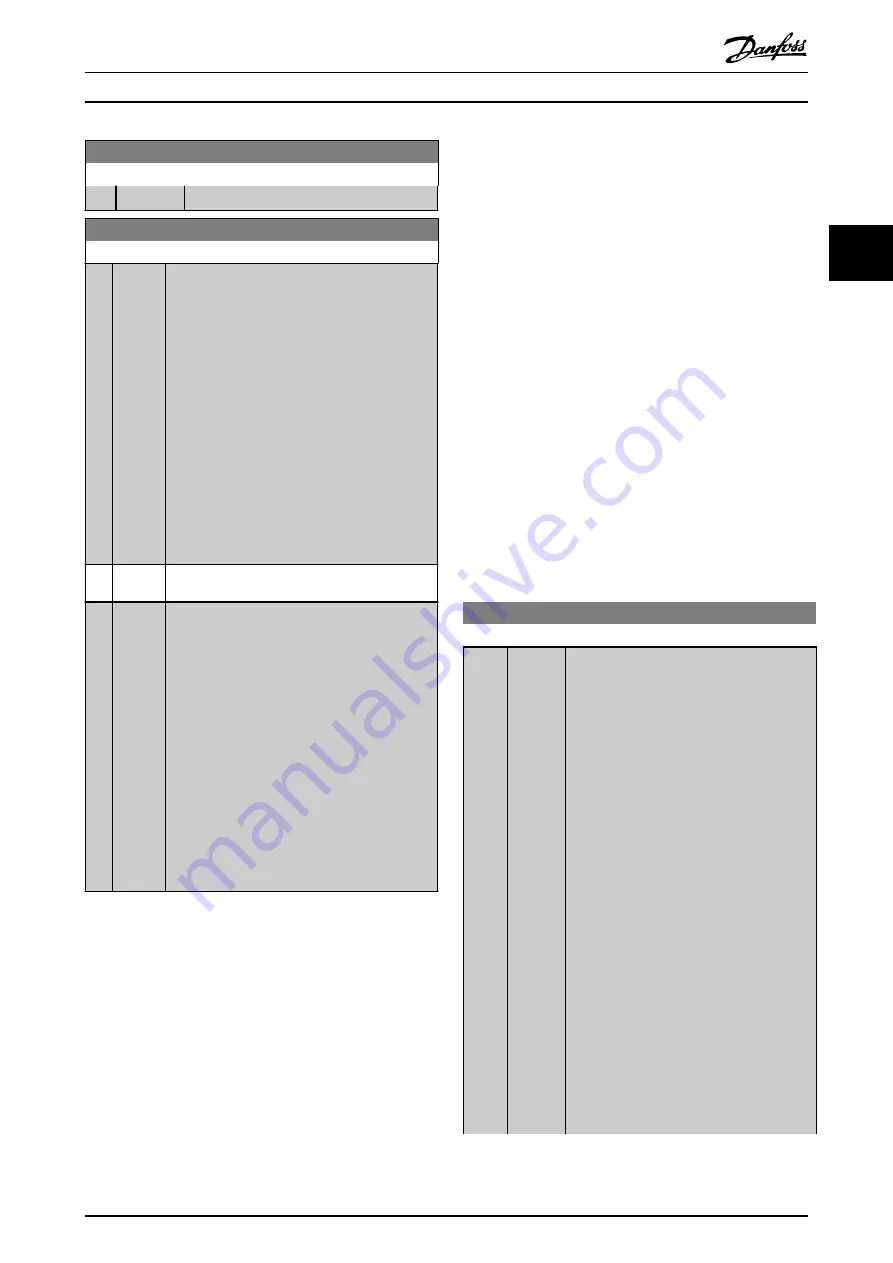
1-72 Start Function
Option:
Function:
[2] coast
1-73 Flying Start
Option:
Function:
This function makes it possible to catch a motor
which is spinning freely due to a mains drop-out.
When
is enabled,
has no function.
Search direction for flying start is linked to the
setting in
Clockwise
[0]: Flying start search in clockwise
direction. If not successful, a DC brake is carried
out.
Both Directions
[2]: The flying start will first make a
search in the direction determined by the last
reference (direction). If not finding the speed it
will make a search in the other direction. If not
successful, a DC brake will be activated in the
time set in
. Start will then
take place from 0Hz.
[0]
*
Disabled Select
Disable
[0] if this function is not required
[1] Enabled Select
Enable
[1] to enable the frequency
converter to “catch” and control a spinning motor.
The parameter is always set to [1] Enable when
= [1] PM non salient.
Important related parameters:
•
1-58 Flystart Test Pulses Current
•
1-59 Flystart Test Pulses Frequency
Important parameters specifically when
= [1] PM non salient:
•
•
•
2-03 DC Brake Cut In Speed [RPM]
•
2-04 DC Brake Cut In Speed [Hz]
The Flystart Principle used for PM motors is based on a
passive measurement at speeds above 2% of nominal
(determined by
1-59 Flystart Test Pulses Frequency
). Below
that speed there are two options:
1.
Either the motor is brought to a halt by using DC
Brake (defined in
,
2-03 DC Brake Cut In Speed [RPM]
or
2-04 DC Brake Cut In Speed [Hz]
).
2.
Change the method of speed and direction
estimation to an active scheme based on sending
out test pules (defined in
and
1-59 Flystart Test Pulses Frequency
).
Current limitations of the Flystart Principle used for PM
motors:
•
The speed range is up to 100% Nominal Speed or
the field weakening speed (which ever is lowest).
•
PMSM with high back emf (>300VLL(rms)) and
high winding inductance(>10mH) needed more
time for reducing short circuit current to zero and
may be susceptible to error in estimation.
•
Current testing limited to a speed range up to
300Hz. For certain units the limit is 250Hz; all
200-240V units up to and including 2.2kW and all
380-480V units up to and including 4kW.
•
Current testing limited to a machine power size
up to 22kW.
•
Prepared for salient pole machine (IPMSM) but
not yet verified on those types of machine.
•
An active measurement function is used to
estimate the speed at very low motor speeds.
This function results in good accuracy in speed
range up to 0-2% of the nominal motor speed.
•
For high inertia applications (i.e. where the load
inertia is more than 30 times larger than the
motor inertia) a brake resistor is recomended to
avoid over-voltage trip during high speed
engagement of the fly-start function.
1-77 Compressor Start Max Speed [rpm]
Range:
Function:
0
rpm
*
[0.0 -
max
output
speed]
The parameter enables “High Starting Torque”.
This is a function, where the Current Limit and
Torque Limit are ignored during start of the
motor. The time, from the start signal is given
until the speed exceeds the speed set in this
parameter, becomes a “start-zone” where the
current limit and motoric torque limit is set to
what is maximum possible for the drive/motor
combination. This parameter is normally set to
the same value as
. When set to zero the function is
inactive.
In this “starting-zone”
is active instead of
to
ensure extra acceleration during the start and
to minimize the time where the motor is
operated under the minimum speed for the
application. The time without protection from
the Current Limit and Torque Limit must not
exceed the value set in
or the frequency converter
will trip with an alarm [A18] Start Failed.
When this function is activated to get a fast
start then also
is
activated to protect the application from
running below minimum motor speed e.g.
when in current limit.
Parameter Description
VLT
®
HVAC Drive Programming Guide
MG.11.CC.02 - VLT
®
is a registered Danfoss trademark
45
3
3